Maintenance Partnership Recovers 4000 Hours of Lost Production Capacity for Automotive Manufacturer
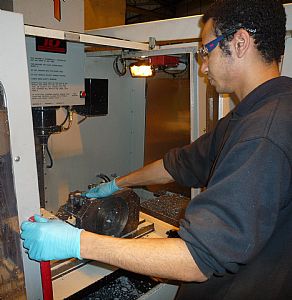
As the UK's leading remanufacturer of automotive engines, Autocraft Drivetrain Solutions is under continual efficiency, productivity and cost reduction pressures that any Tier 1 supplier to the automotive industry will appreciate. In an industry where margins are closely scrutinised, the pro-active management team at Autocraft is continually implementing new initiatives to improve efficiency and productivity.
The Grantham based company's new initiatives and plant investments have noted a spend in excess of £1m in 2011 and a similar spend in 2012. Part of this investment has included the implementation of a maintenance partnership with PEME. With eight employees in the maintenance department that cover all machine tools and production equipment across the 56,000sq/m site, the maintenance team at Autocraft was attending an average of 30 breakdowns each week. With the majority of breakdowns taking on average one full shift to repair, this meant the company was losing 30 shifts of machine production each week. A situation that needed attention.
The remanufacture of engines is a highly skilled process and is very labour intensive. Therefore, when a machine breaks down unexpectedly the resulting costs of downtime are significant. The typical automotive need for lean stock management and just-in-time deliveries mean that the recovery from a breakdown has to be completed with premium time working.
As a supplier to global OEMs such as Ford, Jaguar Land Rover, Aston Martin, Volvo, JCB, Chrysler and Bentley to name a few, Autocraft can ill afford to lose production as some of the remanufactured engines are placed in VORs (Vehicle Off Road), so lead times with the dealer network are crucial. With 140 staff and over 80 machine tools that strip down and re-manufacture over 1200 engines each month, the company invited PEME to investigate the situation in May 2012 with the aim of increasing reliability and production up-time. As a company that focuses upon maintenance partnerships that work alongside existing maintenance departments, PEME developed a bespoke maintenance strategy for Autocraft to deliver maintenance services and reliability elements to PAS55 and ISO:9001 standards. The PEME strategy utilised reliability techniques such as Condition Based Monitoring (CBM), Reliability Centred Maintenance (RCM) and Root Cause Analysis (RCA), and 60 critical assets were identified.
From this, Peterborough based PEME implemented its unique PEME Condition Register (PCR) internet based system that provides a real-time dashboard that displays Key Performance Indicators (KPI's), CBM data and reports plus safety audit information. The PCR system provides Autocraft personnel with site reports that consist of a graphical interactive map view displaying 3D graphical models of the customer's whole facility as well as a breakdown by section and machine. This enables the Autocraft maintenance department to navigate around their factory or specified section and view the latest condition of the on-site assets by use of a visual traffic light system that identifies the condition of each machine. The maintenance team are prompted by an email from the PCR to conduct a remedial activity such as a change of oil, a new motor or drive belt.
However, the PEME programme goes beyond audit and software installation. The implementation phase involved two PEME employees working alongside the Autocraft maintenance team to improve existing maintenance plans using RCM. The PEME engineers also conduct some of the detailed and specialised tasks such as vibration analysis and oil sampling that are beyond the remit of most maintenance departments because of the technically advanced equipment required. One element that PEME has delivered to Autocraft is a culture of 'operator asset care', whereby the machine operator takes ownership and responsibility of their individual machine. As nobody will know the machine better than the operator, this is the first point of defence against any potential issues. The operator relays the information to the maintenance department and it is entered on to the PCR which then triggers the corrective maintenance action.
As Autocraft's co-owner and commercial director, Mr Mike Hague-Morgan comments: "The PEME team has integrated with our maintenance department and brought in fresh eyes and a fresh way of thinking. With specialised maintenance professionals and flexibility, the PEME program has delivered both strategic direction and software that has created a more structured and long term view of our maintenance needs. Of key importance is PEME’s impeccable safety levels, they bring a culture of safety and professionalism that would benefit any manufacturer.”
As a Tier 1 automotive manufacturer that is compliant to standards such as TS:16949, ISO:9002, QS:9000, ISO:14001 and Ford Q1, the PEME system has improved compliance to the relevant standards, as Autocraft's Maintenance Manager, Mr Lenny Drew comments: "We are continually audited and reviewed for our conformity to ISO standards, the PEME system ensures we monitor and log our checks on coolant, chemical and oil usage. So, when we are audited by our OEM customers or a certification body, we have on-line and documented proof of our conformance."
"Since implementing the PEME system, we can actually schedule the work for the maintenance department. The PCR prompts the team to focus upon specific jobs at defined times or dates. My team now has a balanced workload and are undoubtedly more productive. Additionally, we can see the service history of a machine and predict when a problem will arise. I am now able to manage my team and we can now take a pro-active approach to our plant maintenance rather than the reactive response culture that was previously in place."
The implementation of the PEME system has within a matter of 5 months reduced machine breakdowns from 30 to 20 each week according to Mr Drew. "The CBM system has four to five pre-defined checks on each of the specified machines; checks that will be different from one machine to the next. However, as a department we now have more time, thanks to PEME. So, my team can also conduct directed preventive maintenance checks, and as time progresses, our machine downtime will continually decrease."
From a more analytical perspective, the PCR software has identified through the KPI Dashboard that over the short period since installation, breakdowns have been reduced by 33% whilst corrective activity has increased by 31%.
By reducing breakdowns by 33% in the short time scale, Autocraft can now conduct more planned and organised maintenance activities. This improvement in critical asset reliability has already delivered an annual recovery of 4,000 hours of lost production capacity. In the long term the strategy will be self perpetuating as there will continually be fewer breakdowns that will result in more time for the staff to conduct pro-active maintenance. Achieving a 31% increase in action clearly identifies that with the same 8 members of staff, the maintenance team at Autocraft has significantly improved its productivity in a short period of time.
Taking an overview of the current situation and the implementation of the PEME programme, Mike Hague-Morgan continues: "The PEME team has operated with an outstanding level of professionalism and the staff that visit our site have delivered a first class service and maintenance program that has integrated well with our business model. Our maintenance staff are more productive, our machine downtime is reduced, our delivery lead times are improving and most importantly our capacity and profitability is increasing. Furthermore, the improved reliability of some of our key bottleneck machines has unlocked significant capacity that we can sell without making additional capital investment."