OPEN MIND Shows 'World First' At Aero Engineering 2012
6 September 2012
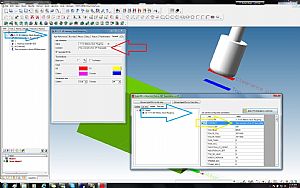
At Aero Engineering 2012, OPEN MIND Technologies will be re-affirming its position as the benchmark for providing CAM solutions to the aerospace industry. On Stand 1125 OPEN MIND will be providing demonstrations of its award winning hyperMILL CAM package as well as discussing its new Application Program Interface (API) interface.
OPEN MIND's first API system has recently been installed as part of a group project for a Tier 1 aerospace manufacturer. The two year project now enables the supplier of commercial wing skins to optically scan wing profiles and export the information using API OPEN MIND's custom solutions for product manipulation. This API system acquires 100s of thousands of measured points and delivers it to OPEN MIND's hyperCAD package that re-shapes and adapts the models, runs the operations-list and finally post processes the information to deliver an NC program to the company's server. This provides a program that is ready for machining with the necessary numbering systems used for part tracking and history. This complete process is fully automated and has zero user intervention during the process.
This completely unique solution has been specifically developed for what is an application at the highest level of aerospace technology. With each individual API package being unique to each application, OPEN MIND is offering the solution as a licensed API toolkit that can be customised by skilled programmers or to be used internally to offer custom solutions if the necessary developer skills are not available. The benefits of this fully automated package are many. Firstly, the cost of a highly skilled programmer are removed as the system is fully automated.
Additionally, the reliable and simplistic operation of the API creates process stability for improved consistency and quality. It also enables the optimisation and automation of highly complex components. The innovative new development is ideal for complex components and structures that are commonplace in the aerospace and F1 sectors.
As well as discussing the possibilities of the remarkable new API system, OPEN MIND will be keen to demonstrate why the new 5-Axis Shape Offset Roughing and Finishing feature incorporated into the company's award winning hyperMILL package, has been such a resounding success since being introduced to the marketplace at MACH 2012.
Whilst most CAM strategies are based on the assumption of two main orientations, the tool axis and the axis perpendicular to it, OPEN MIND's new Shape Offset Roughing has been developed to reduce job numbers and steps. The new machining strategy in hyperMILL enables complex curved surfaces that would be machined in 5x to be programmed like a 3x standard surface. Taking Aero engine parts as an example, one could say that the original plane is replaced by the rotary hub. The strategy then works as if it involved 'curved' Z roughing or finishing and would remove the resulting terraced steps and closely follow the desired form with the added benefits of reduced secondary roughing/finishing in later operations
This allows the NC program to be created very easily and quickly. The new approach is ideally suited to the types of cavities frequently encountered in mould and tool engineering, as well as for the machining of turbine housings, structural aerospace parts, tyre negative moulds and side panels and furthermore synthetic wood models.
Since the tool adjusts itself perpendicularly to the hub surface, there are hardly any undercuts. Each pocket and profile can be machined very cleanly. The new feature enables the use of all types of cutting tool to be used, such as end mills, ball nosed end mills and conical milling tools. The tool angle is calculated for machining either from the hub surfaces of the model or from an externally-designed guide surface.
These strategies can be link with another of OPEN MIND's recent innovations, hyperMAXX. This roughing module that can be incorporated into hyperMILL. This roughing strategy utilises unconventional tool paths to reduce the spindle load and stresses on the cutting tool to maintain a consistently high speed and feed, which has been proven to reduce cycle times by over 280% when compared with leading competitor products. At a leading cutting tool manufacturer's test facility, hyperMAXX trebled the recommended cutting feed and almost double the speed rates for an end mill being used on titanium alloy aerospace structures.
Already a hyperMILL user, the cutting tool manufacturer turned the new hyperMAXX module on and it gave a staggering 280% improvement on the previously combined use of hyperMILL and its solid carbide tooling. Considering the drastic improvement in productivity, tool life was expected to be significantly reduced. However, tool life was improved by over 200%. With unrivalled tool life improvements, productivity gains plus the bonus of reduced machine tool wear, hyperMAXX will undoubtedly prove a success at the Aero Engineering Show. For further information on the new developments from OPEN MIND, come and visit us at Aero Engineering on Stand 1125.