Leader CNC Re-Engineers Success at Aerospace Subcontractor
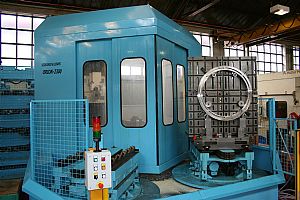
As a specialist subcontract manufacturer of medium to large parts and sub-assemblies for prestigious customers in the oil & gas, aerospace, sub-sea, defence and nuclear industries, machine tool investments at CTL Engineering Ltd are rarely below £500,000. With a mixture of new and older machine tools and when the company's capacity levels recently became stretched, CTL decided to refurbish two of its existing machines instead of opting for new plant.
With a requirement for machining turned parts up to 4m long and 2m diameter and prismatic parts up to 3m by 2m weighing 10 tonnes, the availability of machine tools with a large envelope capacity is fully utilised on a daily basis. However, with an established customer base and long term contracts in place, CTL has little space for downtime, an issue that was increasingly common on some of its more mature machine tools.
As CTL's Managing Director, Mr Ian Booth comments: "We bought our Orion 2 machine in 2004. It was acquired as a second hand machine from Cross Huller, who was using it in their machine shop in Knowsley since it was manufactured in the USA in 1991. After 8 years on our shop floor the productivity and accuracy was becoming questionable, but our main concern was the downtime, as the machine would repeatedly break down and be out of production for anything up to a couple of weeks at a time. Over the last few years we have lost 7 to 8% of the Orion's available uptime, which could cost us £11k to £20k of saleable hours each year. This was unacceptable and our options were to either invest in the region of £3/4M on a new machine or refurbish the existing Orion’s. We examined our two Giddings & Lewis Orion 2300 machines and quickly noted they had minimal mechanical wear. With such well built machines, we knew the issue was mainly electrical so we decided to refurbish our twin pallet 'Orion 2' machining centre first."
CTL called in Nuneaton based Leader CNC and the refurbishment work soon got underway. The dismantling and re-building of any large machine tool on site is an extensive project that very few UK companies have the capability or expertise to conduct. However, with its team of highly skilled engineers, Leader CNC fully stripped the machine to its carcass. It was then rebuilt with a new Fanuc 31i CNC control / axis motors / servo drives and the software was re-written. At the same time, the machine was completely re-wired and a new electrical cabinet, switchgear and panels were fitted. To demonstrate the painstaking process and expertise required for such a project, the machine had all 2500 cables and wires replaced. This means that over 5000 cable ends had to be re-connected to the correct locations and these, in turn, had to interface with the new Fanuc 31i CNC control and the newly written executive software.
Many moving or worn parts were also refurbished or replaced to finally deliver a machine tool with unrecognisable and vastly improved accuracy and performance. The refurbishment of the twin pallet Orion was aimed at improving the Stockport based company's capacity and productivity in order to further exploit its multi sector industry expertise. With the business already running a two shift pattern and its prototype and small batch workload unsuited to lights-out machining due to the manual loading and unloading of large parts, CTL realised the retro-fitting of its twin pallet machine would deliver immediate and tangible results.
"The main focus for the re-fitting was to eliminate the long and unscheduled downtime caused by breakdowns. With frequent breakdowns and the lack of technical support from the existing machine manufacturer, our ability to meet deadlines was fully dependent on the reliability, or rather the lack of reliability, of these machines. As a supplier to companies such as Rolls Royce, Babcock, FMC and Messier Dowty, delivery schedules are just as critical as the quality of the components," continues Mr Booth.
As any user of large machine tools understands, machining time and productivity level is only one critical element. Mr Booth continues: "Our aim from the refit was to improve reliability and accuracy and these elements have been achieved. We now expect machine downtime to fall below 1% for the foreseeable future. But we have also achieved so much more. From an accuracy perspective, Orion 2 previously had an accuracy range of 30 to 40 microns. This has now been improved to better than 12 microns and, considering the machine has X, Y and Z axis travels of 1500, 1200 and 1100mm respectively together with a full rotary B-axis, this now offers an impressive level of accuracy."
This improved accuracy is now provided by the use of glass scales as well as encoder feedback on every axis whereas, prior to the re-fit, the machine only had glass scale feedback available.
"Rapid traverse speeds and super fast tool change times are not essential for us as a cutting tool could be machining one component for a number of hours and, with some parts requiring upwards of 150 to 200 hours of machining, shaving seconds from a cycle is immaterial," says Mr Booth.
The improvement in machine performance has added value to a number of factors including cutting and non-cutting cycles. From the non-cutting perspective, the guide rails and location pins on the robotic mechanism that loads and unloads the 100 tool carousel have been replaced, drastically improving tool change reliability. The replacement of all electrical equipment, controls and CNC control has improved the speed of the machine and the addition of an SD Card slot, together with a DNC & network facility, has given CTL an efficient method of transferring programs from the office to the machine.
As Mr Booth continues: "The new control unit is faster on our complex aerospace work due to its powerful processing speed and longer look ahead capability. This will give us a 15 to 20% improvement over the older and slower system when performing complex 3D machining. For less complex parts, we will still achieve productivity benefits of at least 5 to 10% from the new control unit."
CTL produces parts such as undercarriage components for the Typhoon and the Airbus 330 & 340 as well as aerospace propeller profiles. For the oil & gas industry, the ISO: 9001 and AS: 9100 certified manufacturer supplies drill heads and other sub-sea equipment, including complete assemblies, whilst defence contracts include the manufacture of various submarine components. With so many parts manufactured from difficult materials such as inconel, titanium, ironic 50, super duplex and other super tensile alloys, rigidity and power are an absolute necessity for CTL.
"As some of our materials are difficult to machine, a robust machine tool is a must. Whilst the Giddings & Lewis Orion 2 is basically a robust machine, the moving parts have all contributed to reduced accuracy over the years. With the refurbishment of the spindle, a new spindle motor and a refurbished headstock, the re-build will give us improved tool life, accuracy and surface finishes, together with improved power and torque for heavy cutting operations. Now completed on the first Orion, this reliable package will be well supported by Rob Prossers team at Leader CNC and we are extremely happy with what is now ‘a new machine.‘ From a cost perspective, and what could be called ‘a second hand machine’, it now performs as good as, if not better, than a new £3/4M machine tool. Additionally, we know that the basic construction and build quality of the machine is far superior to most new foreign imports available today and the really compact floor footprint and space saving is excellent for its machining envelope," says Mr Booth.
To complete the project, Leader CNC has installed full guarding around the machine tool and its pallet system, including a twin-camera operator controlled colour CCTV system, providing full health and safety for the operators. This has also proven a major plus point for CTL as, with large parts on fork lift trucks and overhead cranes, safety is always paramount.
"The project has been such a success that we have now commissioned Leader CNC to undertake the same project on our other Giddings & Lewis Orion 2300. The next machine is a 6 pallet machine tool, so our capacity should once again increase significantly. Beyond this, and as the results have been very good, we may have some of our other machine tools overhauled," concludes Mr Booth.