ITC Brings HSM to Fanuc With Bolt-on Spindle Units
11 December 2013
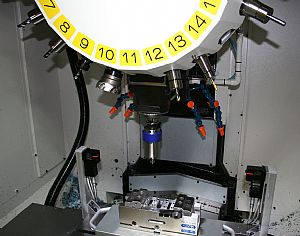
Strategic partnerships between machine tool vendors and manufacturers of ancillaries such as cutting tools, coolants and workholding equipment are increasingly commonplace. The latest relationship that has proven beneficial for both suppliers and most importantly the end user has been struck up between Industrial Tooling Corporation (ITC) and Fanuc Robotics.
The Coventry based machine tool manufacturer recently retrofitted a high speed spindle from Air Turbine Technology (ATT) to a 3-axis Robodrill machining centre to increase spindle speeds from the standard 10,000rpm to 50,000rpm. Supplied by ITC, the ATT 625 high speed spindle is so easy to retrofit to a machine tool, it was an apprentice at Fanuc that installed the spindle in a matter of hours.
The machining centre that serves as a demo machine and test bed at the Fanuc facility has given end users the option of working with a powerful high torque spindle for large diameter cutting tools whilst simultaneously providing an extremely high speed option for light cutting at high feed rates with the ATT spindle. Conducting customer demonstrations, the ATT spindle has reduced cycle times beyond 50% by introducing HSM strategies to parts that are otherwise machined conventionally.
Discussing the benefits of the retrofitted ATT spindle on the Fanuc machine, Fanuc Robomachine's Sales Manager, Mr Nigel House comments: "Combining the ATT spindle with the Fanuc Robodrill gives the end user a powerful high torque machine for optimal material removal rates whilst the high speed spindle provides a lower torque, high speed option for running small diameter tools at high rpm. So, for general machine shops that run the occasional HSM job, we have the perfect fit."
Capable of accommodating cutting tools with a maximum shank diameter of 6mm, the ATT unit is fully integrated into the Fanuc machine tool with the air supply line running through the spindle. Furthermore, with the utilisation of solenoids, a stop block and M-codes, the high speed unit runs in harmony with the machine tool and its CNC control unit.
Concluding upon the installation of the ATT spindle from ITC, Mr House continues: "The ATT spindle enhances the machine performance whilst the cost effective bolt-on unit runs at high speed. This bolt-on addition will prolong the life of the machine spindle."
Whilst ITC's Technical Engineer, Mr Andy Boyles who has been working with Fanuc comments: "The ATT spindles are extremely flexible units that can be retrofitted to most machine tools. In the case of Fanuc, there is also the potential for the spindles to be retrofitted to their robotic cells. The recently formed relationship, not only enables Fanuc to offer extremely high speed machining up to 90,000rpm, but it provides us with the opportunity to show customers the potential of the spindles and the Fanuc machine tools. Furthermore, we can provide Fanuc and its customers with cutting tool solutions that are the best fit for the machine tool as well as the high speed spindles."
"Whilst the spindles can come in handy for 'the occasional HSM job' it is ideal for customers that have specific long running jobs that involve machining with small diameter tools. Utilising the High RPM spindle can reduce cycle times by 3 or 4 times on occasion. At the same time, even on a machine with a high RPM spindle as original equipment, utilising the ATT spindle avoids running the machine spindle flat out for long periods, thus extending the spindle life and saving money. Rebuilding an original high RPM spindle can be very expensive, which makes the outlay on an ATT spindle very modest by comparison."