Norfolk Sawmill Installs Five-Machine Vollmer Saw Blade Shop
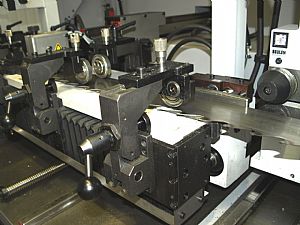
Thomson Sawmills Ltd, a forward-thinking manufacturer of fencing and landscaping/architectural timbers, has replaced the subcontract reconditioning of its bandsaw blades and circular saw blades with five machines supplied by Vollmer UK. Not only does this impressive investment in its capability save on the costs of subcontracting, but Thomson Sawmills is also reaping the rewards that come with greater quality – it has now doubled the service time of its blades!
Established in 1982, Thomson Sawmills processes around 100,000m³ of round timber every year at its 50-acre site at Felthorpe, around five miles north of Norwich. Many of the processes are automated which means the company can meet high volume demand from retail and trade customers using a complement of just 40 staff.
The company constantly seeks ways to make its operation more efficient and competitive, and in 2010 Thomson Sawmills commenced a project to review its blade reconditioning requirements.
“The blades struggle to cut straight at high speeds if they are allowed to run blunt. We change our blades before they reach this stage and as a result we get through around 75 large bandsaw blades a week, and up to 45 circular saw blades,” explains company director and sawmill manager, Jamie Thomson. “Previously we used two subcontractors to turn these around, but we were becoming increasingly concerned about deteriorating service and quality, as well as the lack of process control. Saw blade profiles are complex and even tiny changes can have a big impact on saw performance. The company felt that if we had the opportunity to exert better control over the process, there were potentially big gains on offer.”
The machines in the company’s automated saw mill were supplied in 2005 by a German specialist company in timber processing machinery, and it was in discussions last year about the blade situation that Thomson Sawmills was referred to Vollmer.
“Although we looked at various suppliers of blade reconditioning machinery, it was the support of UK-based engineers that set Vollmer apart from its main competitors,” says Mr Thomson. “In combination with the quality and reputation of Vollmer machines, the decision was made.”
Sited in a separate facility just metres from the automated sawmill, the company’s blade reconditioning facility is now home to five new Vollmer machines. Installed in October 2010, the machines are overseen by an experienced saw ‘doctor’, who was purposely employed by Thomson Sawmills at the same time.
“Our new saw doctor had previous experience working with Vollmer machines and this proved useful in terms of hitting the ground running,” says Mr Thomson. “Saw blade profiles are complex and his experience has been invaluable in generating the best forms for our timbers. With the right profile, incredible sharpness and correct tensioning, we are now reconditioning saw blades for quality, rather than quantity.”
The new Vollmer machines are arranged in cellular format. After leaving a checking station, where each bandsaw blade is assessed for defects such as broken teeth, bends and timber residue, the first job is to re-tension the blade using a Vollmer RC 100 benching centre for fully automatic dressing, a process that encompasses measuring, levelling, tensioning and straightening in a single set-up.
Thomson Sawmills uses three sizes of bandsaw blades: 17ft, 18ft and 28ft diameter. Each is run in batches of around 40-off in cycle times on the RC 100 of 25-30 minutes per blade, with just a few minutes required to change a completed blade for the next. Even changing from one size to another only takes around 15 minutes.
From here, blades progress to the Vollmer CA 210 automatic profile grinding machine, where each tooth receives a reground top and face to carefully determined parameters in terms of size and angle.
“Typically, slightly more angle on the front and back face of each tooth provides the potential for greater speed in the sawmill, but we tinker with this all time, achieving greater and greater efficiency as we acquire more and more knowledge,” says Mr Thomson.
Cycle times on the CA 210 are around 30 minutes for a 17 or 18ft bandsaw blade, or 45 minutes for the larger 28ft version. Although the company could operate the CA 210 at a rate of 30 teeth per minute, it chooses a steady pace of 8 teeth per minute for enhanced quality using a CBN grinding wheel, and this strategy has paid dividends.
“Before we had the Vollmer shop, bandsaw blades would last a single day before needing to be sharpened,” says Mr Thomson. “However, thanks to improved quality, each blade now last two days – a 100% improvement in blade life. Considering the amount of blades we process, this is a considerable saving. The increase in quality also means we can increase the feed speeds on our sawmill machines, therefore our production output is higher since the Vollmer machines were installed.”
After approximately 20 regrinds tooth size diminishes to a point where re-tipping is necessary. Here, the innovative Vollmer GPA 200, a newly developed machine based on a plasma welding technique, is deployed to deposit new stellite material on the tip of each tooth.
With two CNC controlled axes, the GPA 200 is loaded with a stellite rod which is fed into forming jaws that surround the tooth. A plasma torch heats the stellite, causing it to melt and fill the jaws. The jaws are released and the blade indexes to the next tooth. Working speeds are up to 10 teeth per minute and bandsaw blades at Thomson Sawmills can be completely re-tipped in around 30 minutes.
“Our previous subcontractors didn’t have re-tipping facilities so this was an extra cost – one that we have now saved,” says Mr Thomson.
After re-tipping, bandsaw blades require profile grinding on the Vollmer CA 210, but they also require the attention of the fourth Vollmer machine in the reconditioning shop at Thomson Sawmills, the Vollmer CAF 100 side grinding machine. Here, the sides of each tooth can be ground to the required radial and tangential angles at a rate of up to 16 teeth per minute.
The final machine in the line-up is the Vollmer CHC eco, a sharpening machine with automatic bevel grinding control for face and top machining of carbide-tipped circular saw blades with different diameters and tooth geometries. The machine is used to process circular blades up to 800mm in diameter, ranging from 16-tooth multi-rip cutters (which take around 5 minutes to sharpen) up to finishing cutters with up to 120 carbide-tipped teeth.
Once blades are fully reconditioning, they return to work in the automated sawmill: bandsaw blades are used typically to cut along the length of round timbers, while circular saws are used mainly to cut to length. All of the timbers processed are softwoods – multi-species but predominantly pine – around 30% of which is sourced from a contract with the Forestry Commission at Thetford Forest in Norfolk. The company operates in accordance with Controlled Wood standards and is certified to FSC, an international, non-governmental organisation dedicated to promoting responsible management of the world’s forests.
Thomson Sawmills Ltd manufacture and pressure treat close board, super-lap, feather edge, picket and trellis fence panels, as well as a range of landscaping/architectural fencing such as stockfence and chestnut fencing.
“With the installation of these Vollmer machines we have demonstrated that the processing of saw blades has a direct impact on the efficiency of the sawing process and hence on sawmill success,” concludes Mr Thomson. “We’ve had no reliability problems with any of the Vollmer machines and we anticipate rapid payback on our investment.”