Kuhlmeyer Belt Finishing Machine Buckles the Competition
2 September 2014
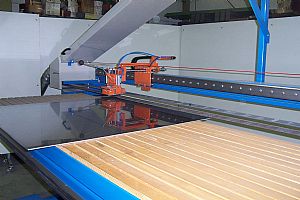
To conduct workpiece grinding and polishing in a single pass with no extra clamping or workholding of the component, Ellesco is now introducing the new Kuhlmeyer ZBS2 twin belt grinding machine.
Particularly effective for the sanding, grinding and polishing of stainless steel and a host of metallic materials, the new Kuhlmeyer ZBS2 has two abrasive belts that are driven over an idle roller that rests above the workpiece with an additional two rollers at each end of the work zone. This innovative design has been developed to eliminate secondary finishing processes whilst giving the operator complete control and visibility of the finishing process.
Primarily purchased for operations such as weld dressing, surface finishing and blending of sheet materials and also finishing folded boxes and parts manufactured from sheet steel, the standard format for the ZBS2 is typically an abrasive belt followed by a Scotchbrite type belt for finishing.
The new Kuhlmeyer ZBS2 range has a 3m wide by 1m table that can be manually operated for small components or as an option, the table traverse can be motorised for the consistently high quality finishing of large surface areas. This table can be extended up to 5m wide as standard with a table height adjustment from 0-630mm. This enhances the ergonomics for the end user whilst larger working ranges are also available upon request.
The two abrasive belts are driven by a 4KW motor with a larger 5.5KW option available for more demanding tasks. This infinitely variable frequency controlled motor drives the 9m long grinding belts at an adjustable velocity from 8 to 25m/s. The abrasive belts are automatically tensioned by individual pneumatic cylinders. This automated system ensures that surface finishes and component quality remains consistent without any requirement for operator involvement or potential error. This prolongs the life of the abrasive belts and also minimises any maintenance requirement.
For handling parts of irregular shapes, a vacuum based manipulator can be integrated to allow the part to be tilted in all axes to deliver a perfect finish on all surfaces. Ellesco can also incorporate an exchange table that allows the production flow through the Kuhlmeyer ZBS2 to be simplified for the operator whilst improving productivity levels.