Optimising 5-axis machining with hyperMILL CAM Technology
25 May 2019
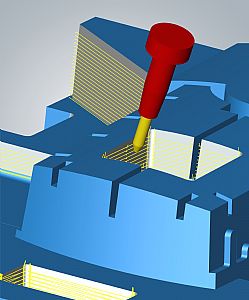
OPEN MIND is celebrating its 25th anniversary. The hyperMILL CAD/CAM suite is a success story that is closely linked with 5-axis technology, a technology that has been greatly shaped by OPEN MIND. Despite its leading position, the experts at CAD/CAM pioneers OPEN MIND are stressing that 5-axis simultaneous machining is not always the best solution.
There are few software companies that are as closely entwined with the development of 5-axis simultaneous machining as OPEN MIND Technologies AG. It was the first CAD/CAM Company to make it possible to use the technology in the tool and mould making industry, holding many patents in this area. The development work is not over yet, not by a long shot.
Further new opportunities for more efficient machining with modern tools are constantly emerging. Two years ago, OPEN MIND implemented innovative 5-axis strategies for the highly efficient finishing of planes and all continuous surfaces with the next generation conical barrel cutters. This technology allows surfaces to be machined up to 90 percent more efficiently – in part with considerably better quality.
The latest ‘5-Axis Prismatic Fillet Finishing’ strategy of the 2019.1 Version of hyperMILL also fits in well here. This strategy rounds off the hyperMILL MAXX Machining Package. This also allows plunging and pulling tool movements to be made very simply in the fillet area using a high feed rate. Even greater performance can be achieved by using the company’s innovative conical barrel cutters, which are also referred to as circle segment or parabolic end mills.
hyperMILL is a complete package that includes a wide range of 2.5D and 3D machining strategies for milling and mill/turning. A particularly striking feature of hyperMILL is its automatic strategies for 5-axis simultaneous milling that can be perfectly complemented by special applications for the turbine, tire and tube areas. The programming associated with 5-axis simultaneous strategies is basically no more complex than for 2.5D or 3D tasks. Defining the required tilting movements is very easy and support is provided for automatic collision avoidance that takes place as early as during the calculation of the toolpaths. This results in a very high level of process reliability.
Here, it is not necessary to rely exclusively on 5-axis simultaneous technology as the system automatically recognises areas for which 3-axis machining cannot be used and excludes them from the 3D operations. The missing areas can then be simultaneously reworked without any problems by using the ‘5-Axis Rework Machining’ function. The functions have been specifically designed for tool and mould making and are perfect for machining hard-to-reach areas with a short-chucking tool. Another example is ‘5-Axis Top Milling’. When machining large, moderately curved surfaces, Top Milling reduces the milling time by using greater distances between the paths. Automatically adapted tool tilt angles ensure high surface quality on concave surfaces. Thanks to multiple infeeds and stock detection, this strategy can also be used for very effective 5-axis roughing.
Use simultaneous machining sparingly
The simultaneous movement of all axes is often useful, but not always advisable. The rotary axes are slower when compared to the linear axes and can significantly increase the runtime of an NC program. For this reason, hyperMILL supports the use of strategies for automated fixed tool angles. This can be performed fully automatically or the user can choose their own areas with a fixed position. hyperMILL then calculates toolpaths for these areas that can be processed without any movement of the rotary axes. Alternatively, one of the rotary axes can also be fixed (such as the slower one) while the other one moves simultaneously with the linear axes. This makes it possible to easily separate the milling areas in a manner that avoids both overlapping and gaps. The appearance of the surface in the transition region can even be improved thanks to a special procedure.
As the attainable feed rate is determined by the slowest axis, successful 5-axis simultaneous machining lies not in the generation of movement; but rather in eliminating movements wherever possible and optimising the axes. Real simultaneous operation only occurs at the places where this does not work.
A good CAM system makes full use of the possibilities offered by machines and tools. The object is not merely to increase feed rates and material removal rates, but also to aim for machining that is easier on the tool and the machine – the avoidance of unnecessary movements is part of this.