NTK Offers New Milling Grade For Inconel Overlays
1 August 2014
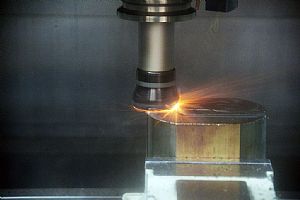
The new SX9 ceramic insert grade for high speed milling from NTK has proven to be a priceless commodity to manufacturers in the Oil & Gas industry. The remarkably tough insert grade has been launched to offer high speed and feed machining beyond 800m/min, which compared to carbide grade tooling offers significant productivity benefits.
Developed for the machining of Inconel, ductile cast irons and additionally difficult to cut materials, the astounding toughness of the new grade enables it to machine at higher feeds and heavier depths of cut than alternate ceramic grades. The engineers at NTK have recently recognised a niche application for the new grade, the high speed milling of Inconel overlays and Stellite welds that are commonplace in the Oil & Gas industry.
The refurbishment work on valve bodies for the sector that includes extensive welding and re-machining processes with the extremely difficult materials, has until now, proven problematic for the Offshore industry. With abrasive weld materials and rough surfaces, ceramic insert grades have until now been rendered too brittle to conduct such intermittent machining applications.
One particular customer tried numerous carbide grade inserts with a standard machining speed of 50m/min with inconsistent and poor tool life, surface finishes and also excessive insert changeovers. The introduction of NTK's new SX9 ceramic grade enabled the Oil & Gas subcontractor to take valve machining times from 3 hours to 13 minutes, a feat beyond the remit of carbide insert grades.
The capability of the SX9 to conduct intermittent machining on Inconel overlays and Stellite welds at speeds of 800m/min is an astonishing discovery for the industry. The ability of the new ceramic grade to offer machining speeds in excess of 20 times that of carbide grades, not only demonstrates the productivity levels of the SX9 grade - it also offers significantly improved tool life, making it the insert of choice for the Offshore industry.
Another NTK customer that tried most carbide grades with catastrophic failure, resorted to grinding its large Oil & Gas valve bores with a cycle time of 70 hours. By introducing NTK's SX9, the subcontract manufacturer slashed the production time to just one hour.
The development engineers at NTK have developed a number of insert designations that enable the SX9 to be utilised in turning and milling toolholders alike. For milling, the round RNGN and RPGN inserts can be used as can square SNGN, SNEN and SNGF inserts and rectangular LNX and APCW geometry inserts for shell, face and end milling cutters.
For high feed roughing, as highlighted with its Oil & Gas customers, NTK recommends its XTM face mill cutter body that is available in diameters from 25 to 160mm with two to 20 insert pockets depending upon the diameter of the cutter body.
For higher speed and feed milling, the QTS shell mill is available with diameter options from 40 to 125mm with four to nine insert pockets depending upon diameter selection.
The diverse availability of insert types, geometries and cutter bodies ensure that NTK can provide the marketplace with a comprehensive range of milling applications that are in many instances, the only choice for specific Oil & Gas milling processes.