Leader CNC Steams Into the Rail Market With FAT Haco Machines
3 June 2015
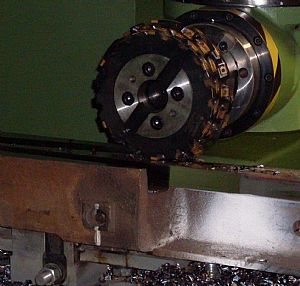
The growth of the rail industry throughout Europe has now seen FAT Haco introduce two new double column machining centres for the processing of particularly large components for this sector. Now available in the UK through Nuneaton based Leader CNC, the new FAT Haco machines can be tailored to the bespoke demands of the customer.
The FAT Haco TUR RM120 and the larger TUR RM 240 CNC machine tools have both generated considerable success on the continent in the rail industry as the build quality, capability and capacity meets the needs of the sector. The most recent installation was at a Polish OEM that acquired both machine types for the processing of railway junction components and railway tracks. Despite their recognised success in the rail sector, the characteristics of the robust FAT Haco machines also makes them an attractive proposition for manufacturers of large parts in the aerospace, oil & gas and power generation markets.
The smaller of the two machines, the TUR RM120, has an 8M by 1.2M travelling bed that sits between the twin column framethat has a spacious 2.2M clearance distance between columns. This sizeable gantry provides an 800mm stroke in the Z-axis whilst the X and Y-axis travels cover the complete bed at rapid rates of 15M/min.
To demonstrate their heavy duty cutting credentials, the TUR RM120 and TUR RM240 are supplied with a monstrous 68kW motor that offers a maximum torque rating of 5400N.m. This drives the ISO60 taper spindle through a speed range of 5 to 2000rpm with uncompromising levels of power. This powerful spindle can accommodate cutting tools up to 50kg in weight with a maximum diameter of 315mm. The TUR line has a 10 position ATC for vertical tools, with an additional 5 stations for horizontal tools which are automatically loaded into the angular milling head. These two configurations give the end user the capability to perform vertical and horizontal machining operations, thereby reducing set-up times and improving cycle times. This same configuration is also installed on the larger TUR RM240, with itskey difference being the larger 8 by 2.4M bed and longer axes travel.
The build quality of both machines is exceptional, with the cast iron bed, table, cross-rail and columns all being cast in FAT Hacos own foundry. The gears and bed are hardened to 60Rc and then ground, providing longevity beyond that of alternative machine tools. All axes are equipped with brushless AC servomotors, planetary gearboxes, Heidenhain linear scales, rigid ballscrews and direct measuring systems, thus ensuring maximum positional accuracy, repeatability and precision contouring. Incorporated into this robust range of machines are components of the highest quality from NSK, Siemens, Sauter and Danfoss. This includes Siemens drives that work in harmony with the Siemens 840D SL CNC control unit.
To protect the guideways from the huge quantities of swarf that are produced by the TUE RM machines, the guideways are protected by telescopic guards, and swarf is efficiently removed from the machine by three in-built chip conveyors. To ensure the TUR RM is supplied to exceed customer expectations, Leader CNC can install a range of optional extras that include various coolant systems, workpiece and tooling measurement, probing and specialised hydraulic clamping devices and fixtures.