NTK Introduces Highly Rigid Boring Bar Series
6 January 2014
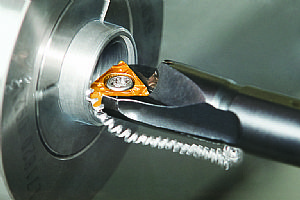
NTK now offers an extensive line of high precision boring tooling designed for Swiss type sliding head turning centres. One of the new product lines is called the 'Mogul Bar'. The Mogul Bar system provides the end user with outstanding chip control and higher rigidity than conventional boring tools.
The most notable characteristics of the Mogul Bar is its excellent chip evacuation and chip control. When the new Mogul Bars work with NTK’s F or FG chipbreaker inserts, the swarf is evacuated backwards. This means that when a Mogul Bar machines an I.D. bore, chips comes are evacuated towards the bore entrance. The majority of boring processes on Swiss machines are conducted on the main spindle and thus the bore itself is a blind hole. This machining process creates many issues if using conventional boring bars designed for CNC lathes. Typical difficulties incurred during a boring process on Swiss machines are chips remaining in the bore that create rough surfaces caused by poor chip control. However, NTK's Mogul Bars are equipped with the company's uniquely designed chipbreaker inserts to evacuate chips straight backwards, thus resolving the issue.
NTK has also engineered a larger clearance area behind the insert for chip evacuation on the bar itself. This feature has been optimally designed without losing rigidity whilst offering a though coolant capability. Another important feature of the Mogul Bar series is high rigidity. Mogul Bars increase rigidity as a result of a newly designed bar head configuration and a minimal flat width on the bar. The steel shank Mogul Bars can machine as deep as L/D=5, a depth that normally requires expensive carbide shank boring bars. Furthermore, NTK offers a carbide shank Mogul Bar that can machine up to L/D=7 depth and this gives users flexibility of machining deeper bores in a single process.
From an insert perspective, NTK offers both coated carbide grades and cermet insert grades for Mogul Bars. As most tooling engineers know, cermet grades can machine at higher speeds with higher productivity levels whilst delivering better surface finishes. Furthermore, the grades can achieve more accurate dimensional control than conventional carbide grades. These benefits come from the fact that the primary TiN/TiC substrate of cermet grades are chemically stable compared with the WC substrate of carbide grades with better adhesion resistance.
Mogul Bars are available from a minimum machining diameter of 5mm. With the combination of NTK's innovative chipbreakers, customers can enjoy better chip control and highly rigid boring bars. In comparison with solid carbide boring tools, Mogul Bars offer a cost advantage.