IMC President Launches TaeguTec's New 'Gold Rush' Series in UK
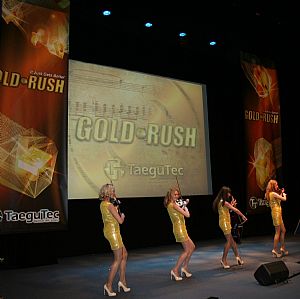
On 21st June 2012 TaeguTec UK launched its new Gold Rush series of cutting tools. Presented at the Birmingham ICC to over 200 customers and distributors by IMC Group President and CEO Mr Jacob Harpaz, the prestigious event proved a huge success.
From the offset Mr Harpaz eluded to the phenomenal success the IMC Group and in particular TaeguTec has achieved, not only prior to, but also since the Berkshire Hathaway takeover in 2008 by investment guru Warren Buffet. Prior to the acquisition, the IMC Group registered increased sales of 20% and 9% respectively in 2007 and 2008. Whilst the global downturn had a detrimental impact on business in 2009, the IMC Group was the only major cutting tool manufacturer to immediately bounce back and record sales in 2010 beyond the 2008 levels. This was credit to a remarkable 44% growth from 2009 to 2010.
Whilst growth at TaeguTec since its incorporation into the IMC Group in 1999 has been overwhelming, the company has been no stranger to success since its inception when it opened the Sang-Dong mine in 1916 and later became known as Korea Tungsten Ltd in 1952. With global growth and investment over the following 47 years, TaeguTec is rapidly emerging as one of the IMC Group's leading brands.
Commenting on the growth at TaeguTec, Mr Harpaz attributes the success to a number of key strategic factors. Relating to the global downturn, Mr Harpaz said: "The world recession forced high productivity on end users. Companies not previously adopting the newest technology were forced into acquiring high specification tooling to improve productivity, reduce costs and remain competitive in the marketplace. Additionally, TaeguTec is manufacturing products that can machine at very high speeds to add to this productivity enhancement. These factors have seen a huge surge in demand for high technology TaeguTec products that support productivity increases."
However, Mr Harpaz was quick to note that the demand for the TaeguTec product range is also credit to the investment in R&D and the strategic set-up of the company's internal teams. As Mr Harpaz continued: "At the IMC Group we are not concerned about our competitors and what their focus is upon. We are our own most fierce competitor and this is how we continually develop leading solutions."
Highlighting how the products are developed at TaeguTec to stay ahead of the competition, the IMC CEO discussed how a product development team 'A' will create a product and as soon as the product is launched, team 'B' with completely new members will strive to improve upon the product created by team 'A'. When team 'B' launch their improved product, a third team 'C' will start the same process over. Each time a new team is introduced, it is with a completely fresh outlook and no team member is re-introduced to the same product. This strategy creates an internal culture of competitiveness that delivers a continuous flow of new and innovative products that are better than the previous development. It is this strategy that notes the company launching over new 1000 products each year.
Industry Specialisation
The ongoing product development at TaeguTec doesn't focus solely on developing new products, but also creating solutions. This is apparent with the company's industry specific engineering teams that are dedicated to delivering machining solutions for the automotive, aerospace, power generation, shipbuilding, rail, medical and general industrial solutions. Internal teams that focus solely upon one sector generates a culture of expertise that is harnessed from long term relationships and partnerships with industry leading OEMs. An example of this has been noted at Hyundai.
The rapidly growing Korean automotive giant has ambitions of overtaking the likes of Toyota to become one of the largest automotive manufacturers in the world. TaeguTec is the cutting tool partner for Hyundai, supplying its manufacturing plants in Korea, India, US, China, Turkey and the Czech Republic. As a cutting tool partner, TaeguTec is committed to providing Hyundai with a 15% year on year cost reduction. It is this industry specific expertise that TaeguTec cultivates for the benefit of its wider automotive customer base. A philosophy and culture the company embraces in all key industry sectors, as more and more manufacturers enter agreements to use TaeguTec as a 'Partner for Cost Reduction'.
Of course, key industry sectors often demand very specialised solutions and to this end, TaeguTec works closely with its IMC Group member companies. As Mr Harpaz continued: "TaeguTec is a 'full line' supplier of cutting tools to all industry sectors. As a group, we have niche manufacturers of specialised tooling that support our core products."
These niche manufacturers include Outiltec, a French manufacturer of standard & special reamers, drills and profiling tools as well as gundrills; Unitac, a provider of brazed and indexable single tube and double tube deep hole drilling tools; Wertec, the tailor made manufacturer of boring & reaming tools; Metaldur, a bespoke producer of internal & external grooving solutions and IT.TE.DI, a specialist manufacturer of PCD tooling for the aerospace industry.
Globalising Success
Since becoming a member of the IMC Group in 1999, TaeguTec has grown almost exponentially. This growth has been built upon a strategy of continually opening regional offices to serve the end users regardless of locality whilst strategically increasing production capacity by opening manufacturing plants in China & India to serve the insatiable appetite for its cutting tools from these emerging markets. This ongoing growth seamlessly continues with the recent opening of a second manufacturing plant in Daegu, Korea. Coupled with remarkable growth levels, this carefully conceived strategy has seen TaeguTec's exports raise from 21% in 1999 to 65% in 2011.
The TaeguTec strategy has reaped rewards in recent years. However, as the company's existing branding states 'It Just Gets Better', TaeguTec is destined to maintain its phenomenal rate of growth. As Mr Harpaz continues: "As the global economy continues to recover, TaeguTec is witnessing significant growth in Korea, Turkey and the BRIC countries. A large element of this demand is because India & China are investing in more advanced machine tools and this goes hand-in-hand with the demand for high quality cutting tools. At present, China is the world's largest manufacturer of automotive components and India will be the 3rd largest automotive component manufacturer by 2015. As the cutting tool demand from these countries increases, TaeguTec has manufacturing plants in the locality to supply the demand."
Product Innovation
Despite TaeguTec's strategy for global growth in key industry sectors and regions, none of this would be a success without the relentless product innovation. Following Mr Harpaz's insight into the global cutting tool industry and where the IMC Group and TaeguTec fit into the equation, the afternoon presentations revolved around the new TaeguTec Gold Rush line of products. Discussing the evolution of insert tooling, Mr Harpaz identified that PVD and CVD coated tooling are clearly the products with the highest demand. Whilst CVD coated inserts are renowned for their high speed machining capabilities and PVD coatings for their edge toughness, the global cutting tool industry has witnessed a marked change in demand between 2006 and 2011. In 2006, CVD coated inserts accounted for 55% of cutting tool demand with PVD coated products at 20%. By 2011 the roles had reversed with CVD tooling accounting for 25% and PVD inserts increasing to 56%.
"With industry demanding the capability to machine at high speeds with cutting tools that demonstrate a high level of edge toughness, our R&D teams have worked hard to deliver a range of products that offer high speed machining with excellent edge toughness. The result is the new Gold Rush range. We are now setting 45HRc as the minimum hardness level that all our cutting tools should be capable of machining at," continues Mr Harpaz.
The result with the new Gold Rush Series is a range of inserts that are finished to a polished standard and then given their unique 'Gold' coating for enhanced performance. The new coating that is available as a CVD or PVD option now delivers a smooth surface that improves chip flow whilst also improving the strength of the inserts.
For turning applications the TaeguTec Gold Rush series now introduces the ceramic and SiN SC10 and AS10 grades for cast iron machining. These new inserts are complimented by the T-Cast series of AS20, TC430 and AB20 grades that are ceramic grades specifically for aerospace machining. Adding to the cast iron turning stable, TaeguTec has also launched its new 'Black Rush' series of CVD coated inserts. The new TT7005 and TT7015 have been created to deliver exceptional performance levels on gray cast iron.
For general steel machining Mr Harpaz introduced the new CVD coated TT8115, TT8125 and TT8135 that have been developed for general machining, continuous and interrupted machining respectively. This range is complimented by the TT9215, TT9225 and TT9235 CVD coated inserts for stainless steel and super alloy applications. More specific to stainless steel is the new TT5080 and TT9080 grades that are PVD coated.
With regards to milling, Mr Harpaz was delighted to introduce the new MillRush, Mill2Rush, Chase2Mill, Fineball and TopDrill Series, whilst more specific applications such as threading, boring and grooving have been extended with the launch of the new TopMini and TopMicro ranges. Closing proceedings, Mr Harpaz assured the audience of customers and distributors that the IMC Group and TaeguTec would always strive to be the benchmark in cutting tool innovations, delivering cost reductions and productivity benefits to its customer base.