Oxy-Fuel, Plasma, Waterjet or Laser Cutting?
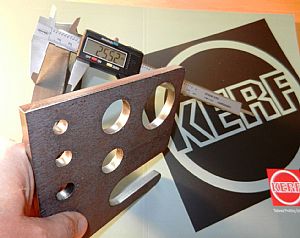
The past four decades has seen considerable developments in the metal cutting process with a range of oxy-fuel, plasma, waterjet and laser cutting machines used to cut materials from 1mm galvanised sheet through to 300mm thick mild steel.
Each process still has its role to play in the cost effective manufacture of a wide range of products. There is no question that early air plasma systems created huge leaps in productivity with the high speed cutting of steel plate. The problem however was that for many; holes were not of a good enough quality and the edge finish had a large bevel angle. Furthermore, edge dross also meant that components often required a considerable amount of manual re-working after being cut, a process that was time consuming and labour intensive.
One option that was developed was the 'combination machine' - The punch plasma. Whilst an revelation at the time, as the machine would punched out holes and cut the profiles with a plasma system, for some the hole quality still wasn't good enough due to the shear angle created by the punching process.
Step forward the modern high speed CO2 laser, developed during the 1980’s and continually evolving, the laser is a fine precise process that produces a high quality edge finish and excellent hole quality. For years laser machines have been improving in speed and capability. However, the problem is laser cutting appears to have reached its limit in terms of the thickness of material that can be cut.
Whilst new more powerful laser sources are developed there is a grey area of cutting mild steel plate from 15-20mm upwards. Some laser machines can cut these thicknesses but the edge finish is not as neat as on thinner materials.
Additionally, oxy-fuel cutting is time consuming (pre-heating the plate) and relatively slow to cut whereas laser has reached its limits; so what are the alternatives? There is waterjet that can cut thicker materials and with an excellent finish but again the process is very slow.
Rochdale based Kerf Developments believes that its recent collaboration with its technology partners has resulted in a new process that resets the standard in high definition plasma cutting.
It is claimed that the process can pierce and cut mild steel up to 60mm thick, however if the material is in the 12mm to 30mm thickness range, the company sees the major potential for the innovative new Kerf Ultrasharp technology. This thickness range poses an issue for laser cutting as it starts to run out of power and cutting speeds have to be significantly reduced, not the case with the Kerf Ultrasharp technology.
As a direct comparison, the Kerf Ultrasharp process will cut 20mm mild steel typically three times faster than a laser. Furthermore, the required investment levels are a fraction of the cost in terms of acquisition and ongoing running costs.
As Kerf’s Sales Director Craig Walsh comments: “Being independent brings huge benefits for Kerf. We are able to select the 'Best of Breed' suppliers for our machines with leading plasma, motion control and CAD/CAM technologies. We then incorporate these high-end technology products into our range to deliver cost-effective, highly productive and high quality turnkey solutions”.
“We see the Kerf Ultrasharp process as an alternative to laser for a large majority of cutting applications. The new enhancements that we have developed for the high definition plasma process produces an excellent edge quality but more importantly addresses the issue of hole cutting with plasma. The result is what is classed as 'bolt ready' holes with draft angles on internal and external profiles of less than two degrees. This we believe is unique in our market.”
“We see a huge market for Ultrasharp with companies who are already running traditional oxy-fuel, plasma or laser machines, as we can compliment these systems with the Kerf Ultrasharp technology. For those manufacturers with a suitable application for the process, we can offer a wide range of machine widths and lengths and put together cost-effective turnkey packages that we back up with exceptional after sales support. For many and most importantly, will be the productivity and cost benefits. We can provide a solution that has been proven to cut 3 times faster than laser in many trials and field tests. All this is done with a machine solution that is a fraction of the cost of laser.” concludes Mr Walsh.