ITC Showers Subcontractor in Success
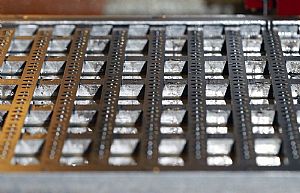
Since its inception in 1984, the Fabricon Group has been involved in the production of aluminium showering systems; something that later led Managing Director Mr Mark Bushdyhan to buy shower manufacturer Autumn UK. Whilst shower manufacture remains a major aspect of the Fabricon Group, the company now provides 3D computer design, prototyping & testing and full scale plastic part production as well as a wealth of bespoke projects.
With its longstanding expertise in plastic production and in particular aluminium manufacture, the Fabricon Group is a specialist in the delivery of high quality shower cubicles and stair lift components. However, it was the machining of extruded aluminium boxway for stair lifts that led the Ashton-Under-Lyne company to aluminium cutting tool specialist Industrial Tooling Corporation (ITC).
Conducting a large on-going project with a renowned stair lift manufacturer, Fabricon was witnessing poor surface finishes and chatter when machining the boxways. As a company that prides itself on its quality and aesthetically pleasing product ranges, Fabricon trialled ITC cutting tools and in particular the 2041 Cyber Series with a geometry developed specifically for machining aluminium. The 2041 range immediately eradicated the tool chatter and improved tool life whilst significantly increasing the speed and feed rates to provide considerable productivity improvements.
Commenting upon the introduction of ITC cutting tools, Fabricon, Production Manager Mr Ryan Bushdyhan comments: "We tried numerous tools with indifferent results. Then the ITC representative offered us the 2041 Series, the results have been outstanding. We cannot quantify tool life or performance based on the quantity of parts. This is because one end mill will be running for months with no deterioration in surface finish or material removal rates."
Following the successful implementation of the 2041 Series of end mills, Fabricon trialled the Widia line of VDS drills from ITC on black steel bar strips that are part of the rail system for stair lifts. The 7.4mm diameter pre-thread holes that are 6mm deep were drilled with remarkable ease. So much so, that Fabricon has drilled over 22,000 holes with a single drill. This astounding drill life was followed by a Widia M8 VariTap from ITC that has threaded over 7380 holes.
As Fabricon machines 15,000 of these parts each month with four threaded holes in each component (a total of 60,000 holes per month), the company has consistently achieved these tool life levels for both the drill and the tap.
This consistently high performance level is matched by a Widia VDS 9.3mm diameter drill that precedes an M10 VariTap on similar components produced from bright mild steel. With 15,000 bright mild steel parts processed each month consisting of two threads per part, the company drills and taps 30,000 holes with M10 threads. In this instance the VDS drill processes over 21,500 holes whilst the VariTap consistently achieves 3240 threads.
Commenting upon this, Mr Bushdyhan says: "The tool life of the VDS drills is staggering, especially as we plunge drill at a speed rate of 1m/min. We haven't broken a drill yet. The quality of the drills means they are always changed through wear as opposed to breakages. For a company that drills such a high quantity of holes, this tool life consistency and the confidence we take from the performance of the drills is of great reassurance to our machine shop staff. Furthermore, it eliminates any unnecessary tool changes and the downtime associated with continuous tooling changeovers."
With the success obtained from the ITC 2041 Series of end mills and the Widia line of VDS drills and VariTaps, Fabricon requested an ITC specially designed T-Slot cutter that was manufactured at the company's Tamworth facility. The T-slot cutter was required for a specific batch of parts for an architect business. To produce the 30,000 T-slots in 606 Aluminium, ITC developed a T-Slot cutter with an 8mm neck, a 12mm width and a height of 2.6mm. Commenting upon this, Mr Bushdyhan says: "We ordered 5 cutters as the 30,000 slots had to each be 35m long. We did the complete job with just two cutters. Like the end mills, drills and taps, the ITC special range of cutting tools have given us exceptional tool life and productivity levels."
"We have tried numerous tooling vendors down the years with indifferent results. The ITC range has been nothing short of phenomenal. The tool life, consistency, component quality and productivity rates have all improved significantly and this has reduced our tooling costs and non-cutting times. To obtain all these benefits from a cutting tool supplier that can offer us a complete range of products has been a huge benefit to our business," concludes Mr Bushdyhan.