New ITC Cutters Have a Ball With Aluminium
5 April 2012
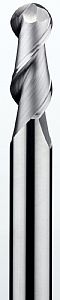
Extensive research and development work has paid dividends for ITC with the launch of its new 2172 Cyber Series ball nosed end mills for aluminium. The Tamworth based manufacturer has worked closely with leading aerospace and motorsport manufacturers that machine considerable quantities of aluminium to bring the new innovation to market.
Manufactured from ultra wear resistant micro grain carbide, the 2172 ball nosed series have been designed to offer exceptionally high performance machining on aluminium and non-ferrous materials. The centre cutting straight shank tools have a right hand helix that delivers performance that outshines competitor products. These attributes combine with a radical new flute geometry that evacuates swarf from the work envelope at a remarkable rate. This prolongs the already outstanding tool life and assists the 2172 Series in achieving its high quality surface finishes.
Unique to ITC, the flute geometry enables the 2172 Series to perform at astounding speed and feed rates to generate excellent performance levels. The new 2172 Cyber Series is available in 3, 4, 5, 6, 8, 10, 12, 16 and 20mm diameters with identical shank sizes. The overall length of the series ranges from 40 to 100mm with a length of cut for the 3mm and 20mm cutters being 20mm and 40mm respectively, with all additional cutters in the series having a proportionate and optimal flute length.
The ball nosed 2172 Cyber Series complements the existing 2161 series of square end and radius end range of milling cutters. However, with the new ball nosed 2172 Series, customers can now machine 5-axis forms and surfaces with complete confidence. The new range of cutters offers outstanding swarf evacuation and tool life credit to its geometry, which also delivers astounding results when machining cavities and additionally complex forms.
The expansive diversity of the 2172 Series provides the end user with a multitude of machining options for specialised applications. Simultaneously, the radius further enhances tool life by preventing cutter chipping and breakages which can be common when machining at high speeds and feeds.