Photocopy & Print Company Turns to DYSS to Improve Productivity
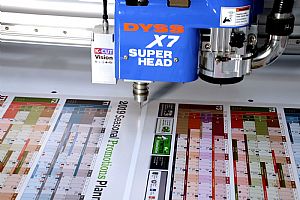
Since its inception in 1995, Print On in Cheshire has evolved from a high-street photocopy shop to a digital print-on-demand company producing everything from posters and signage through to pop-up banners, stationery, die cut boxes, PoS displays, FSDUs, acrylic boards and general large format print and finishing. To support this growth, the Cheadle company has moved to a new purpose-built facility and filled it with the latest print and finishing technology, including a DYSS digital cutter from AG/CAD.
In 2015, the business invested in a Mimaki 2.4 by 1.2m flatbed direct to substrate UV printer to expand its large format capabilities and enter new market segments. However, in the three years since, the company had been hand cutting large format sheets and boards, a laborious process open to human error. Commenting upon the situation and the decision to invest in a DYSS X7-1624C cutter, Print On Managing Director, Mr Alex Oldfield says: “We needed the flatbed printer to support the changing needs of the market and to move into large format work. Likewise, we found that customers were looking to work with an ever increasing range of substrates. Without a cutting machine we often had to turn work away or have it cut externally. Additionally, a percentage of the work that we could hand cut required geometries and shapes that were extremely challenging. We looked at the digital cutter options and as soon as I saw the DYSS machines from AG/CAD at a trade show, I knew it was the machine our business needed.”
Print On opted for the DYSS X7-1624C with the Super Head configuration for the flexibility afforded by the routing spindle and the additional 2 tool slots which can accept a range of quick-change knife tools and creasing tools. The K-CUT Camera Vision System also included in the package offers unparalleled precision when cutting printed media.
The Benefits of the DYSS
The benefits of the DYSS X7-1624C have made a significant difference to the 11 employee business, as Mr Oldfield continues: “One of the key things about the DYSS is confidence. We now have the confidence to take on all types of work, regardless of material types or complexity. We can take on work that we previously had to turn away because of these factors. This has resulted not only in the nature of our work diversifying, but also our turnover increasing accordingly. We have also increased our client base as a result of the DYSS and we are now working with more print procurement companies. This is making for an exciting time for our business and its future.”
Part of this entry into new market segments is credit to AG CAD’s KASEMAKE CAD software that was supplied with the DYSS machine. “We can now do more complex designs with the KASEMAKE software. As a company, we are now making headway with customers that are looking for boxes, FSDU’s and PoS display projects that were previously beyond our capability. This is giving us a foothold in the medical, pubs and leisure, retail and high-street sectors.”
Measuring the Impact of the DYSS
The business is currently split 50/50 between small and large format work and the DYSS has made an impact on both facets of the business. “As an example of the benefits, we have previously been contracted to print and cut 1000 A3 sheets - by cutting 20 parts per large sheet by hand, this labour intensive work would take a member of staff up to 4-5 days. With the DYSS, this work can now be completed in less than a day. We have increased productivity massively whilst reducing labour-intensive operations. Our large format work can now be processed at least 50% faster with the DYSS X7-1624C, streamlining our business and reducing lead times for customers.”
Not yet quantified are the material cost savings at Print On. However, Mr Oldfield recognises this is significant: “Previously, we would have considerable off-cuts and waste from hand-cutting boards. With the facility to ‘nest’ components with the KASEMAKE software, we can get more parts from each sheet. Additionally, we can use more of our off-cuts for future work. We no longer have to order cut-to-size sheets and this is also creating a cost saving and an improved lead-time on material supply.”
“Another factor that we can acknowledge is the reduction in human error and the subsequent waste. In the past, we would Javelin-cut large sheets and whilst this was efficient and relatively precise, when you put 2 or 3 sheets alongside each other, there would often be a slight difference. This would either result in secondary finishing or scrapping sheets and re-printing and cutting. Waste from hand-cutting could be significant, but this has been totally eradicated with the DYSS X7-1624C as its precision and consistency are guaranteed.”
On the subject of reducing lead-times, Mr Oldfield says: “With some small format work such as A4 and A5 folders, we used to order cutting formes to die cut the work. Now, if the quantity is relatively low we can cut these projects on the DYSS. This eliminates the cost and 2-3 day lead-time of buying cutting formes and enables us to pass time and cost savings on to the customer. We are delighted with the benefits and opportunities that are now open to us with the DYSS machine. It seems the longer we have the machine, the more we are recognising the cost reductions and market potential.”