New Tornos Turning Centre - A Paradigm Shift in Machine Tool Design
16 April 2013
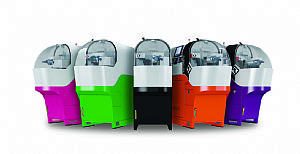
Tornos has a well established reputation in the field of bar turning for the watchmaking industry and until the launch of the new Swiss Nano, never has a manufacturer gone so far ahead in design, ergonomics and integration research with regard to a human-machine interface.
For more than 100 years, Tornos has been producing machine tools for the high-precision manufacture of small components for the watchmaking sector. Over the last twenty years, Tornos has been providing NC solutions to meet highly specific watchmaking requirements with its Deco 7 & 10, Micro 7/8, Delta 12 and EvoDeco 10. Taking all this into account, nobody knows the sector better than Tornos. To this end, the Tornos engineers pulled out all the stops to develop a machine whose design stands out resolutely against other products in the market with the aim of creating a new machine tool category.
Combining all aspects of design
It is well known that design must bring together two aspects. Firstly, the aesthetics that play on emotional effect, and secondly the practical aspects that work on both a rational and emotional level. The Tornos Marketing Manager, Mr Brice Renggli says: "We wanted to create a modern automatic turning machine with a 4mm capacity, occupying minimum floor space and with complete 180° access. So, we have created a frontal design and integrated a tablet in addition to the conventional control."
Frontal access: complete freedom of action
Given the space constraints in watchmaking and small workshops, the Swiss Nano machine was developed so it doesn't require any rear access. If necessary, it can even be placed against a wall. The machining area is protected by a ‘bubble’ and is accessible from all sides. Mr. Renggli, continues: "The setup is user-friendly, not only is everything easily visible, but it also gives us ideal accessibility. We had a very positive experience."
The Swiss Nano was intended to be a resolutely, uncompromising watchmaking machine and its kinematics enable it to produce 75% of the moving parts in a watch. However, in the UK, Tornos envisages this machine making a significant impact in the production of small connectors and the electronic industry. Production for the watchmaking and electronics sector includes anything from simple to complex parts that may require gear hobbing. Regarding the precision and quality, Mr. Renggli says: "The test customers have produced many component types and the machine runs ‘like clockwork’, behaving to their complete satisfaction."
With a footprint of 1.8 X 0.65 X 1.6m (LxWxH) and a maximum workpiece diameter of 4mm, the Swiss Nano incorporates an X1/Y1 tooling platten with seven turning tools with maximum shank dimensions of 8 X 8mm. The Swiss Nano also has the capacity for three end mounted tools with a diameter up to 16mm as well as another two end mounted tools for counter-operations. To meet the specific needs of the end user the Swiss Nano is available with optional extras such as a gear hobbing device, transverse drilling, HF spindles and polygon tools.
The 1kW induction motorised spindle and counter spindle are both capable of a maximum speed of 16,000rpm. Furthermore the Swiss Nano offers fixed, rotating and guide-bushless operation to ensure the customer receives the machine capable of producing all their parts in this diameter range. The Swiss Nano also offers peripheral additions such as a carousel collection system, vacuum, smoke extractor and fire prevention system.
Designed for stability
The kinematic structure was designed for exemplary balance and thermal management. The axes and cast iron members are aligned symmetrically to the guide bush and the thermal aspects are managed by ‘mini-loops’ that prevent heat propagation. The structure is anchored on three damped points. This enables rigidity and vibration stability to reach new peaks.
Consequently, machining precision and quality are everything that they should be. Mr. Renggli specifies: "Results of the tests were never able to fault the machine, either with respect to the high precision required in watchmaking or in terms of quality of finish."
Setting, monitoring and interaction
The Swiss Nano includes a precision tool setting system using a sensor and feeler probe. The aim of this is to provide a user-friendly system able to position the tools to within 3 to 8µ, according to the bar diameter. The greatest advance may be in terms of communication. The Swiss Nano has a graphic tablet on top. All the basic production data (workpieces, products, machine, bar changeover, fleet monitoring) are reported on this interface. At a glance, the operator can access all the data for a specific machine or for a whole fleet of machines.
Tornos UK's Accounts Manager, Mr John Stretton beleives: "In the UK Tornos UK has many customers producing small parts and we see the Swiss Nano providing addition flexibility and performance, especially in the small diameter connector industry where we have many Deco 7 and 10mm machines installed. The new Swiss Nano is more an exciting addition to our machine tool range that will offer potential beyond the remit of competitor products. Furthermore, its aesthetically eye catching, offers easy operator access and all in a small footprint. This is a very exciting new machine from the Tornos stable that will be available for UK installation in the last quarter of 2013."