Kerf Supplies High-Def Plasma Cutting Machine to Irish Fabricating & Profiling Shop
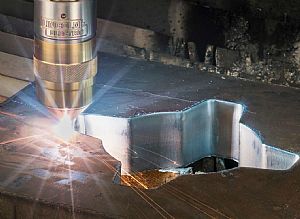
When Arcon Engineering made the trip from Ballymena to the MACH exhibition eight years ago, the fledgling company was looking for a new CNC plasma cutting machine to replace its aging and unreliable plasma machine. In meeting Kerf Developments at MACH 2008, Arcon found more than a machine supplier; it located a partner that could confidently serve all their sheet and metal plate cutting requirements.
Formed in 2003 to cater for the complex cutting and fabricating demands of the mining, transport, utilities and heavy industry sectors, Arcon offers an extremely diverse level of services. With expertise in design, CNC profiling, welding and fabrication, press brake forming, assembly and much more, Arcon Engineering has grown at an exponential rate, now employing over 30 staff. Nowhere is this growth better demonstrated than with the CNC plasma cutting machines from Kerf.
Commenting upon starting his journey of buying machines from Kerf, Arcon Engineering's Managing Director, Mr Paschal McLoughlin recalls: "Our old plasma machine was unreliable and this was compounded by our struggle to reliably obtain service support and parts. This caused considerable headaches and production bottlenecks. We went to MACH and reviewed all the available machines, and it was Kerf that had the build quality, service, support and productivity that we needed. We installed a Kerf RUR3000 CNC plasma cutting machine with a Hypertherm HPR260 plasma unit in June 2008 and it has been running over 18 hours a day plus weekends ever since."
Of course, the reliability of the RUR3000 combined with the often 24 hour production, led the Ahoghill manufacturer to invest in a second profiling machine and once again the company bought from Rochdale based Kerf. "Running our first machine non-stop, we were conscious of depending upon the reliability of the RUR3000. We knew that any breakdown or unscheduled maintenance would create a bottleneck or capacity issues. Considering this, we bought a second machine. Of course, the first Kerf machine never failed us; and within no time the second machine was also running at capacity."
The second machine, a Kerf RUR2500GP with a Lincoln Electric Proline 200amp high definition plasma system slotted straight into the business in November 2014. Like its predecessor, the RUR2500GP has been running non-stop since installation. The company is cutting profiles from one-off and small quantities to larger batch runs from materials such as stainless and mild steel with plate thicknesses varying from 3, 4 and 5mm through to heavy duty 30 and 40mm plates.
As the Irish business has expanded, it has closely reviewed its processes and more recently considered investing in a CNC laser profiling machine for high-precision cutting with impeccable edge finishes. However, upon discussing the evolving needs of the business with Kerf Developments, it was soon realised that Kerf once again had the solution. Arcon wanted to achieve extremely precise profiles with outstanding edge finishes, so Kerf took Arcon to a local company using the latest Lincoln Electric Spirit plasma unit with Ultrasharp technology to demonstrate the system.
High Definition Plasma or Laser
As Mr McLoughlin continues: "We wanted the quality of laser without the cost, Kerf gave us the alternative with their new RUR3500P machine that has an Lincoln Electric Spirit 400amp plasma unit with Ultrasharp technology. The cut quality and precision was outstanding whilst the cost wasn't near the price of a laser machine. Furthermore, the Kerf RUR3500P is more flexible than a laser as the high definition unit is powerful enough to cut through material far beyond the scope of a laser."
The single head RUR3500P machine with an Lincoln Electric Spirit 400amp high definition plasma unit was installed in June 2016 and the company has been thoroughly impressed. The design and technology built into the Lincoln Electric Spirit system incorporates a water reservoir that keeps the cutting torches cool. The benefit of this technology is that torch and consumable life is extended considerably. Furthermore, the high-powered system has a lower gas consumption. The result for Arcon is a more powerful machine with significantly reduced operating and consumable costs. For a business that is sometimes running its machines 24 hours a day, the saving over the life of the machine will be huge. In fact, trials have shown that this technology uses up to 78% less plasma gas than competitor machines.
From a capability perspective, the powerful 400amp system can cut plate up to 75mm thick, which gives Arcon the potential to extend its workload beyond existing plate thicknesses. In addition, the new machine has the ability to mark components as well as cut. This allows Arcon to mark datum points, identification features and location spots for secondary drilling operations.
In conclusion, Mr McLoughlin says: "We've had Kerf machines for almost 10 years and the local service network, machine reliability, consumable availability and the overall build quality and productivity is outstanding. Furthermore, technology has evolved considerably and with the new Lincoln Electric Spirit high definition plasma unit and the latest Burny CNC control unit that automates production and reduces material usage, Kerf has ensured that we stay ahead of the curve. We are likely to be buying machine number four in the future and I have no reason to even consider looking at a different supplier. We're delighted with our decision to invest in Kerf."