Innovations Deliver Results at MACH for ITC
4 May 2012
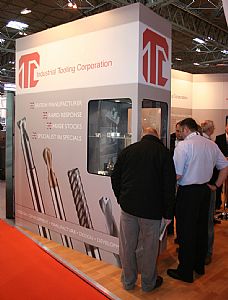
MACH 2012 proved a resounding success for Industrial Tooling Corporation (ITC) as it promoted a multitude of new cutting tools that have been developed specifically for the machining of hard and abrasive materials. At the UK's showpiece event, ITC generated a significant number of high quality enquiries from aerospace, automotive and F1 OEMs as well as from the general subcontract manufacturing sectors.
The industry specific lead generation is credit to ITC's outstanding reputation in the respective markets as well the new products that were shown for the machining of hard steels and aerospace alloys.
Among the new offerings making their debut at MACH and delivering a number of orders and industry specific enquiries was the new 5021 Cyber Series of 5 flute harmonic end mills. The new 5021 Series has been developed to deliver high performance machining and productivity benefits when processing difficult materials. As an integrated partner and preferred supplier to many global aerospace OEMs, Tamworth based ITC has worked strenuously with its customers that are regarded as the benchmark in high technology industries to provide an astounding series of new milling cutters. It is this expertise that strengthened the company's reputation and made the stand a sought out area for aerospace and F1 OEMs visiting the show.
The new 5021 Series is a straight shank, square end centre cutting range with a radical new flute geometry for staggering material removal rates. The solid carbide 5021 is manufactured from ultra wear resistant micro grain carbide that is Cupro coated to enhance tool life and machining stability. With a long length that offers additional reach benefits for the user, the cutters demonstrate stability and rigidity that far exceeds competitor products. This is credit to the unequal flute spacing that reduces machining noise and vibration by eliminating the harmonic effect of the cutters.
Also generating major interest levels at MACH was the new 6051 Cyber Series of End Mills. The impressive 6 flute series of cutting tools has already made an impact on productivity and tool life for many aerospace OEMs and F1 manufacturers. Like the 5021 Series, the 6051 is also a long length, straight shank solid carbide cutter with an unequal flute spacing and Cupro coating.
The geometry of the 6051 Series has been tirelessly tested to provide end users with a long reaching cutter that eliminates problems inherent in long series cutting tools. The right hand helix and cutting series is available in 6, 8, 10, 12, 16 and 20mm diameters with each diameter offering the option of a square end, 0.5, 0.75 or 1mm radius. The various radius options serve to further enhance tool life and eliminate potential chipping in extremely difficult applications. The respective cutting diameters have a machining length of 18, 24, 30, 36, 50 and 60mm with an overall length from 75 to 150mm. These dimensions have been designated for each diameter to ensure optimal performance for each individual cutter.
For machining intricate profiles, pockets and complex 5-axis components in extremely hard materials up to 65 Rockwell, ITC was also pleased with the feedback for its new ball nosed cutters. The 2152 short series and 2162 long series have been launched to give outstanding machining performance to mould & die and general engineering machine shops working with hard materials. The two flute solid carbide ball nosed cutters are centre cutting with a straight shank and short length of cut for the processing of intricate forms and cavities in hard steels.
Showing these new cutting tools along with a range of established products, ITC was also pleased with the response it received for the Widia series of hole making products. Widia's drilling and tapping series are now available from ITC since the companies signed a distribution agreement in 2011. Complementing ITC's cutting tool range, the Widia products are a welcome addition to the ITC stable.
Further innovations on the ITC stand that drew interest at MACH was the range of Air Turbine Spindles for increasing the capabilities of machine tools. The Air Turbine Spindles on show demonstrated that with simple installation, a machining centre can be retrofitted to deliver spindle speeds up to 90,000rpm for high speed machining applications such as drilling, milling, slotting and engraving to enhance cycle times and surface finishes.