ITC Delivers Material Benefits for Oil & Gas Specialist
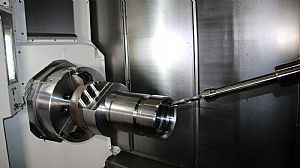
Bucking the trend during the prolonged downturn in the oil & gas industry, Chappell Engineering has just had the most successful four years of its 45 year history. Four years ago the Stonehouse subcontractor moved to a new facility and since moving, the company has invested over £5m in new technology.
The investment includes a mixture of five XYZ machining and turning centres, two Doosan Puma turning centres and nine Mazak machines. The Mazak investment includes five MY Series turning centres, two Integrex i400S sub-spindle machines and a Nexus 510 machining centre. The jewel in the crown is the latest addition, the UK's first installation of the new i800 Vari-Axis. When specifying the i800, Chappell Engineering demanded an extremely robust, precise and flexible platform that would perform on difficult-to-cut oil & gas materials. The Mazak engineering team and Chappell agreed the machine should be specified with a CAT50 dual contact spindle configuration. It is here that Industrial Tooling Corporation (ITC) came to the fore with its BIG KAISER face and taper contact toolholders.
Manufacturing anything from one-off to batches in excess of 500, the 14 employee company machines oil & gas materials from ally-bronze and 316 and 410 stainless through to 625 and 718 inconel and super duplex. The success of Chappell Engineering has arrived from realising that flexible machine tools capable of one-hit machining are vital to productivity, but most important is the 'get it right first time' approach.
As Production Manager, Mr Frank Phillips says: "Our work is all about high precision, high value parts. We achieve productive machining times from extremely capable machine tools. However, precision, rigidity and getting the tight tolerance jobs right are more critical factors for us. For example, a typical billet could cost upwards of £500-1000 and we often get parts nickel plated at £1000 per part. With a material cost beyond £2000 before we start machining; many finished parts could have a residual valued of beyond £5,000 to £10,000. So, the short term expense in machine tools and tooling will reap long term benefits for our business."
It is this philosophy that demanded the CAT50 dual contact spindle and subsequently a complete tooling solution from ITC. "We needed maximum strength and rigidity from Mazak, as we wanted to run the machine at the boundaries of its capability. When it came to sourcing toolholders with dual face and taper contact, the BIG KAISER range from ITC was the only solution that would meet our demands. Nobody else had high-end dual contact back-ends but ITC. We were familiar with the quality of the BIG KAISER brand and we haven't been disappointed."
The Gloucestershire company tooled all 40 positions on the new i800 Mazak with back-ends from ITC.
"The ITC engineer recommended a series of BIG KAISER hydraulic toolholders, heavy duty toolholders and ER collets. The i800 also has a trunnion table that can be used for 1m diameter turning and Neil Vine from ITC even supplied heavy duty CAT50 turning tool holders and turning tools for the machine. In the 6 months since installing the Mazak i800, the dual contact BIG KAISER toolholders have demonstrated astounding rigidity. This rigidity is the bedrock of our impeccable precision levels. Consequently, this rigidity has also improved tool life, surface finishes and productivity to such an extent that we have set about implementing the BIG KAISER toolholders throughout our machine shop."
The Mazak i800 is now primarily tooled with ITC supplied cutting tools that include a full range of robust BIG KAISER back-ends with highly productive 63 and 80mm diameter face mills and 6 to 20mm diameter end mills from WIDIA as well as a variety of WIDIA indexable insert turning tools. With regard to specialist tooling lines, ITC's Neil Vine has also applied the BIG KAISER BCV50 Mega 20N long series of tool holders for reaching into deep bores and milling and drilling difficult to access features.
This access is particularly prominent on the Mazak i800 where parts up to 1m diameter require drilling and threading. A recent example is an 800mm long rectangular gate valve for the oil & gas industry that consisted of a 250mm diameter turned feature at the centre of the valve. This turned protrusion required side drilling and threading at a depth of 275mm. To reach this depth and provide sufficient clearance of the workholding fixtures, the drills and subsequent threadmills were used with the 300mm long BIG KAISER BCV50 Mega 20N long series toolholder.
The subcontractor has now acquired a number of BIG KAISER BCV50 Mega 20N long series toolholders for machining difficult to reach features on large components. The extended hydraulic toolholders have been chosen for their astounding rigidity and concentricity when machining particularly hard materials. One new project to machine super duplex female test sub risers for use at the base of an oil well required cross drilling and a milled flat on the Mazak Integrex i400. Located at the base of a 274mm deep bore, the drilling depth was an additional 110mm - taking the hole to a total depth of 384mm. The 300mm long BIG KAISER hydraulic chuck with a C6 Capto back-end was used with a 150mm long drill to maintain a run-out precision of less than 5 microns. With the drill, back-end and 300mm toolholder all supplied by ITC to provide such staggering concentricity levels; it's blatantly obvious why the company has opted for the quality of the BIG KAISER brand from ITC.
Concluding on this, Mr Phillips continues: "This female sub riser is a large billet that requires nickel plating in the bore, which takes the cost of the part beyond £2000 before any machining takes place. To use anything other than the very best toolholders and tools would be ridiculous. Very few companies have invested in the robust and precise machine tools, toolholding and tooling like Chappell Engineering. This investment level enables us to take on work that other subcontractors will shy away from. Investing in the very best technology from XYZ, Doosan, Mazak and ITC with its BIG KAISER and WIDIA brands is what continues to make us very successful through what has been a difficult period for the oil and gas industry. Our investment strategy will continue and ITC and BIG KAISER will certainly be part of our plans as we move forward."