Leader CNC Grinds Out a Result for Morgan AM&T
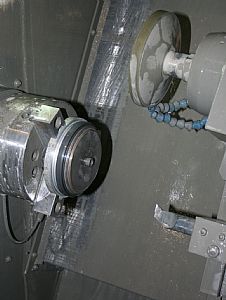
As a world leading manufacturer of impregnable silicon carbide seals & bearings for the petrochemical industry, Morgan AM&T has extensive expertise of grinding some of the most difficult and abrasive materials available. The problem that arises from wet machining such abrasive materials is maintaining the longevity of its machine tools.
When the Redditch based manufacturer reviewed the marketplace for an appropriate grinding centre and finally acquired an £180k machine, the investment only lasted a matter of months. The short lifespan of the grinding centre was caused by the fine silicon carbide from the parts and diamond from the grinding wheels penetrating the ballscrews of the machine via the coolant. With over 25 years of expertise in the field of grinding, Morgan AM&T's Production Manager Mr Martin Hanks was intent on finding a solution. After widespread investigation and realising that no standard grinding centre could resolve the issue, Mr Hanks found his solution through adapted DMC turning centres from Leader CNC.
" First, the ball screws on the DMC turning centres are not exposed to swarf from within the work envelope, so that issue is immediately eradicated. Secondly, the axis of movement on the gang-type tool slide is always on the centreline of the component, which is critical for grinding. And most importantly, with most gang-type lathes, the centreline distance of the tool spindle to the workpiece offers little clearance but, on the DMC, we can comfortably fit a 140mm diameter grinding wheel with ample clearance. Even then, although knowing that these machine features were simplifying our decision, we still had to overcome the issue of installing a grinding spindle. The Leader CNC engineering team provided a solution by retrofitting a 28,000rpm spindle from Emmaco, so then we could grind our parts," says Mr Hanks.
The first DMC, a 2-axis DMC6GL, was installed in 2008. The machine proved such a reliable and cost effective solution that the company, part of the Morgan Crucible Plc family, soon acquired two additional two machines, a DMC8GL and a second DMC6GL with a C-axis for grinding pockets.
The DMC 6GL, equipped with a C-axis, works in conjunction with a high precision air chuck and both the internal and external features on the bearing seals are machined. This combination has drastically reduced set-ups and respective cycle times on parts that previously had to be transferred to machining centres for secondary operations. To prevent the corrosive nature of the dust from penetrating the working elements of the lathe through the chuck, an additional air blast has been installed..
With components from 15 to 50mm in length and diameters up to 100mm that are produced in varying batch sizes, the production shop demands flexibility and productivity that can both be achieved in a cost effective manner.
As Mr Hanks continues: "Our components have a general tolerance band of +/-5microns, so selecting a super precision CNC grinding centre wasn't a critical consideration in our machine selection. Most grinding centres only remove a small amount of stock but, as we are removing anything from 2.5 to 14mm, the rigidity and robust design of the DMC turning centre is ideal for our needs."
The first number of DMC turning centres proved such a good fit for Morgan AM&T that it installed an additional three machines in September 2011. The DMC 8GL and two DMC6GL(M) models have all been supplied with high frequency spindles and HF inverters to enable them to slot straight into the production facility. The special spindles retrofitted to the DMC turning centres can accommodate grinding wheel diameters from 6 to 175mm with rotational speeds from 28,000 down to 6,000rpm.
The benefit of using small diameter wheels on the turning centres are many fold for Morgan AM&T. Firstly, the diamond wheels are self dressing, so the operators do not have to intervene to continually dress the wheels. Secondly, the grinding wheels on the DMC centres can be set at a 5 degree angle. When machining at this entry angle, the diamond wheels maintain their sharp edges which is critical for maintaining precision on a batch run. Most importantly, the price of small diameter diamond wheels varies from £100 to £300, their lower cost instantly creating a saving for the 40 employee business.
The new DMC additions from Leader CNC enable Morgan AM&T to machine its components at an average cycle time of 10 minutes. The increased capacity now enables the company to manufacture complete parts, from initial powder pressing and forming to final machining, in less than 2 weeks, thus improving lead times and delivery schedules.
As Mr Hanks continues: "Compared to some of our grinders that are still in operation, the DMC turning centres deliver faster machining cycles, reduced set-up times and reduced costs. Additionally, the robust turning centres offer us longevity in an extremely demanding environment whilst the flexibility of the C-axis allows us to complete parts in one-hit on one machine."
"In certain cases, even where our grinding centres are slightly faster in processing the parts than the lathes, the benefits of the Leader CNC lathes still far outweigh the grinding centres. For example, we have a relatively large family of parts that are machined in 19 minutes on a grinding centre as opposed to 24 minutes on the DMC lathe. However, the grinding centre uses a 19 inch diameter diamond wheel that costs £1000+ whereas the turning centres use a 7 inch diameter wheel at £100. Any operator error or problem with a wheel can instantly result in a breakage at a significant cost, a cost not as critical with the smaller wheels. Additionally, the large wheels require regular re-dressing that can take hours. In the time that a large wheel is dressed, the DMC lathes, which do not require re-dressing, can complete a batch of parts."
In conclusion, Mr Hanks states: "We have decades of experience in grinding but could never have believed that a turning centre would deliver a far more feasible solution for our machining needs than a dedicated grinding centre. Since we installed the DMC centres engineered by Leader CNC, our flexibility and productivity has increased drastically whilst set-ups and lead times have all been reduced. The addition of the latest three machines was a common sense decision for us and we now placed an order for two more machines."