Leader Bites Into Cycle Times With New Shark Machining Centre
30 September 2014
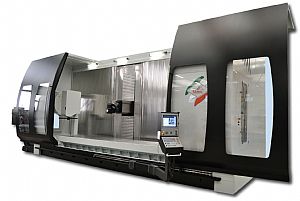
Since its recent UK launch, the new Gruppo Parpas Shark machining centre from Leader CNC has been causing a stir in the marketplace. The Shark line of high speed, fixed bed and moving column machining centres delivers high precision and speed that generates dynamic performance levels.
The construction of the Shark range is the result of painstaking Finite Element Analysis (FEA) to optimise the frequency and rigidity calculations of the machine base. With a cage-shaped column and central sliding saddle, the Shark has a thermo-symmetric structure that guarantees maximum rigidity and precision over the complete work envelope regardless of machining conditions.
Build upon this base is the highest quality linear guideways and roller bearings that permit optimum acceleration and accuracy without heat generation. These foundation blocks provide a machining centre that is ideal for machining applications in the aerospace, power generation and mould and die sectors. The machine bed is available with 3, 4 or 5m in the X axis with a Y and Z axes travel of 1200 and 1600mm respectively. The Shark can comfortably machine components in this spacious work area at a rate of 15m/min with a rapid traverse of 35m/min and acceleration/deceleration of 1.5m/min.
The innovative new machine has a variety of rotating spindle heads available to offer the customer full 4th-axis machining capability. The numerous spindle heads that are driven by powerful torque motors can provide continuous and contemporary positioning accuracy of 0.001 degrees throughout a full rotation of 360 degrees. With complete spindle cooling for thermal stability, the Shark series offers spindle speeds up to 7000, 10000, 20000 or 22000rpm. For heavy cutting, the operator can benefit from the high pressure coolant system or a through-tool coolant facility to immediately evacuate swarf from the work envelope.
To maximise material removal rates and rigidity, the Shark is available with a robust BT or HSK spindle taper that can be fed cutting tools from either a laterally positioned stock drum tool carousel with a quick change arm facility or via a chain magazine that can be fixed to the machine moving column. The stock drum is available with 24, 30 or 40 tool positions whilst the larger chain magazine provides 40, 50 or 60 tool stations.
With innovation integrated into every aspect of the new Shark line of machining centre, Gruppo Parpas can provide this machine with a number of bed configurations to meet the demands of the end user. These options include the TGT bed type that has an inbuilt 800rpm rotary table within a fixed table that allows turning and milling capabilities that are fully controlled by an axis within the NC unit. Another option is the TGV table that is a continually NC controlled 50rpm turntable that is operated by a torque motor. Whilst another option is the 800rpm TGW indexing table. These split bed configurations allow the machining of multiple components in a single set-up to improve productivity and support prolonged unmanned machining. Furthermore, the configurations can be divided by an optional partition wall that can be installed on the table to allow pendulum operation.