Paragon Taps into Lights-Out Machining with ITC
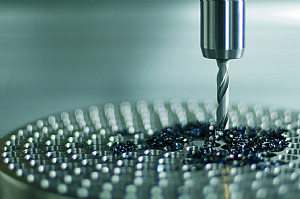
With an existing bank of sliding head turning centres and rigid fixed head twin spindle Miyano turning centres, Paragon Precision Products Ltd has evolved to become a prominent subcontract manufacturer for the Oil & Gas industry. To maintain its market position, increase its capabilities and capacity levels, Paragon has continued to make investments through 2012 that include a new Miyano ABX64 turning centre and a Haas VF4 machining centre as well as a new CMM to guarantee the precision levels of its larger parts. Despite the increased capabilities, one key element that concerned the Milton Keynes company was its supply of cutting tools to perform to the levels of its machine tools - until the introduction of cutting tools from Industrial Tooling Corporation (ITC).
Serving the medical, defence, aviation and scientific, automotive and fibre optics industries with components of exceptional complexity and quality, the core of the business for the ISO:9001 manufacturer is within the oil & gas sector. The inherent problem with supplying this demanding sector is the machining of inconel, titanium alloys and various grades of stainless steels.
As Paragon Precision's Managing Director, Mr Paul Kratovil comments: "Our daily production consists of batch runs from 50 to 30,000 turned parts from difficult materials that demand complex front and rear end machining. With large batch production, the issue was tool breakages when rear end working. One example was a stainless steel double ended valve body that required a 3.9mm diameter, 33mm deep hole on the rear end. Regularly produced in batches of 800, we trialled a number of drills from renowned tooling manufacturers, but none would drill more than 250 holes. This number was often inconsistent and we never knew when a drill would actually break. The knock-on effect was that we would lose the remainder of our back end tooling with the consequent boring bars and threading tools being damaged by the broken drill. This would incur unnecessary tooling costs and downtime that we had little control over."
It was this issue among others that noted ITC's Technical Sales Manager, Mr Gary Bambrick presenting Paragon with a number of highly productive, cost effective and consistent tooling solutions. When Mr Bambrick reviewed the drilling issue, ITC's new range of solid carbide VDS drills were introduced to the valve bodies and made an immediate impact. A 3.9mm diameter AlTiN coated VDS drill was trialled with 2000psi through coolant and immediately smashed the previous best results of 250 holes per drill. In fact, the first VDS drill was examined after machining a batch of 800 parts and showed no wear. This remarkable tool life went further, with the same drill still demonstrating no wear after 1600 holes.
This impressive set of results and the reduced tooling costs and downtime combined with the productivity gains and increased machine uptime was a success that Paragon wanted to emulate throughout the workshop. To instigate further benefits, Paragon has now introduced the VDS drills throughout the machine shop where possible, with astounding results. However, with a large component throughput each month, many of the drilled holes require subsequent threading or boring. The introduction of the VDS drills now meant that Paragon was in receipt of drills that could outperform the taps by some margin. To balance the situation, ITC trialled its new Series of GT taps. The first test was conducted on an oil & gas component produced from stainless steel that required an M6 thread and was only yielding 250 holes per tap. As soon as the ITC tap was installed, it produced over 3200 components and the tap still showed no wear.
As Mr Kratovil continues: "The ITC drills enabled us to run more jobs lights-out with complete confidence, which has obviously paid dividends for us. However, some of our long batch runs also required threaded holes on the rear-end and we had to run these jobs manned through the day because of our lack of confidence in the taps. By supplying taps that can match the performance levels of their drills, ITC has enabled us to run far more jobs unmanned overnight. We identified this as an issue some time ago and have tried pretty much everybody's drills and taps with little success. The M6 tap from ITC is the first of their taps we have used and I have never seen anything like it."
In another job, machining ½ UNC tapped holes in 316 Stainless, the component needed 30mm deep tapped holes. Competitor taps had been tried, but consistent 'Birds nesting' had required constant operator attention and often required swarf clearance before the next hole could be started. Introducing the GT Series Taps, ITC overcame this problem. Running a constant 10m/min feed rate swarf now falls off the tap, thus allowing the operator to be setting the next machine tool. A VDS Drill had been used to Drill the 10.8mm hole, and with the GT Series Tap a perfect productivity combination had been achieved.
Whilst the tapping trials are in their infancy, the results are already speaking volumes for the quality of the new ITC Range of GT Series taps. With confidence in the technical expertise of ITC's representatives and the products offered, Paragon has also trialled ITC's VariMill range of stub length solid carbide cutting tools. "The VariMill series is following on from the success of the VDS drills and GT Series Taps. The VariMill has already improved our tool life when machining stainless steel parts by over 20% whilst being a more cost effective solution than previous products. We have tried most products from a wide variety of cutting tool suppliers, but in ITC we have found some truly incredible products," concludes Mr Kratovil.