Precision Machining Down to the Smallest Detail
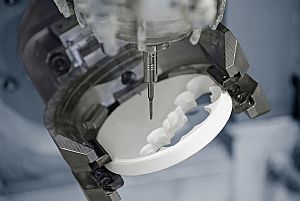
Whether its die construction, dental technology, medical equip-ment or the watchmaking, jewelry or optical industries – the number of high-precision applications for micro machining has risen enormously in recent years. Anyone who wants to take an efficient approach to delicate tooling, high spindle speeds and extreme requirements for precision must have clamping systems that offer stable processes.
In view of smaller shank diameters, ultra-fine structures, tight spaces and minimum tolerances, many tool holding systems have to fit in the micro machining area. Equally, many mounts that achieve excellent results in brand-new condition turn out to be a real thorn in the side for users over the course of time. The reasons are varied. Firstly, a tailing-off in concentricity properties, defective eccentricity and even dirt penetration are some explanations, as are seized tools or difficulties with tool pre-setting. Even with precision tool holders, it is well worth taking a closer look.
In order to achieve exact results in micro machining, the tool holder should have a concentricity and repeat accuracy of less than <0.003mm. Remember this applies to an unclamped length of 2.5 times the shank diameter. With high rotation speeds, it is also a good idea to have a balancing grade G2.5 at 25,000rpm. It is important for these values to be guaranteed in the long term. In many systems, material fatigue as a result of friction or heat sees the mountings gradually lose their high precision and tolerances can no longer be maintained.
Contamination can represent a similar problem. If even the smallest chips get into the mount and become jammed, a negative effect on the balancing grade is the result. With every clamping procedure, the tool holder then loses precision because the chips cause wear inside the mount. This effect can sometimes arise very quickly, above all with multi-piece toolholders, such as precision collets.
It is worthwhile comparing systems
If you compare the relevant clamping systems, polygonal clamping technology – patented by SCHUNK, the leading expert for clamping technology and gripping systems – performs outstandingly well. With heat shrinking technology, cooling lubricants evaporate leaving resi-dues in the clamping diameter, and it is sometimes necessary to in-stall a ventilation system in addition to the expensive, energy-intensive heat shrink unit. With polygonal clamping technology, the strain on the budget, the environment and the health of operators is reduced.
It is not even necessary to use electricity for the clamping procedure. Furthermore, heat shrink holders quickly reach their limits when it comes to small shank diameters. This is due to the thermal effects and different coefficients of thermal expansion between the holder and tool. Expensive micro tools become seized time and time again, and cannot be released from the mount. Even if things do not get so far, heat shrink tool holders frequently lose their concentricity accuracy by being repeatedly heated and cooled over the course of time.
Remarkably simple clamping principle
In contrast, the Schunk TRIBOS Polygonal Clamping Technology of-fers concentricity and repeat accuracy of <0.003mm with an unclamping length of 2.5xD over several thousand clamping procedures. With a balancing grade G 2.5 at 25,000rpm, the tool holders suitable for high speed machining are able to meet even the most demanding requirements. They are suitable for all tool shanks of h6 quality, and have been tested at up to 205,000rpm. To judge from users in the micro die construction field, TRIBOS is the first system ever to achieve reliably precise results when using milling cutters with a cutter diameter of 30µm.
Instead of a round locating hole, the tool holding system from SCHUNK has a polygonal locating hole for the tool. When a defined pressure is applied from outside using a clamping device, the locating hole deforms within the permanently elastic range, resulting in a cylinder. In this condition, it is easy to insert the tool into the holder. Then, the external pressure is reduced and the elasticity of the material causes the inner diameter to return to its original, polygonal shape. The tool is thus clamped in a force-fit grip by the inherent stress within the steel.
This applies even for the smallest shank diameters of as little as 1mm. Polygonal chucks are deformed during the clamping proce-dure. Consequently, there is no expansion in the length. This guarantees that tools can be preset with a minimum tolerance of 0.01mm in length – and this in itself is a significant advantage compared to thermal shrink holders that generally undergo what is referred to as settling, in which the preset length dimensions are reduced during cooling.
Many users have now recognized they can achieve the best surface finishes and tool service lives by taking advantage of the high abso-lute accuracy and dynamic properties as well as the good rigidity and damping values of TRIBOS. With such high demand, SCHUNK is significantly expanding its range of precision tool holding systems for micro machining this year.
New interfaces and a higher level of standardization should contrib-ute to allowing users to increase the process stability and efficiency of demanding precision applications by a noticeable amount. For ex-ample, the TRIBOS-Mini designed for high-speed micro applications will shortly be joined by the ground-breaking high-speed HSK-E 20 spindle interface. The clamping technology experts at SCHUNK are convinced that this newly standardized interface is superior to many short taper interfaces due to its accuracy at high speeds. In addition, it needs much less space compared to the HSK-E 25 interface. SCHUNK has designed the robust TRIBOS-RM with an extended L1 dimension of 78mm especially for high-efficiency 5-axes machining.
The super-long unit can be used in a multitude of applications. In addition to direct clamping, it is suitable for clamping small shank diameters in conjunction with the standardized GZB-S intermediate sleeves. In order to allow precision machining of hard-to-reach areas, the mount can also be combined with the standardized TRIBOS-SVL tool extension. As a first step, there is the universal 5-axis professional tool for HSK-A 32, HSK-A 40, HSK-E 32 and HSK-E 40 interfaces.
In addition to launching these two new products, SCHUNK is going to expand its range in such a way that many of the previous special solutions will now be included in the standard catalogue. For example, TRIBOS-Mini will be standardized with ø 1, 1.5, 2, 3, 4, 6mm and 1/8 inch. TRIBOS-RM with ø 3, 4, 6, 8, 10, 12mm and 1/8 inch. In addition to the HSK-A 25, -A 32, -A 40, -E 25, -E 32, -E 40 interfaces that are already available, both mounts will also be available for HSK-E 20, HSK-F 32 as well as for BT 30 and SK 30.