ITC's New Spin On Micro-Machining AT MACH With High Speed Spindles
30 January 2016
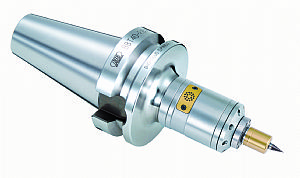
When considering the purchase of a CNC machine tool, it becomes apparent that selected options are focused on specific applications. The machine tool is designed to run a pre-selected range of tool types and sizes that are based on factors such as horsepower, accuracy, flexibility and speed. Now, with the arrival of the BIG KAISER Air Turbine Spindles, Industrial Tooling Corporation (ITC) will be changing the rules at MACH 2016 on Stand 5220.
At present, high-end CNC machines are achieving 60,000rpm to facilitate micro machining with small-diameter cutting tools. These speeds bring balance and dynamic run-out issues that are difficult to manage when using large tool-holders. By shrinking the rotating portion of the spindle, the user improves control of run-out and balance. This is where the new spindle speed increasers can be applied. They are much smaller and weigh substantially less than a typical machine spindle. The largest turbine assembly in the new BIG KAISER RBX line has an effective diameter of just 75mm. The entire speeder weighs just 5kg. The light weight RBX allows operators to focus on the dynamic run-out and balance issue that makes high-speed micro machining difficult.
The BIG KAISER air-powered spindles at to be shown MACH 2016 use compressed air to drive a turbine and develop much higher spindle speeds than a conventional machine spindle. An instant benefit is that the machine spindle doesn’t rotate when running a speeder, so it incurs no wear and tear. Furthermore, the use of air pressure as an energy source eliminates problems associated with the heat generated when a machine tool spindle runs near its maximum speed for prolonged periods. Without any heat build-up, the BIG KAISER air-turbine spindles can operate continuously during the long cutting cycles that go hand in hand with the light chip loads micro-tools require. An added benefit of an air-turbine unit is that it generates a noise level below 65dB.
Higher speed, lower torque
One essential factor users should keep in mind when considering an RBX spindle is that when output speed increases, available torque decreases. The RBX5 covers spindle speeds from 40,000 to 50,000 rpm. The RBX7 handles the 60,000 to 80,000rpm range and the RBX12 delivers spindle speeds from 100,000 to 120,000rpm. The torque ranges of these three units establish guidelines for tool diameters and the machining processes they can perform. The lowest-speed unit addresses drill and end mill diameters up to 1.5mm, depending on the stability of the setup. At speeds greater than 100,000rpm, drill diameters max out at 0.4mm and end mills at about 0.6mm.
Thermal displacement of less than 1.2μm on the RBX, combined with a high accuracy tool holding system, addresses many of the requirements for running micro cutting tools. As cutting tools get smaller, the necessary spindle speed for proper tool use increases.
As the air pressure powering a speeder rises above 45psi, spindle speeds will increase. The maximum required air pressure to achieve the top speed in any range is 90psi. Regardless of the drive mechanism used, most problems associated with high-rpm micromachining are caused by poor dynamic run-out of the machine spindle and its attached cutting tool assembly. BIG KAISER has integrated its air-turbine drive mechanisms directly into a proven high-speed tool-holding solution, a micro-collet that clamps tool shanks with diameters as small as 0.5mm. This extremely high clamping force and low run-out of 3μm at 4 times tool diameter increases tool life and improves finish, compared to a conventional collet system.
For further details on how you can improve productivity, prolong spindle longevity, improve precision and tool life whilst improving the capabilities of your existing machine tool, call ITC for more details on the BIG KAISER range of RBX high speed spindle units or visit Stand 5220 at MACH 2016.