MKW & OPEN MIND Helps Bluebird to Sail again
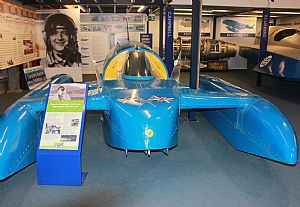
Many people will remember the 4th January 1967 as the landmark date that Donald Campbell took his Bluebird K7 to the water for the last time on Lake Coniston. Laying in a watery grave for over 30 years, it was song about Donald Campbell, 'Out of this world' by rock group Marillion that inspired the family's search for his body.
Closure for the family finally came in May 2001 when Donald's body and the Bluebird were both raised from the lake bed. Five years later, a team of engineers and enthusiasts decided to rebuild the famous craft, a project that has enlisted the charitable support from companies in the North East, such as MKW Engineering. The re-build project that started in 2006 is approaching completion credit to manufacturers like MKW Engineering that are utilising high end CAM software from OPEN MIND Technologies.
As part of the MKW Group, the Tyneside based company has provided its expertise to manufacture critical components that sit on the underside of the Bluebird's sponsons. The 14foot long sponsons are the floating wings on each side of the craft; that during the final journey at 305mph were identified to be continually bouncing off the water. Unfortunately when the sponsons bounced past the maximum 5.5degree pitch angle, the boat left the water for the last time.
MKW's involvement in the project occurred as a recommendation, credit to its manufacturing expertise in the defence, aerospace and Oil & Gas industry that sees the prestigious manufacturer producing complex 5-axis components such as satellite, communications and aircraft components plus large jigs and fixtures for the assembly of satellite systems for OEMs such as Rolls Royce, EADS, BAE, Lockheed Martin, Raytheon, BP, Total, Procter & Gamble, Nissan and the MoD to name a few.
Moving into 5-Axis
MKW acquired its first 5-axis machine tool over ten years ago to accommodate its increasingly complex workload and to reduce cycle times on its large parts with small batch sizes. Since 2002, the company has invested heavily in 5-axis machine tools. Out of its 26 machine tools, seven are now 5-axis. With the capacity to machine jobs up to 6m long by 2.5m wide, the majority of work at MKW is aluminium, stainless steels, duplex and titanium, with material costing anything upwards of £15,000 per part. With high material costs on large parts and the overall value of components after machining exceeding £25,000, getting the job 'right fist time' takes on a new level of importance.
As MKW's Sales & Commercial Director, Mr Rahmon Nassor comments: "We have invested over £6m in ten years on machine tools and this investment has continued with the addition of a full 5-Axis VTC800/30SR from Mazak in May this year. It has taken our count of Mazak's to 11. With continued investment in machine tools, our CAM package was creating problems as the post-processors were incapable of supporting the complex tool-paths on our 5-axis investments. This created scrapped parts, tool breakages, machine crashes and a culture of nervousness. Additionally, the package couldn't keep up with our high workload of one-off or small batch production of complex parts."
"We knew we needed a new CAM package and with recommendations from numerous machine tool installation engineers and our own investigation of 3 leading vendors, we opted for OPEN MIND's hyperMILL. The results have been exceptional."
Benefits of OPEN MIND's hyperMILL
Despite putting up with the limited CAM package for some time; the final straw came when the 140 employee company won a new order for batch a of complex propulsion components for an airship for the USA. The parts were virtually impossible to program on the previous CAM system, so the decision was made. hyperMILL was installed in 2011 and it immediately took the programming time from 40 hours to 24 on the propulsion part. Not only did hyperMILL reduce programming times by 45%, it also reduced the machining time by 30% for the ISO:9001 company.
As soon as hyperMILL was installed, the benefits arrived in abundance. Firstly, the ability to simulate part production prior to any physical cutting gave the programmer confidence that parts were not going to be scrapped. This confidence was backed by OPEN MIND's ability to supply post-processors for each individual machine to ensure the part programmed on screen was exactly what would be cut by the machine.
Secondly, the ability to simulate the part prior to machining enabled MKW to accurately quote jobs, as Mr Nassor continues: "Rapidly simulating parts from drawings and electronic files enables us to price work accurately for customers based on the knowledge of the machining strategies required, the cutting tools and the hours required for each job. Depending upon the features of each component, hyperMILL has reduced our programming times on average from 30 to 50%. This improved programming time is credit to a user friendly platform that is intuitive and guides the programmer through each step."
Other benefits for MKW from hyperMILL is the significant time saving for the programmer by using the easy to use tool database and the feature recognition option. This enables the programmer to select a feature on a part such as a hole, and hyperMILL will automatically identify all other holes with the parameters and calculate the tool paths accordingly to eliminate unnecessary tool changes.
Manufacturing Donald Campbell's Legacy
The feature recognition has proven of major benefit on the sponsons manufactured for the Bluebird K7 project. Each of the two 1.8m long aluminium sponson parts has over 480 holes of differing diameters and hyperMILL reduces the tool changeovers and optimises tool paths with its feature recognition cycle.
However, a key feature of hyperMILL that has proven a huge success for MKW is the mirroring function. This feature enables the programmer to mirror a program in all axes for left or right hand parts. Particularly beneficial to the F1 and aerospace industries with symmetrical structures; the sponson component initially took 8 hours to program. Instead of programming the opposite hand part with an estimated programming time of an additional 8 hours, the MKW team utilised the mirror function to create the opposite hand sponson part in minutes.
When MKW acquired its hyperMILL seat 18 months ago, the company also opted for the hyperMAXX roughing module. The Bluebird K7 project was the first part the company has applied the hyperMAXX module to. Despite the sponson parts primarily consisting of holes and slots, the application of hyperMAXX shaved 20% off the four hour machining cycle time for each part.
As Mr Nassor concludes: "Since acquiring hyperMILL, we can machine all our complex 5-axis parts in confidence that the post-processors and program transfer from OPEN MIND will machine exactly what the programmer requires. To instil further confidence, hyperMILL has 1st class collision avoidance. However, it is the improved ease of use, the reduced programming times, reduced cycle times and the other features such as mirroring, hyperMAXX roughing and feature recognition that are making an impact on our business. There is now a much shorter time from purchase order to delivery and hyperMILL has played a major role in that."
As for the Bluebird K7 project, the craft is being re-built around the original construction and with many components obsolete, this is a painstaking process for the engineering team. Upon its eventual completion, which is estimated to be in another two years, the Bluebird K7 will sail on Lake Coneston and then be the centrepiece of a purpose built £1m museum on the lakeside. For further information, please visit www.bluebirdproject.com or www.bluebirdk7.com.