Kerf Takes Plasma Cutting to the MAX
4 October 2012
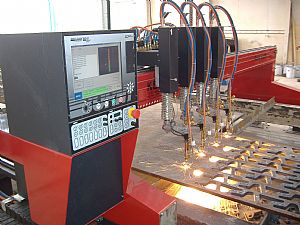
Now available for large oxy-fuel and plasma cutting applications, Kerf Developments has launched the all new MAXI 5000GP profile cutting machine. Designed for high speed profile cutting with bespoke bed sizes to meet the needs of the end user, the new MAXI machine has been designed with ease of use, reliability and flexibility in mind.
The new MAXI incorporates a number of additional features to set this innovative machine apart from its competition. With unrivalled quality levels on every feature of the machine, the MAXI delivers a smooth running, low resonance and precision machine frame that can accommodate a wide range of cutting heads. This precision is credited to the fabricated steel crossbeam that is stress relieved and precision machined to create a strong heavy duty structure that is well suited to high speed plasma and gas cutting applications.
Running on high precision linear rails and bearing assemblies that run the full length of the machine, the crossbeam guarantees unsurpassed accuracy when cutting. This accuracy is further enhanced by the installation of twin synchronised AC Servo motors and planetary gearboxes. The accuracy is given on a machine that offers cutting widths of 3.5, 4, 4.5 and 5m with bed lengths that can be bespoke to each individual application to suit single sheet or pendulum loading to maximise productivity. To further support the demands of the end user, the bed length of the MAXI can be extended at any stage as the support table is completely isolated from the side rail assemblies. This also ensures drive elements and accuracy are not compromised by shock loading, power surges or intense localised heat generated during cutting.
Setting the MAXI apart is the Burny 10 LCD Plus control system that is available on all Kerf Developments cutting machines.
The innovative PC based shape cutting motion control unit is an industrial grade PC designed for workshop environments where temperature and humidity extremes as well as airborne particulate, vibration and constant machine movement are commonplace. The focus of the Burny 10 LCD Plus is centred around customer ease of use and friendly operation. Allowing multiple control and program tasks to be completed simultaneously, the Burny 10LCD Plus also has productivity at the core of its design.
Utilising a Windows based operating system and real time motion control, the Burny control incorporates a 50 shape library that allows users to edit and create new shapes from the library, to further enhance ease of use and productivity.
This typically reduces programming times by over 80%. Additionally, this unique system improves repeatability and eliminates potential operator error. With a 15inch colour touch screen interface and additional help screens, the Burny 10 LCD Plus control on the new MAXI is undoubtedly the most user friendly and productive unit available. Furthermore, the Burny control system offers nesting software that assigns tailored lead-ins, lead-outs and cutting technology for each individual component to improve part quality.
The MAXI can be interfaced with any of the innovative range of Kaliburn plasma cutting systems offered with the Kerf machine range. Entry level air plasma systems through to ultrasharp high definition plasma cutting units are all available.