ITC Offers Universal Turning Grade
3 February 2015
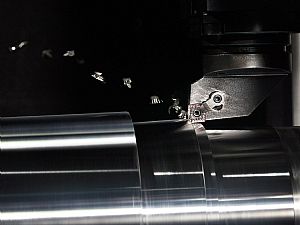
Manufacturers turning a wide range of materials face extreme challenges daily. Machinists understand that the most efficient machining parameters for their cutting tools often means a compromise between speed, feed and cutting depths. To take the guess work out of this, Industrial Tooling Corporation (ITC) is now offering the new WIDIA Victory™ family of turning inserts.
The new line from ITC provides a range of new geometries and grades that extend your parameters by delivering excellent chip flow that results in smooth machining, improved efficiency and extended tool life. For difficult-to-machine materials like Inconel and Rene in complex aerospace applications or cobalt-chromes and high-alloy stainless steels in precise medical applications, the new WIDIA Victory FS geometry is a ground, high positive design best used in finishing tasks where surface finish and minimizing part deflection are critical. Precision grinding, proprietary nose geometry and optimised edge treatment result in an insert that retains its high-quality cutting edge with minimal heat generation and good chip breaking at finishing parameters. The high rake angle reduces cutting forces and also reduces built-up edges.
The new FS line is available with a WS10PT grade, which is a high-performance PVD series. This grade utilises a two-layer coating that increases coating integrity and reduces depth-of-cut notching to increase productivity and consistency. All inserts in the WS10PT grade undergo a post-coat treatment to increase compressive stress and improve edge toughness. This delays built-up edge and results in longer tool life. The WS10PT is available in other geometries including the UR geometry.
Stainless Steel Performance
The WIDIA Universal Roughing (UR) geometry from ITC is specifically designed to increase roughing and medium turning performance in stainless steels and steel workpieces. Its unique chip breaker and rake profile design breaks chips without excessive cutting forces that result in edge breakages. Its positive rake angle further reduces cutting forces while improving depth of cut notching resistance. Together with a multi-layer coating that includes a ZrCN top coat for both extended performance and improved wear identification, the result is the ability to increase speed or feed rates efficiently, increasing productivity and reducing cycle times.
Also available in the Universal Roughing geometry are the WP15CT, WP25CT and WP35CT grades that particularly improve performance on steel workpieces. Emphasising an excellent combination of toughness and cutting performance, the WP15CT is universally applicable on all finishing, medium machining and light roughing steel operations, wet or dry, interrupted and non-interrupted.
The new WP25CT is best applicable on all medium to light roughing operations, wet or dry on interrupted and non-interrupted cuts whereas the WP35CT is the best choice on all roughing and heavy roughing jobs that are interrupted or non-interrupted. These new grades also feature the ZrCN top coating and proprietary post-coat treatment that reduces friction and improves edge toughness as well as functioning as an excellent wear indicator.