Medical Giant's Success With First Ever Tornos EvoDECO's
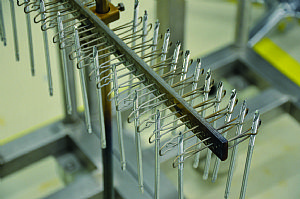
The Stryker Corporation is regarded as being a global leader in the production of orthopaedic and general medical equipment. With an extensive range of products that include joint prostheses, trauma and vertebrae implants and surgical navigation systems, Stryker has over 25,000 employees in more than 100 countries. Regarded as the benchmark in its field, Stryker relies upon turning centres from Tornos for many of its global operations.
One production facility that forms part of the US$9 billion turnover company is the implant screw business in Selzach, Switzerland. The department for implant screws in Selzach has more than 32 Tornos machines with the latest additions being two new Tornos EvoDECO 20's. The immediate success of these machines has already resulted in an order for three more of these machines, which will contribute to the production of the millions of screws the medical specialist manufactures each year.
The two EvoDECO machines were purchased to produce parts that until their introduction had been manufactured on the Tornos Deco 20. They were also lined-up to create development parts. Stryker has an extremely comprehensive machine inventory, equipped with machines from a variety of well-known manufacturers, to ensure it has the right machine for every task.
Highlighting the reasons for producing particular parts on the Tornos Deco and EvoDECO, Roland Urben, the Production Manager for Implant Screws at Stryker said: “We constantly strive to select the most suitable machine for each part we produce, in terms of both technical and economic considerations. The Tornos machines are without question, the most precise in our machine inventory, which is why we use them for the most demanding parts. From an economic perspective the Tornos machines are currently very competitive as regards return on investment.”
As a specialist well-acquainted with the old Deco 20 and the new EvoDECO 20, Mr Urben states that: “The Deco 20s were already extremely precise, and the new EvoDECO 20s operate with at least the same level of precision. We found that the biggest difference between the two generations of these machines is that the new machines are significantly more robust. In addition, the EvoDECO is much easier to operate and is also quieter, which is an advantage for our operators that should not be ignored. The ability to access TB-Deco directly from the machine simplifies things a lot and so is also much appreciated.”
Since the launch of the first Deco machines in 1996, the TB-Deco software has made a name for itself in the sector. Commenting upon this, Mr. Urben says: "There is a completely different philosophy behind it, which makes things somewhat difficult for beginners. However, once you master the software, it is a very efficient and easy-to-use tool. Most Stryker employees are assigned to a specific brand of machine, but some specialists can also switch between TB-Deco and the classic ISO system used by other machines. We manufacture many different types of part here, but everything is to do with screws, so we don’t need to switch our programming system. TB-Deco easily meets all our needs when it comes to the Tornos machines. At Stryker, one operator is in charge of several machines at the same time."
The first two EvoDECO 20s ever
“Tornos supplied us with the first two EvoDECO ever made, and we were immediately able to work productively using the machines. The quick commissioning of the machines and the excellent service by Tornos cannot be emphasised enough,” Mr. Urben explains.
Even though established implant materials such as titanium and stainless steel are used to manufacture the screws, the challenges presented in terms of geometric and dimensional precision require machines whose performance can consistently keep up with requirements. Mr. Urben is very satisfied with the EvoDECO in this regard: “The options which Tornos has specially developed for the medical sector, such as high-pressure drilling, thread whirling or hexalobular internal milling (Torx), enable us to carry out all required machining steps.” Depending on the circumstances, Stryker have developed their own macros or turned to the specialists at Tornos. The final aim is always to use the machine to machine a complete workpiece.
Alongside its department for the production of surgical screws, Stryker also operates a centre for development and prototype manufacturing, which is able to rely on the services of an EvoDECO. “Thanks to the versatility and performance of the EvoDECO, particularly for milling and cutting, we were able to develop new screws and new processes. During the planning and development of new parts, we are engaged in a constant dialogue to ensure that we are able to deliver parts which precisely meet requirements. Furthermore, to make optimal use of the possibilities and capabilities of the machine, enabling us to optimise our production,” Urben states.
Reliability for Production
Operators at Stryker work in shifts and the machines typically run around the clock for five or six days a week. Mr Urben is full of praise: “The EvoDECO is extremely reliable and robust, so we can implement small to medium-sized production runs, depending on the type of screw, without any concern. And when we need it, we know that we have a capable after-sales service we can rely on.”
“In recent years, Tornos has been working constantly on improving its after-sales service, and we are now very satisfied with the results. Their reaction time is outstanding and the solutions they suggest are always suitable,” Urben adds.