Peugeot Citroen Save Tooling Time with OPEN MIND CAD/CAM Package
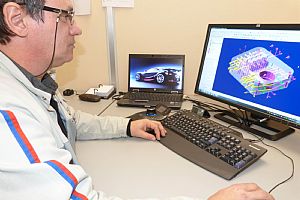
A great many tools have to be created to mass produce quality vehicles, and they have to be flawless. Their quality and cost are key factors in the competition of the global automotive market. The skill of the toolmakers and their machine-tool programming have a crucial role to play in meeting these challenges.
The role of the Peugeot Citroen Group (PSA) tool shop in Mulhouse involves designing and producing aluminium foundry moulds, casting and stamping tools for the automotive group. The Mulhouse plant close to the French border is less than 100km from Strasbourg and Zurich, geographically making it a European hub for the automotive industry. The plant has 270 on-site professionals that have access to a sizable pool of CNC machines for tack welding, drilling, milling and jig grinding. The increasing performance requirements mean that methods and resources have to be continuously improved. This rule applies equally to the programming of its machines. Some seven years ago, PSA introduced CAD/CAM programming software and it hasn't looked back since.
Meeting, tests and adopting software
The PSA tool shop in Mulhouse adopted CNC very early on, just as it did centralised programming of the machine tools. “To facilitate the programming of repetitive geometries, we developed the macro instructions ourselves in parallel with the application of the CAD/CAM software that we were using then, and independently of it,” as programmer, Serge Locher, explains. But the versions of the software have been superseded as part of a normal development, making it more and more difficult to integrate these macros.
In their search for a solution, Laurent Sifferlen, head of the process group at PSA (tooling, CAD/CAM, quality) and Serge Locher met with Jorge de Carvalho, an application engineer at Open Mind Technologies and writer of the CAD/CAM software hyperMILL. The management was won over by hyperMILL’s functionalities, ease of handling, its ability to manage complex paths, as well as its options for recording personalised macro instructions easily, and saving them. An initial programming trial on a DMG DMU80 machining centre was carried out for a lattice work foundry mould core using hyperMILL and the results were impressive.
“We were instantly surprised by the results in improving machining flexibility. By automating the loading of CAD models from Catia, we found that we were eliminating every source of error when automating the casting operations,” says Serge Locher. Furthermore, doing away with manual introductions previously required, makes it possible to achieve gains in terms of programming security, time and reliability. hyperMILL was then adopted, and two software licences were bought by the programming office.
Training and services that go that extra mile
Following three days of training for programmers by Open Mind engineers, all of the software’s functions were proven to have been properly set up and to provide the anticipated benefits. “We were able to recover our drilling, casting and milling macro instructions and create new ones directly in the hyperMILL software,” Serge Locher says enthusiastically. For programmers, this means that all their work is permanently upgraded, saving them very valuable programming time. For example, the cooling circuit of a mould of a given dimension always utilises similar drilling circuits. The macro concerned, only has to be called with a single click, and it can be integrated into the mould’s program.
More than 150 of this type of macro have already been created in the hyperMILL software bank and are used daily. After these applications in 2-axes, hyperMILL’s programming was quickly requested to test blank engraving capability; that is, machining complete moulds in three dimensions. Here too, results exceeded expectations. The result was to extend the adoption of hyperMILL programming to other machines. By programming multi-functional processes such as turning and milling makes it possible to anticipate any problem by simulating the operations.
“While turning operations are programmed in ISO, the hyperMILL software allows us to carry out all milling operations and check that everything is going to go ahead correctly,” explains Serge Locher. The simulation is going to be gradually extended to all 5-axis machines with Open Mind engineers responsible for ensuring the kinematics of each machine are integrated in the software. In parallel, the creation of macro instructions is going to be continued in 2D and in 3D.
Automatic development and facilitated communication
“Thanks to the use of macros, we are able to concentrate more quickly on what is essential and dedicate ourselves to improving how each tool is machined,” explains Serge Locher. In fact, the various machining options for pocket milling may be tested and chosen based on the best parameters.
The adoption of the hyperMAXX ® function, developed on the Open Mind core VoluMill and using the principle of trochoidal machining for deep pocket milling could soon also be part of this panel of solutions. It would achieve a time saving of around 30% in machining, not to mention a significant reduction in tool wear. One other major satisfaction point for the PSA Mulhouse tool shop programmers lies in the facility with which post processors have been implemented for each machine. As translators of the instructions programmed in the right language for each machine are based on its kinematics, the post processors form a crucial interface between the software and CNC. “With Open Mind, we know that what we are programming and simulating will actually be implemented in production,” emphasises Serge Locher. In addition, no matter how the software develops, the macros will always be valid since they are created directly in the software. Six hyperMILL licences are used in the programming office at the Mulhouse tool shop today.