If it's not burning, it's not earning
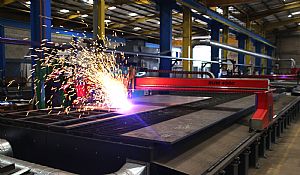
To realise its ambitions of being the UK’s leading independent profiling and processing company, the P.P. Group has consolidated its business interests by bringing its three manufacturing facilities in Salford, Gorton and St Helens, under one roof - a brand new 110,000sq/ft 6 acre site in Oldham. Moving to its new factory in 2017, the £9m investment included a 36m oxy-fuel and plasma cutting cell from Kerf Developments.
The significant investment is testament to the success of a business that has a 5% 'book debt' limit on its client base. By limiting and spreading the risk ratio of its client base, the company has continually evolved to a position that it is now profiling, processing, fabricating and welding beyond 12,000 tonnes of steel every year. To emphasise how central the Kerf RUM4500g oxy-fuel and RUM4500p high-definition plasma cutting machine has become to the strategy for continued growth; the machine is processing over 400 tonnes of steel each month. This equates to almost 40% of the material that passes through the doors of the 100 employee company.
Discussing the installation of the Kerf RUM4500 cell, P.P. Group Managing Director, Mr Peter McCabe says: "In our previous factories we had a 9m by 4m plasma cutting machine for processing steel up to 40mm thick and a 22m by 5m flame cutting machine for materials up to 200mm thick. The machines were more than 10 years old, they were unreliable and this was compounded by poor service and support. Additionally, the machines were expensive to run, not particularly user-friendly and the machine configuration didn't suit pendulum loading. We made the business decision not to bring the machines to the new factory. We looked at replacing them with a more efficient, productive, cost-effective and user-friendly solution. Kerf Developments had exactly what we were looking for."
With plasma and flame cutting being central to business activities, getting the most suitable machine was critical. The bespoke production cell configuration selected by the P.P. Group was a 12m by 3.5m bed with an RUM4500p single gantry 400amp Lincoln Electric high definition plasma cutting head with Ultrasharp cut technology and a 24m by 3.5m table with two RUM4500g gantries, each with four oxy-fuel flame cutting heads – all on a single platform. This single bed configuration has streamlined workflow and improved throughput whilst the 8 oxy-fuel heads have improved productivity by more than 35%.
"Since we installed the Kerf RUM4500 system, the cell has been operating 24 hours a day and 6 days a week, it is a major contributor to our growth. If it's not burning, it's not earning. Prior to the Kerf installation, we didn't have the confidence to sell our capacity as the old machines were inefficient, unreliable and the machine beds were too high. Our business has grown by 10% in the year since we moved to the new factory and the Kerf cutting cell is a major contributor to this growth."
The height of the bed on the previous machines made loading and unloading a challenge for staff. The Kerf RUM system has a larger bed than the previous two machines combined and it is positioned at an ergonomically suitable height that makes loading and unloading convenient for operators. The large bed also allows the company to conduct pendulum cutting, this enables staff to load one plate or unload parts while the machine is cutting another plate. This immediately reduces processing times by 50%. The 12m bed section of the Kerf plasma machine was designed purely for pendulum cutting, as carbon steel plates are supplied in 6m lengths as standard.
"The Kerf system has reduced cycle times by 50% due to the facility for pendulum cutting. The Burny 10 LCD CNC control unit is very easy to use and it makes programming profiles fast and efficient. The kinematics of the Kerf machine combined with the Burny 10 control and the Ultrasharp cutting technology enables us to nest our parts with precision and proximity that wasn't previously feasible. This is reducing our waste material and allowing us to cut more parts from each plate."
"The Ultrasharp technology has also improved surface finishes on cut profiles and this has drastically reduced hand finishing operations. One operator would previously be spending 4-5 hours a day hand finishing parts and this is no longer necessary. Added to this saving, the efficiency of the Kerf machine has reduced our consumable consumption by at least 30%. We cannot praise Kerf highly enough. The service has been exceptional and we have the confidence in the machine and the Kerf support to build our profiling capacity around this machine. The Kerf RUM4500 cell has delivered productivity gains, throughput efficiency, labour and consumable savings and cost reductions. We couldn't ask for anything more from an equipment supplier."