ITC is no bore at A&M EDM
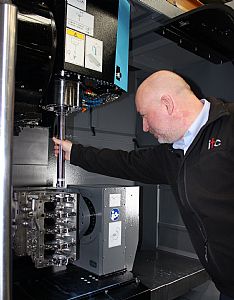
A&M EDM Ltd is an engineering solutions company always striving to maximise its service to clients in the aerospace, motorsport, automotive, marine, medical, rail, defence and general subcontract sectors. To achieve this, the West Midlands company has invested in technology from 3, 4 and 5-axis machine tools, EDM wire and spark erosion and laser welding that is comprehensively supported with cutting tools from Tamworth manufacturer Industrial Tooling Corporation (ITC).
The Smethwick manufacturer has played a proud role in the Ventilator Challenge and it has more than 57 CNC machines on the shop floor as well as a host of accreditations and awards. Like many subcontract manufacturers, A&M EDM machines a variety of materials that include stainless steel, mild steel, aluminium, inconel, titanium and exotics with a variety of production demands from bespoke one-offs and short runs through to longer run batches for its customers – and ITC is always on hand to support with its cutting-edge tooling solutions.
One reason that ITC sets itself apart from rival cutting tool vendors is the ability to provide specialised solutions with unparalleled support. So, when A&M EDM developed a new project re-manufacturing engine blocks for classic vehicles, the company turned to ITC’s BIG KAISER specialist Mr Simon Yeomans. While Simon was at A&M EDM on another application they asked for a double check on the high profile engine block which needed to be 100% correct. The BIG KAISER expert from ITC introduced A&M EDM to the BIG KAISER app that walks customers through the best route to a solution for every application.
Discussing the introduction of the App, ITC’s Mr Yeomans recalls: “I introduced the shop floor engineers to the BIG KAISER app and we went through the simple process together. The first step is to identify the process you want to undertake, such as rough boring, fine boring central or fine boring peripheral. Once we selected fine boring peripheral, we then had to select the applicable boring head, the bore diameter, the material to be machined, the spindle size and the bore depth or the overhang of the boring bar. From these easily identified parameters, the App calculated the cutting data and also identified the required insert for the task. On this boring task, the App recommended a 0.3mm radius insert as well as the cutting data – the results were very impressive.”
Following the success of cutting the piston bores, ITC was subsequently asked again for support on the same project, this time for machining the five-bearing crank bore. A&M EDM Director Gary Surman is an autosport enthusiast and when he re-designed one of the early series Mini engines for track sports, the engineer turned to ITC for support when boring critical cylinder bores and the crank bearings bores.
On the shop floor at A&M EDM and looking closely at a five-bearing engine, senior engineer Paul Fox said: “We have to line bore all the bearings, which has to be done in one go. The challenge with this is machining two different materials. We have to machine aluminium and steel in a single operation and they both require different cutting speeds. This means you are cutting from one material to the other intermittently, so it’s a case of getting not only the cutting tool but the speeds and feeds right to achieve both the precision and surface finish.”
Discussing the project ITC’s Simon Yeomans says: “A&M EDM are long-term customers of ITC cutting tools as well as longstanding users of BIG KAISER boring equipment. So, with the new project, A&M contacted ITC to discuss the application and the material. I created a drawing of the process, which involves lots of extensions on the boring head.”
Specifically, the project required a boring reach of 340mm with the facility to precision machine 49mm diameter bores. This required five high-quality steel boring bar extensions, three 60mm length extensions and two 40mm extensions. ITC’s Simon Yeomans applied the BIG KAISER peripheral boring head with the ability to machine from 41mm up to 74mm diameter by using different sized cartridges that securely bolt to the side of the boring bar.
With such a long bore and multiple extensions, the question of stability arises. Regarding this, Simon Yeomans says: “There is no doubt that this is a very tricky bore to machine. We have to cut to different materials over a long length with lots of extensions, so this really is not a normal boring application. However, the BIG KAISER system is the industry-leading brand for boring technology and regardless of the extensions, the process is extremely secure. The only issue with running a boring bar of this length is that we have to slow the cutting speeds. Additionally, the customer requires a very close tolerance throughout the bore, and this has to be achieved with exceptionally high-quality surface finish.”
Referring to the adjusting mechanism on the BIG KAISER peripheral boring head, ITC’s Simon continues: “BIG KAISER boring heads are well designed with a nice large adjusting dial. So, once you unlock the boring bar, the customer can turn the dial to adjust the boring head. The larger adjusting increments on the boring head are 0.1mm with smaller increments being 10µm and we can then adjust the vernier scale resolution to just the precision down to 1µm.”
Discussing the challenges of insert grade, Simon continues: “With the machining of aluminium and steel in a single process, we have carefully reviewed the operation and selected a general coated K10 insert grade that is capable of effectively machining both steel and aluminium materials. In this particular instance, we are literally just scraping the steel and predominantly cutting aluminium. So, we are essentially cutting half a hole and cutting very lightly into the steel using inserts with a sharp corner radius of 0.1mm.”
Of course, such precision boring on critical features on an engine demand the utmost in process stability. Referring to the part that is machined on a Hurco VMX42Ui machining centre, Simon states: “The entire boring assembly in the machine is supplied by BIG KAISER and the nice thing about this Hurco machine is that it is a new machine with a BIG-PLUS Spindle. This enables us to implement a BIG-PLUS back-end that connects directly to the boring tool, extensions and the boring head. The BIG-PLUS system is a face and taper dual contact system that provides unparalleled levels of precision, stability and repeatability. If the boring bar is taken out of the machine and then put back in, it will be back in exactly the same position, making this a very effective solution.”
Using a BIG KAISER boring head to undertake the task, Paul Fox says: “We use quite a lot of cutting tools from ITC for several reasons. Firstly, they are local to us so they can support our needs and they also keep a high level of stock on the shelf, so we can pretty much get everything we need by the next day.”
“On this engine project alone, we have a lot of ITC tools. We are using the BIG KAISER boring system as well as a complete range of ITC end mills, drills and thread formers - they really are supplying the majority of the tools for this project.”
Concerning backup and support, Paul Fox continues: “ITC are very supportive. They are always available on the end of the phone and they frequently visit to ensure that everything is running smoothly, and our needs are met.”