Precision Aerospace Acquires Tornos Turning Centre
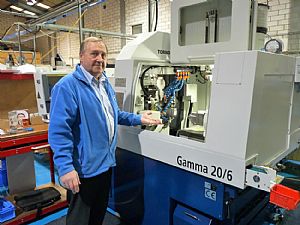
When Precision Aerospace Component Engineering Ltd (PACE) was looking to update its plant list with a new turning centre to produce bolts for the aerospace industry, the Braintree based company found the solution it required at the recent Tornos UK open house.
The aerospace manufacturer that produces components for actuators, filter systems, motors, generators and engines for commercial airliners and military aircraft wanted to acquire a high specification turning centre to replace ageing sliding head lathes. To achieve this, PACE placed an order for a Tornos Gamma 20/6 sliding head turning centre to add to its plant list of 18 CNC turning centres and 8 CNC machining centres. This plant list is continually expanding as the SC21 registered company has grown by over 20% through 2011. In 2011 alone, PACE has invested over £500,000 in machine tools with the addition of three Mazak machining centres, a Mazak turning centre for parts up to 250mm diameter, the Tornos Gamma and a Hurco VMC, scheduled for delivery in November.
The acquisition of the Tornos Gamma 20/6 is the first Tornos purchase since the AS9100 registered business bought a Tornos ENC164 in 1994. As PACE's Production Director, Mr John Green recalls: "Our Tornos ENC164 has only had 3 minor breakdowns in over 17 years of continuous running. This level of reliability and the subsequent service levels we received, always made Tornos a contender when looking for new plant. When looking for a new machine, we wanted something that was extremely capable, flexible and productive to the point that it could replace 3 ageing sliding head lathes. With the Gamma 20/6 we have achieved this."
The Gamma 20/6 has been purchased primarily for the production of bolts that the company produces in quantities over 15,000 per month. The S80 bolts are used extensively throughout an aircraft and the family of bolts produced at PACE vary from 2 to 15mm diameter in lengths up to 100mm. Currently the bolts are turned on three Manurin sliding head lathes in 50 seconds and are then transferred to a machining centre for a hexagonal bolt head to be machined. Despite having fixtures in place to improve the process, the hexagonal machining takes an additional 20 seconds and is labour intensive with the transfer of bolts from one machine to another. The Tornos Gamma 20/6 will complete the bolts in one-hit under 40 seconds by simultaneously machining the hexagon on the sub spindle whilst turning the next part on the main spindle.
As Mr Green continues: "Completing the bolts in one-hit will improve the productivity, process reliability, component quality and consistency. Additionally, having an operator involved brings an element of inconsistent production. For example, the setter putting the parts on the machining centre for hexagonal milling will need coffee, toilet and lunch breaks. With the Gamma, we can load the barfeeder with 3m bar and take the labour intensive element out of the equation. This will enable us to allocate some of our staff to alternate jobs."
PACE conducted a full review of the marketplace before selecting the Tornos Gamma 20/6 and there were a multitude of reasons that made the Tornos stand out from its competition. As Mr Green explains: "The Tornos was streets ahead of its competition with a number of advantages that made the choice a simple one. Firstly, the Gamma has a guide bushless system that its competitors do not. This system reduces bar remnants and the subsequent material waste by up to 15%. When the machine is running two shifts to produce over 800 parts a day, the material saving will be massive over an extended period. This was a major selling point for us as our aerospace grade materials are expensive and the ability to reduce costs are always attractive."
"We already have a Japanese sliding head lathe, so our experience enabled us to note a number of additional advantages with the Tornos. For example, the Tornos is a lot quieter than alternate sliding heads and it has a larger swarf capacity. Both elements improve operator experience and comfort whilst the swarf capacity reduces machine stoppages for chip clearance. Additionally, the Gamma is more capable than other sliding heads in the same price bracket, as it has a Y-axis on the sub spindle. Whilst competitors can offer this option, their machines are in a higher price bracket, a bracket where Tornos offers additional features that are again ahead of the competition."
Further points of note for 80 employee PACE are the Swiss build quality of the Gamma that far exceeds alternate machines with a similar footprint. The Tornos philosophy of rigidity runs throughout the machine right down to the tool posts that accommodate 16 X 16mm tool holders compared to 12mm on alternate machines. This feature not only improves the surface finishes on components but also provides greater tooling interchange ability between machines.
"The short delivery lead time on the Tornos means it will be fully operational by November. We are excited at the prospect of installing this machine as it will provide a multitude of savings and benefits to our business and as our business continues its success and growth, high specification machine tools can only serve to underpin our exceptional position in the aerospace marketplace," concludes Mr Green.