Kerf Makes it Easy With New Linc-Cut
3 February 2021
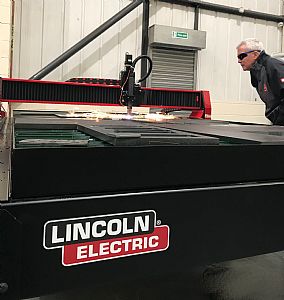
For manufacturers looking for a cost-effective CNC plasma cutting table that is easy to install, easy to set up and even easier to operate, Kerf Developments has the solution with the new Linc-Cut S 1530W. If you are looking to boost your responsiveness and creativity, this new ‘plug and play’ plasma cutting system could be the perfect cutting machine for your business.
The machine has been designed and developed by Lincoln Electric, the leading Global supplier of cutting and welding equipment. Kerf Developments will be supplying and commissioning the machines and providing training for the operators, together with service, support and spares from their headquarters in Rochdale.
Perfect for cutting mild steel and stainless steel plate up to 1.5m by 3m, the Linc-Cut 1530 makes high-speed plasma cutting affordable and attainable for small metal fabrication companies, sheet-metal contractors, custom vehicle fabricators, and prototyping companies. Whilst the cost-effective price point and flexibility of the machine make it appealing; the productivity, capability and flexibility guarantee a shrewd investment for any sheet metal processing business.
Parts that customers may want to manufacture on the machine can be input using a variety of methods. The CAD software supplied as part of the turnkey package enables users to draw components. The system also allows users to import parts in standard file formats such as DXF or DWG. Pre-loaded into the software is also 36 standard parametric shapes that include everything from simple adjustable rectangles through to complex circular flanges to simplify and speed up part programming for the end-user. Once drawn, the system is able to nest components with the potential for manual or automated programming for maximum material utilisation and cost-savings.
The Linc-Cut 1530 is fitted with the latest Lincoln Electric Flexcut 125amp plasma system which offers excellent cutting and marking performance with a very low bevel angle and an impressive cut quality. Adding to the quality and precision is impressive productivity levels with the machine capable of cutting 25mm steel plate at up to 800mm/min and thin sheets in the 6mm range at speeds beyond 5300mm/min.
From an ease-of-use perspective, the Accumove CNC motion control technology provides increased processing power and synchronisation of each component on the table. The electronic torch height control, motors and computer-aided manufacturing software are all managed within this single operating system that keeps the entire communication loop enclosed and delivered through a single visual display. The new Visual Machine Designer (VMD) is the human-machine interface (HMI) of all Accumove CNC controllers as its user-friendly design and appealing layout is extremely easy to learn and use. This is credit to a set of new functions that have been installed directly in the controller to simplify the cutting process.
These features include Process Management that allows all parameters to be controlled through the 20inch touchscreen display with a host of functions that can increase productivity. This intelligent system can automatically determine cutting conditions based on a few simple parameters entered by the user such as material thickness and type. Additional innovations include plate alignment that simplifies material loading and calculates alignment to adjust and control trajectory accordingly and the laser positioning mode that simplifies the aligning of sheets. The package also includes an automatic nesting module that enables users to load DXF or DWG files, enter the quantity and the VMD software will automatically generate the production nests.
Suitable for installation in any environment, the water table makes it possible to capture any dust released during cutting and any residual gas escape will remain below the exposure limit values for workshop conditions.