Medical Subcontractor Measures Drills of Less Than 10 Micron Diameters With Blum
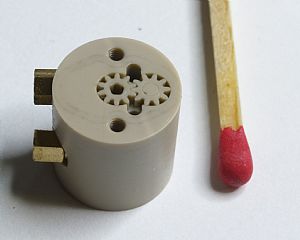
If you've never seen a 30µm diameter drill don't worry, you would need a magnifying glass. Half the thickness of a human hair is just the scale that W Präzisionstechnik works on. High precision five-axis milling machines produce the tiniest components with almost incredible accuracy. Laser-based measuring systems from Blum-Novotest are used for tool setting and breakage detection on these extremely sensitive tools.
Helmut Wandinger founded his company back in 1997 to produce machine components. He quickly made a name for himself thanks to his extremely accurate and small-scale milling work, such as production of micro-nozzles as small as 50 microns. Today, six employees work at W Präzisionstechnik and the machinery in use has expanded to a total of six five-axis machines from Chiron, Mikron and Primacon.
Tools with 10µm in diameter
The range of products manufactured by this subcontractor are mainly for the electrical engineering and medical technology sectors. Apertures, nozzles and micro-mechanical components sit alongside custom-made products for university research facilities such as the renowned Fraunhofer Institute. A short time ago, Wandinger produced metal parts with several hundred recesses, each with a diameter of 30 microns; the ball cutter used had a diameter of just 10 microns. Even nozzle matrices with almost a thousand holes in the micrometer range are no problem for W Präzisionstechnik.
To maintain the micron precision, significant investment is required. The climate in the production shops is precisely controlled to 0.1 degree Kelvin and the machines are fitted with temperature sensors all the way to the base. If it is very cold outside, the machine base cools down when the machine is turned off. The machining centre then has to run empty for several hours until the entire system is once again at a uniform temperature level. Wandinger remembers, "In the early days we had a window in the production shop and sunlight used to come through the shutters onto one of the machines. This beam of sunlight caused such significant temperature expansion that precision production was out of the question. We are often operating in tolerance ranges between two and three micrometres - not just for drilling, but for contour milling too."
All machines equipped with Blum laser measuring systems
Contactless tool measurement systems from Blum-Novotest are used on all the machines. Wandinger remembers: "At the beginning we calibrated the tools manually by touch, but even the slightest contact can destroy the tiny tool cutting edges or totally break off the tool, and we quickly moved over to laser systems." The Blum system initially arrived as part of a Chiron system and it impressed from day one.
As the LaserControl measurement systems have to be located in the working space in the machining centres, the optics need to be protected. Blum uses several methods to do this. On the one hand, the laser optics are mechanically protected by a shutter during machining. When the shutter opens for measurement, a sudden blast of air is released to clear the device of dirt and chips. During measurement, a stream of barrier air reliably protects the optics from contamination to guarantee excellent in-process reliability.
Focussed laser beam
Unlike other laser measurement systems, the laser beam on the Blum devices is focused, in other words the beam is extremely thin at a particular point between the laser transmitter and receiver. The models in the Nano NT series reach a beam thickness of just a few microns. On unfocused systems with a greater beam thickness, it is possible that the measuring system will "miss" the actual drill when determining the tool length and only detect the significantly thicker shaft. If these incorrect tool values are then used for milling, a tool breakage and a rejected workpiece are almost inevitable..
Reliable tool monitoring
Tool breakage monitoring is also an important application for the Blum measuring systems. Between two machining cycles, the tool spindle briefly moves to the laser measurement system, which measures whether the drill is still in place. At 30,000 rpm, even a very minor resonance, such as a 2 micron imbalance, can cause a 100 micron drill to break, demonstrating how important breakage detection is.
Wandinger calls it 'total breakage'. In a worst case scenario, all of the downstream tools could also break as a result. The costs of a 'total breakage' - but also of an individual broken tool - are far from negligible, as a single one of these highly sensitive tools can cost up to 250 Euro. In addition, the forces resulting from collision with the workpiece can also jeopardise the accuracy of the spindle.
Highest precision
For Wandinger, it is important that the laser measurement systems are fitted directly in the working space, ideally immediately adjacent to the tool holder. "This enables all influences, such as temperature-related expansion of the machine, to be measured and taken into account. The thermal expansion of the spindle and the tool fitting, as well as the speed-related displacement of the spindle, can also be compensated, which is essential when accuracy levels of less than ten microns are required."
The measurements that can only be carried out in the working space also include concentricity tests at operating speed. Sometimes it is not until the drill is being calibrated on the machine that incorrect labelling on the packaging is noticed. "You are trying to fathom why your 100 micron holes have a diameter of 120 microns, until you measure the tool diameter and identify the fact that the incorrect drills have actually been supplied," Wandinger said.
"I am fascinated by how accurately tools can be measured. This has a direct impact on costs. For instance, we once had a workpiece that had to have 960 tiny holes drilled in it. At this diameter, the feed rate is 1.5mm per minute. So if I slow down the movement a tenth of a millimetre too early above the surface of the workpiece when approaching a drilling point, I will be drilling nothing but air for four seconds before the drill actually gets to the workpiece. With 960 holes, this adds up to more than an hour of 'dead drilling'. However, if I have measured the length of my drill to an accuracy of a few microns, I can get closer to the surface at high speed, saving lots of time - and ultimately production costs".
No scrap parts
"We are extremely satisfied with the laser measurement systems from Blum. Because the tools are measured directly in the machine, we can achieve a level of precision that is at the very limits of what is technically feasible. We have reached the limits of conventional measurement methods. The contactless measurement technology and extreme accuracy of the Blum tool measurement systems are the only way we can achieve these tolerances. In most cases, we can now make the very first part a good part, and this is thanks largely to the LaserControl equipment," concludes Mr Wandinger.