ITC Invests in New Grinding Technology To Extend Tool Production
17 December 2017
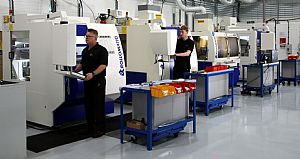
In 2016 Industrial Tooling Corporation (ITC) extended its manufacturing facility by over 50%. Now, the Tamworth cutting tool manufacturer has invested well over £1m in state-of-the-art manufacturing equipment to extend its product ranges and enhance manufacturing capacity, productivity and the remarkably high-quality standards the company maintains.
The investments at the leading UK cutting tool manufacturer includes two Rollomatic grinding centres, a centralised Vomat microfiltration coolant system, a Haimer balancing machine and also an Action Super Abrasives (ASA) wheel dressing machine. The new equipment was delivered in September and has been fully operational since October.
The Rollomatic machines include the new ShapeSmart NP5 blanking machine, ITC’s third Rollomatic precision cylindrical grinding machine. Ideal for preparing tool blanks, the NP5 has an integrated 3-axis robot loader for automated and lights-out blanking of rotary tool shanks from 0.025 to 25 mm. Alongside the ShapeSmart NP5 is the new Rollomatic GrindSmart Nano 6, the UK’s first Nano 6 installation. This high precision 6-axis grinding center has been designed for the high-performance production of micro-tools a diameter range between 0.03 – 2.0 mm.
With innovative hydrostatic technology, the GrindSmart Nano 6 achieves concentricity tolerances below 0.001mm while the integrated robot loader can accommodate up to 1000 tools. The two Rollomatic additions will enhance capacity and productivity whilst the Nano 6 in particular, will enable ITC to extend existing ranges with precision diameter offerings as small as 0.1mm diameter.
Commenting upon the installation of the two Rollomatic machines, ITC’s Managing Director, Mr Peter Graves says: “The two Rollomatic machines will increase our capacity levels in line with business growth. The third blanking machine, the NP5 can run around the clock to meet the ever-increasing demand for our product ranges whereas the Nano 6 is an micron precision grinding centre for processing tools below 2mm diameter. This will enable ITC to extend existing product lines to sub 3mm diameters in line with customer enquiries. It will also allow us to investigate the feasibility of introducing new micro tool ranges.”
To ensure optimal conditions, ITC has also installed a centralised coolant system from Vomat. Now linked to all grinding centres at ITC, the temperature controlled Vomat coolant system guarantees coolant is maintained at a constant and cooled temperature in all grinding centres with ultra-fine filtration. The high-end Vomat system will extend grinding wheel service life and further enhance the surface finishes of cutting tools, which in turn will extend the overall quality and performance of the already impeccably high-quality cutting tools.
Also driving the ongoing improvement in productivity and performance is the new ASA wheel dressing machine. In the first couple of weeks since installation, there has been a dramatic improvement in grinding wheel service life and surface finishes on tool faces have also improved. These enhancements are also a result of the Haimer Tool Dynamic wheel balancing machine that now sees ITC balancing grinding wheels on all of its grinding centres.
“With the additional manufacturing footprint, we not only have the space to install production machines, but also invest in technology that will augment our ongoing commitment to customer services and product quality. We will continue ordering high-tech machine tools through the remainder of 2017 and beyond,” concludes Mr Graves.