ITC Makes it Plain Sailing To Success for Moat House Eyewear
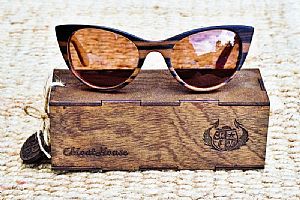
When Nick and Sam Clarke decided to leave the rat-race of daily life, the husband & wife team moved to a picturesque moat-house in the sleepy village of Appleby-Magna near Tamworth. When left with an abundance of oak from the fallen limb of a tree in the grounds of The Moat House, the couple felt the high quality wood was too good to burn and set about finding a more eco-friendly solution. The innovative pair came up with the concept of manufacturing high-end, hand crafted sunglasses from the fallen tree - a concept that has now evolved into a booming cottage industry.
From the most unlikely of settings, Company Director at Moat House Eyewear, Mrs Sam Clarke comments: "We were chopping wood for the fire and at the same time, discussing possible ideas for a business. Nick is a carpenter and extremely talented at crafting wood, but we didn't want to produce anything bulky like cabinets - so we opted for the niche market of wooden sunglasses. From developing the concept in March 2013, we spoke with various suppliers of machinery to progress the project, but one issue we had was cutting the recess for the glass lenses to sit precisely into the frames. That was until a chance meeting with Industrial Tooling Corporation's (ITC) Managing Director, Mr Peter Graves."
The Moat House prides itself on being part of the great British manufacturing revival by internally producing all elements of the glasses from arms and frames through to lenses. This is done with precision machines and a glazing lab all sourced from UK suppliers and manufacturers. Sourcing from UK manufacturers only is a philosophy the company has retained since it was founded in March 2013 and throughout the concept period that brought the trendy eyewear to market in April 2014.
With only a handful of global manufacturers of handcrafted wooden eyewear, the Moat House prides itself on its eco-friendly credentials that see it cut the frames and arms with a laser processing machine. Whereas alternate manufacturers use 5-axis machining centres and cut the eyewear from a solid block of wood, the Moat House method ensures there is no wasted wood. This is because Moat House Eyewear cuts its frames and arms in thin strips and laminates and cross-bonds the glasses to produce more robust, aesthetically attractive and fashionable eyewear. However, an issue arose for Moat House when the laser machine couldn't carve the precision recess into the bespoke frames. This is where ITC stepped in. As Mrs Clarke recalls: "We knew Peter at ITC from the local pub and we approached him about our manufacturing problem. From there, Nick worked closely with the ITC engineers to develop a cutting tool with the correct dimensions, geometries and angles to carve out the recess. The result is an extremely precise and productive V-grooving tool that has been developed by the engineering team at ITC and is bespoke to our exact needs."
The innovative couple have designed and produced a unique jig for clamping the frames during manufacturing. This works in harmony with a retro-fitted hand-held drill that now delivers a remarkably precise lens seating for each and every pair of glasses. When developing the V-Groove cutting tool, Moat House Eyewear was remarkably fortunate to have a manufacturer of precision cutting tools on its doorstep. What's more, with ITC's Tamworth manufacturing facility being local, Moat House Director, Mr Nick Clarke could liaise with ITC engineers on a frequent basis to develop the concept tool.
However, this project wasn't just about producing a V-Grooving tool with a pre-defined diameter and groove width. As Nick Clarke takes up the story: "We are effectively using a precision jig to clamp the hand-held drill in place, so we can process the grooves with the ITC V-Groove tool. As well as tool dimensions, the ITC engineers had to consider the rigidity of the fixturing system, the speed and torque of the drill, the cutting depth and also the properties of the wood. Whilst ITC is a specialist in cutting the most difficult materials known to engineers; their knowledge of processing wood was also astounding. We cut Ebony Makassar, a very dense wood that can rapidly burn through cutting tools; but ITC also considered this factor and generated geometries that can rapidly cut through the wood whilst providing an excellent finish within the lens seat. Furthermore, the V-Groove tool is produced from solid carbide, so tool life is exceptional. We've now been running the same cutter for over two months and due to the combination of geometry and material incorporated in the tool, it hasn't lost its sharp edge by machining hard wearing wood."
Where Next For Moat House..
The unique new line of fashionable eyewear from Moat House Eyewear has only been available since April 2014, and already the company has an established distributor supplying the cultured classes of Knightsbridge among other upmarket areas. The next step will be to exhibit at an exhibition in Paris that is specifically for the optical industry and particularly the fashionable side of the sector. This rapid uptake of the trendy new eyewear now means that the husband and wife team are running a booming business 24/7 and already looking at expanding the business. If you are interested in reviewing the Moat House range of fashionable eyewear products, please visit www.moat-house.com