Motorsport Manufacturer Raises the Bar with Hydrafeed
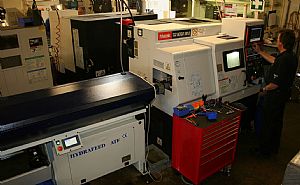
When T&K Precision Ltd invested in its latest Mazak CNC turning centre, a barfeed from Hydrafeed to accompany the machine was a necessity for the Motorsport subcontractor. The Northampton based company has acquired equipment from Hydrafeed for over 25 years, starting with rotary indexing units and collet closers that has evolved to barfeed systems when it acquired its first Mazak CNC turning centre over 12 years ago.
The acquisition of the Hydrafeed 5-51 Autofeed long magazine type barfeed was chosen by T&K Precision because of its 3.2m bar length capacity that has cut material waste and the related material costs by over 15%.
T&K Precision conducts over 95% of its work in the Motorsport industry with the core of its work being the thread rolling of studs and bolts for F1 teams. To cater for its customers, the company has 10 Mazak CNC turning centres and five Hydrafeed barfeed systems. As T&K Precision’s Director, Mr Tim Forster comments: “We acquired a Hydrafeed barfeed over 12 years ago to complement our first Mazak CNC turning centre, as the machine tool and barfeed work in complete synergy. With component turnaround’s from four hours to four weeks in a batches from 10 to 1000 in difficult to machine materials such as nimonics, titanium and high nickel alloys, the turning centres are ideal with regard to flexibility, productivity and the fast turnaround of parts. Off the back of this, the Hydrafeed barfeeds are user friendly, simple to set up and program, giving us the perfect performance combination.”
The reason for the January acquisition of the Mazak Quickturn Nexus 100 was to turn parts up to 300mm long with a 25mm diameter. Turning bar of this length would result in considerable waste if the company was to use a standard short magazine barfeed. By acquiring the Hydrafeed 5-51 Autofeed barfeed, T&K Precision is making marked material savings, as Mr Forster continues: “The materials we use are very expensive, so reducing waste and bar remnants has a marked benefit to our bottom line. Some bars we turn are over £800 for a 3m length, if the Hydrafeed 5-51 is reducing remnants by 15% we are saving £120 per bar. When we are turning components up to 300mm long in quantities up to 1000, the saving can prove very noticeable.”
When selecting production equipment T&K Precision is intent on working with suppliers that can deliver high performance plant with exceptional levels of reliability and service, as Mr Forster continues: “The studs are a critical element of the F1 car as they absorb heavy loads in the gearbox, engine, chassis and additional critical components. With such critical parts that are the final fixing before the car goes on the track, we often work to extremely short turnaround times that are incomprehensible for most manufacturers. To gaurantee we get the work out of the door and satisfy our customer demands, reliability and an impeccable service record from our suppliers is a must.”
Additionally, the T&K Precision workload requires machine tools that meet its demands for user friendly and flexible interfaces that reduce set-up times to suit small batch runs and continual changeovers.
To this end, the new Autofeed has a user friendly touch screen control system that has a memory capacity for 36 different jobs to simplify changeovers. The control system supports all trouble shooting and diagnostic features. It is linked to an innovative remote pendant that allows manual and automatic operation with bar pusher movement; emergency stop and manual load/unload functions. The control system operates the robust and reliable Mitsubishi controller and servo drive that improve the functionality and movement of the Autofeed.
Additional features on the new Autofeed include stock alignment guides for reducing set-up times plus quick change guide channels with a ‘U’ shaped bottom guide channel to enable the sections to efficiently slide out of their base. This cuts noise and vibration to improve operability for the end user.
As Mr Forster concludes: “The Hydrafeed barfeed system has delivered everything we require. It has cut costs and is user friendly, flexible, highly productive and the service and support is second to none. When I buy production equipment, high on my agenda is outstanding support, and as a UK manufacturer, Hydrafeed can provide all the technical knowledge and support we require with a fast response.”