ITC Installs New Rollomatic Grinding Centre
5 February 2014
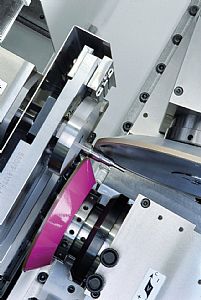
As part of its continual investment program, which has seen Tamworth based Industrial Tooling Corporation (ITC) invest over £1m in new machine tools in the last 12 months, the company has now taken delivery of its latest acquisition, a Rollomatic NP5.
Adding to the Anca GX7 and four Walter Helitronic grinding centres delivered through 2013, the new Rollomatic NP5 is a direct replacement for a Rollomatic 148P4 CNC grinding centre purchased in 2005. Commenting upon the latest acquisition, ITC's Production Manager, Mr Kevin Ford says: "The new Rollomatic is the latest addition that demonstrates our ongoing commitment to our policy of equipment renewal. The policy ensures we maintain our investment in leading edge technology and the new Rollomatic offers many improvements in both time cycles and quality levels achievable in comparison to the previous machine."
Whilst the new acquisition is part of an ongoing renewal strategy that carries the philosophy of maintaining ITC's position as a benchmark in cutting tool technology and innovation, the new Rollomatic NP5 machine has also brought a wealth of benefits for ITC.
In comparison to the previous Rollomatic 148P4 that had a maximum tool diameter capacity of 12mm, the new addition offers a 25mm diameter capacity that allows ITC to produce larger tools on the machine. This improves scheduling and capacity for ITC and streamlines production of its larger diameter cutting tools. Furthermore, with a built in Fanuc control with Rollomatic software, ITC can now draw tool profiles direct on the machine as opposed to previously working off-line and sending the tool profile to the machine. Additionally, with a touch screen display and Rollomatic's Nano-Grind Software, the new grinding centre is very easy to use and set-up.
The new NP5 incorporates a re-designed pick and place Rollomatic robotic loading system. This is not only faster and easier to set-up with only a few parameter changes in the software, but it also offers a larger tool capacity of 20mm diameter by 300mm long. This allows larger diameter batches to be run in automatic mode, should the need arise. The NP5 also improves synergy between other machines at ITC, as the loading system now uses pallets that are common with four of the company's other CNC tool and cutter grinder machines. This allows for the easy flow of urgent batch work when required.
Another benefit of the NP5 over the previous 148P4 machine is that it has a programmable C-axis. For ITC, it provides the potential to grind flats and conduct thread grinding operations that were beyond the realms of the previous machine.
Commenting upon the improved precision and ability to maintain process stability, Mr Ford continues: "We have purchased the automatic Marposs in-process gauging option and this enables unmanned running of very close tolerance work and allows us to achieve higher batch tolerance than was previously possible, all with minimum intervention. This is permitted as the Marposs system measures the cutting tools mid-cycle and automatically compensates the machine parameters for the next part."
During the installation and set-up process, the Marposs system recorded a one micron tolerance band over an unmanned 12 hour shift. It is this level of process control that will enable ITC to guarantee the quality of its cutting tools in the future.
Concluding on the installation, Mr Ford says: "The new machine slotted straight into the space vacated by the original machine, utilising the original coolant feed to the centralised coolant system. This enabled a short period of down time from the original machine being decommissioned to the new machine being up and running. The NP5 has slotted straight into our production facility and it has improved productivity, capabilities and also quality. These are all parameters we demand from our new machine acquisitions to ensure we are the benchmark in cutting tool technology."