Komet Group Polishes PCD Cutters with Vollmer
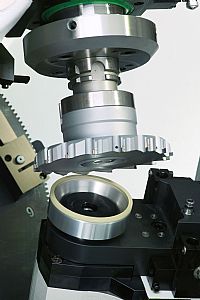
As a manufacturer of precision cutting tools, the Komet Group GmbH has employed Vollmer technology in its Stuttgart manufacturing plant to automatically polish PCD (polycrystalline diamond) blades. Komet has selected the universal QXD 200 machine that also automatically polishes PCD milling tools when they are eroded. With polished PCD cutters, Komet aims primarily to increase the lifespan of its milling tools when used on highly-abrasive composite materials.
"Regardless of whether it's in planes, wind farms or cars, in the future these products will increasingly contain light and abrasive composite materials. In order to process these materials efficiently and economically, the lifespan of blunted PCD tools must be increased. Today, with the automatic polishing process of the QXD 200 from Vollmer, we have achieved this," says Dr Reinhard Durst, Head of Research and Development of Carbide Tools at Komet.
The Komet Group that comprises of the Komet, Dihart and Jel brands, is a global market and technology leader in the field of composite and PCD thread milling cutters and drilling tools. The company is based in Besigheim. In its works in Stuttgart, Komet has a long established reputation for producing high quality PCD-tipped milling tools that have long life spans when machining aluminium. However, in order to meet the growing demand for PCD tools for highly-abrasive composite materials, the ability to polish eroded PCD blades is indispensible. Polished milling tools are less susceptible to wear and they offer extended tool life when working with composite materials.
Since the manual polishing process for PCD milling tools is very time-consuming and work-intensive, Komet decided to introduce an automatic polishing process. The basis of this is the Vollmer QXD 200 universal machine, which Komet has customised in collaboration with Vollmer to achieve its desired requirements. The result is automated clamping for the polishing process, which can be applied to a wide variety of PCD milling tools.
The oscillating polishing process is configured so that the diamond grinding disc only polishes the PCD blades directly behind the bevel. This leads to shorter processing times and less wear on the polishing disc. A typical PCD face milling cutter that is eroded by the QXD 200 in approximately four and a half hours, can then be fully polished within just 30 minutes.
"Polishing with a manual machine would take at least three times longer than with the QXD 200. In addition, automatic polishing ensures constant quality of our PCD milling tools," says Dr Reinhard Durst.
In addition to the production of Komet standard milling tools, the QXD 200 is used for special designs commissioned by customers. Komet expects a significant increase in the number of standardised milling tools in the PCD field in the near future, made possible thanks to the QXD 200. Apart from the QXD 200, Komet is using more Vollmer eroding machines in its production of PCD precision tools.
"We are bound to the Komet Group by more than just a deep-rooted customer relationship, because together we have already taken important innovative steps in PCD processing," says Dr Stefan Brand, Managing Director of the Vollmer Group. "We are expanding perfectly as one of the technology leaders in our markets, as we plan today for the challenges that the metal industry will face tomorrow."