Machine Investment Continues at ITC
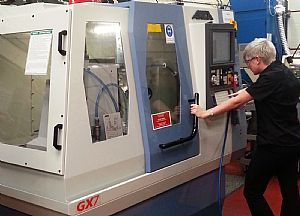
As the UK's leading manufacturer of cutting tools, Industrial Tooling Corp (ITC) has invested over £1m in new machine tools in the last 12 months. The new acquisitions include an Anca GX7, Rollomatic NP5 and four Walter Helitronic grinding centres.
The continual investment program at ITC highlights the company's commitment to delivering cutting tools that are manufactured to the highest possible standards on the latest CNC technology.
Speaking about the new machine tools, ITC's Managing Director, Mr Peter Graves comments: "We are fully committed to manufacturing solid carbide and HSS cutting tools that set new standards in geometry development, precision and surface finishes. These are all aspects that we can improve with our new technology and the result for the end user is cutting tools that further extend our reputation for quality, precision, performance and extended tool life."
The new machine purchases are not solely down to company growth, as Mr Graves says: "Some of the machines are new installations to support our capacity demands and the ongoing growth. However, the primary reasons behind the investment is to replace older machines and improve the machine specifications, reliability, automation, productivity rates and the accuracy. For example, our new Anca GX7 has replaced an aging machine. This has improved flexibility and enables us to interchange tooling and grinding wheels with our three other Anca machines. Furthermore, it enables us to do quick modifications to existing tools and it has the option for us to incorporate automation at a later stage."
The introduction of the Rollomatic NP5 increases the Tamworth company's ability to process cutting tools with shanks up to 25mm diameter, delivering more capacity for cutting tools in this diameter range. The arrival of the Walter HeliTronic Power Automation at the end of 2012 was a replacement for an older Walter machine. The direct replacement that incorporates wheel changers and automation has improved the programming process with the latest Walter software. Furthermore, this new machine makes it easier for technical staff to develop new geometries. It is this ability to develop and test new geometries on the latest CNC machines that sets ITC apart from its competitors.
Two of the new Walter grinding centres, a MiniPower F and a HeliPower both include a Fanuc robotic loading and unloading systems that feed pallet systems at the side of each machine. These new additions have improved setting times and cycle times with faster tool to tool times and productivity rates. All this is provided in a grinding cell that has in-process gauging. This ensures the machine is able to maintain its high accuracy tolerance level of 5microns with remarkable consistency. Maintaining this tolerance band on a complete batch of cutting tools that may run unmanned overnight justifies ITC's investment and highlights its commitment to customer quality.
As Mr Graves concludes: "Whilst the reason for selecting each individual machine may differ to suit our production and development needs, the overriding aspect is that our investment highlights our commitment to developing the most technically advanced cutting tools on CNC machine tools that offer capabilities and benefits beyond that of manufacturers that do not have a continual investment program. As the UK's distributor for Widia Hanita round tools, not only do our new additions enable us to offer a full re-grind service for the Widia range of products as well as the ITC manufactured products, but we can return the tools to an 'as new' condition with improved turnaround times."