Kerf Cuts A Clean Profile for Bristol Subcontractor
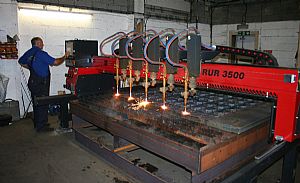
When Adam May was working for a steel profiling company, the young engineer was disillusioned by the poor quality and lead times of the supply chain. Mr May spotted a gap in the market for a reputable company to deliver high quality steel profiles to tight delivery schedules; so he set up AEM Steel Profiles Limited. Four years later, the Bristol company is already outgrowing its 5,500sq/ft facility and is harbouring ambitions of hitting a £2m turnover - not bad going for an engineer that has not long turned 30.
After developing a budding business over the last four years that now has 10 staff; the company is growing rapidly by maintaining its mantra of supplying the marketplace with high quality steel profiles on time. With the ability to supply flame cut, waterjet, laser and high definition plasma cut steel profiles up to 500mm thick; the pride of AEM's shop floor is the three flame cutting machines from Kerf Developments.
As Managing Director, Mr Adam May recalls: "Like any start up business with limited finances, we started out with 2nd hand machines. Despite our first two machines working well for the first 18 months, we wanted to start investing in new machines. Added to this, the OEM supplier was providing poor and unreliable service levels. We found Kerf Developments on-line and compared them against our current vendor. The cost, build quality and proposed service levels from Kerf won us over."
The company's first foray into Kerf machines arrived in September 2013, with a small footprint Scorpion 2500 Flame Cutting Machine with four cutting heads. This 3.2 by 2m bed machine was initially acquired to conduct one-off and small batch production runs, so AEM could retain longer production quantities on the large table machines without interrupting production with urgent jobs. As Mr May continues: "Quality and delivery is everything to us, so having a machine that can allow us to turn urgent jobs around in hours instead of days is a huge selling point. Added to this, Kerf has lived up to its promise of providing outstanding service levels. So, when we were looking at replacing our other two machines - Kerf was a clear frontrunner in the selection process."
After due diligence, AEM replaced its older machines with two Kerf RUR3500 Flame cutting machines. Delivered in August and September 2014 respectively, the new Kerf additions have a 3m wide cutting bed. With four cutting heads on one machine and five torches on the other, when compared to the configuration of 3 and 4 heads on the older machines, the two RUR3500's have drastically improved cycle times. This is particularly the case when cutting large batches of parts. Furthermore, the larger work envelope and improved nesting capability reduce waste material for the subcontractor. Operating in industries such as nuclear, oil & gas, yellow goods, Engineering and structural fabrication.
Complete Flexibility
The Kerf machines at AEM are now configured with the two RUR3500's constantly running high volume batch work, cutting up to 200mm thick steel profiles. Whilst the smaller Scorpion machine produces smaller production runs. As Mr May continues: "The current telecoms sector job on the RUR will be produced in a batch of 250 parts. The 60mm thick, mild steel plate has taken 2.5 hours to cut 160 parts, this is a 50% cycle time reduction compared to our previous machines. If we wanted to reduce our turnaround and set-up times further, the bed of the Kerf machines can be extended to accept larger steel plates. If we get an urgent job whilst this batch is running, we don't have to disrupt production as the smaller machine can cater for this."
Summarising upon the Kerf acquisitions, Mr May is extremely impressed with the build quality, precision and edge finishes provided by the Kerf product line. However, it is the ease of use and user friendliness of the control unit that was an unforeseen benefit. As Mr May states: "The Kerf machines are supplied with a Burny 10 LCD control unit, which is extremely intuitive and visually reassuring for the machine operator. On our previous machines, we would download jobs to the machines and the machine CNC would only display code. With the Burny 10, the operator has a large screen with a complete visual of the process, so any necessary changes can be made at the machine. This has also eliminated any potential errors and acted as a secondary quality control process. The simplicity and user friendliness of the Burny control combined with the robust build quality of the machine has been a revelation for us. Kerf has delivered us a simple, robust, reliable and well supported solution that meets all our profiling needs."