OPEN MIND Celebrates 25th Anniversary
5 April 2019
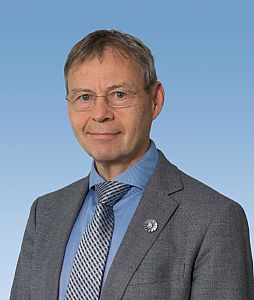
OPEN MIND Technologies AG is celebrating its 25th company anniversary. The hyperMILL® CAD/CAM suite has allowed OPEN MIND to become one of the world’s leading providers in the market. It is now considered a cutting-edge company from a technological perspective in many sectors. OPEN MIND has significantly shaped and driven forward the development of modern 5-axis simultaneous machining in tool and mold manufacturing. OPEN MIND attends to the needs of users across all industries and is now represented by its own sales and service subsidiaries in 15 countries.
25 years after the company was first founded, all signs appeared to indicate further growth at OPEN MIND. The CAD/CAM specialist had 305 employees at the end of 2018. By the end of its anniversary year, this number is set to grow to over 330 with new subsidiaries set to open. “We began with just 20 employees – but our love for technology and our innovative spirit are something that has not changed throughout the years,” says Dr. Josef Koch, CTO and one of the founders of OPEN MIND.
Strong customer relationships
With subsidiaries across the globe, OPEN MIND embodies the motto of ‘Think globally, act locally.’ The software developer attaches great importance to being close to its customers across the world in order to be able to offer them direct consultation and optimal service on-site.
Two hyperMILL® releases each year guarantee that current developments and requirements are implemented in the software for tool and mold making, as well as the automotive, aviation, production machining and energy industries. The internal innovation team seeks out new approaches and technologies to develop even more efficient solutions to global manufacturing challenges.
Customers in all industry sectors benefit from continuous time and cost savings; as well as increases in efficiency and quality. “We understand our users’ day-to-day practice down to a tee and love our software – and this is what motivates us to continue to develop innovative ideas, even after 25 years, and to further improve hyperMILL®,” says Dr. Koch. “We are pioneers in 5-axis processing, and we continue to embody this pioneering spirit. In the future, this will be our utmost challenge.”
Getting the most out of machines and tools
“With the aid of efficient processing strategies and our very own postprocessors, we have succeeded, time and time again in getting the most out of machines and further increasing process reliability, from the design to the machine. Alongside speed and surface quality, we always keep an eye on one further cost factor for the user: Machine and tool-friendly processing to extend tool lives and maintenance cycles,” says Volker Nesenhöner, CEO at OPEN MIND Technologies AG, explaining the key to the company’s success. “In addition to being able to offer the typical benefits of a CAM manufacturer, we have been availing ourselves of further options for optimizing processing methods over the last few years. We have managed to intensify cooperative relationships with our partners. We also support progressive process automation and the integration of additive manufacturing processes with our solutions.”
Innovations, special procedures, and solution packages
hyperMILL® now serves all types of cutting processing, from 2.5D, 3D, 5-axis, and 5-axis simultaneous machining to procedures such as mill turning. hyperMILL® MAXX Machining, our very own performance package, sets totally new standards in optimizing HPC tasks for both roughing and finishing. Specialized packages, such as for turbomachinery construction or the manufacturing of tire molds, offer tailor-made solutions for specific production areas. The software suite offers a complete solution, especially in conjunction with our own CAD software hyperCAD®-S, which is tailored to the requirements of CAM users. With the aid of the cutting-edge simulation solution hyperMILL® VIRTUAL Machining, the essential interconnection between CAM and the machine is made a reality and implemented, thus achieving a milestone in implementing Industry 4.0 in manufacturing.