Mitsubishi Becomes Worlds First SC21 Bronze Award Cutting Tool Manufacturer
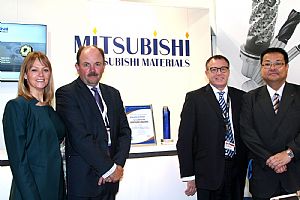
At the recent Farnborough International Air Show, Mitsubishi Materials UK was presented with an SC21 Bronze Award, making it the worlds' first cutting tool manufacturer to obtain the prestigious aerospace and defence industry award.
Supply Chain 21st Century (SC21) was a concept developed into a full programme 8 years ago as a joint collaboration between 16 of the UKs primary aerospace OEMs and 3 key SMEs. The creation of the programme came about purely as a result the major aerospace OEMs’ concern that the current quality and delivery standards of its supply chain would in the long term have an adverse impact upon growth potential of the sector.
Commenting upon the increasing uptake of the programme, Phil Curnock the Head of Supply Chain at ADS Group who manages the national programme says: "At present there are over 1200 UK companies with the AS9100 standard and we currently have over 700 of these companies signed up to SC21. SC21 goes beyond the AS9100 aerospace standard, an important difference is that it is an improvement journey not a standard and is a benchmark for excellence. The aim of the programme is to diagnose a continuous improvement strategy for each member, a strategy that revolves around operational effectiveness, quality and delivery."
Whilst Mitsubishi is a globally renowned manufacturer of high quality cutting tool solutions, the company's internal strategy to continually improve quality and delivery to its customers meant the SC21 framework was an ideal fit for the business. As Mitsubishi UK's Business Development Manager, Maria Martin comments: "In March 2013 we obtained our ISO:9001 accreditation, and as a company that always strives for improvements, we looked at the next logical step. For Mitsubishi, there were many key drivers pushing us towards obtaining the prestigious award. Firstly, to further grow the company's business in the aerospace sector, it was recognised that primary SC21 companies such as Bombardier insist that its suppliers are on the SC21 journey. Moving forward striving for the next level, Silver and Gold awards will be a key element for Mitsubishi to develop its aerospace business.”
Fundamentally SC21 is an improvement strategy that means enlisted companies should improve once on the programme. As Maria Martin said: "The SC21 programme was developed by the primary OEMs and has picked out key elements from the existing Lean, TQM and Six Sigma frameworks. This almost guarantees that a company cannot fail to improve if SC21 is implemented correctly. For Mitsubishi, this improvement programme is a management tool for developing operational excellence. It encompasses leadership, strategy and helps to build relationship excellence internally, and also with customers externally."
"To achieve the Bronze award, we had to obtain a minimum level of performance, Business and Manufacturing Excellence. The performance levels are set at a challenging 98% on-time delivery and 90% customer satisfaction for product quality. Every year this will be measured over a randomly selected 25% of our customer base. The level automatically rises for silver and gold awards and this will be our target as we strive to continually improve."
The Benefits of Accreditation
Whilst Mitsubishi has only just received its award, the fact that it has become the first cutting tool supplier to be accredited leads the company to expect that its aerospace customer base will grow considerably. However, internally the company is already reaping the rewards of the new framework.
As Maria Martin continues: "We were already running an efficient operation, but the programme has already identified aspects of our business that can and have been improved. For example, we have recently installed a new CRM system and the SC21 framework has been built into this management tool. As a result, we can map our processes and identify issues that were once unmonitored. To this end, we now collect data on any problems whether they are in the supply chain or in the product quality. For example, any problems with damaged products shipped from overseas are now identified before they even reach the customer. This wasn't previously the case."
SC21 has also improved internal communication between departments at Mitsubishi. There are no barriers in the chain of command or the supply chain, so internal sales and service staff now have improved relationships with the customers. This enables members of staff to follow the job/cutting tool from supply to end of life, giving a better understanding of the product and the customer.
In addition, delivery performance was not previously monitored in the same level of detail. The company now has a framework in place and a benchmark for improvement. "By measuring every key element of the business and building it into our CRM framework and management strategy, we have targets for quality and delivery and this has raised the bar for all our staff. SC21 has improved staff morale and motivation and has identified that we all want the same end result. By embracing the SC21 we have already witnessed improvements throughout the business and an unexpected benefit is that we now have additional capacity because the system has been able to streamline some processes. As we move forward, we will only continue to improve and grow as a business and SC21 will be a major driver in this development," concludes Maria Martin.