Print Specialist Opts for DYSS Digital Cutting Table
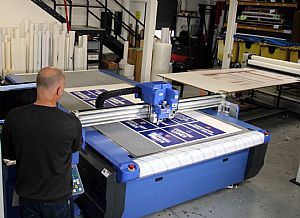
‘C3 Midlands Creative Design & Print Solutions’ is a company name that gives a distinct description of what this18 employee Birmingham business is all about. The company prides itself on its ability to turnaround customer’s work quickly whilst doing it well. It is this commitment to quality and fast turnaround’ It is this commitment to quality with a fast turnaround that has seen C3 invest in a DYSS X7-1630T digital cutter from AG/CAD.
Formed over fourteen years ago, the design and print specialist invested from day-one to serve both large and small format print sectors. Currently operating with two large format SwissQprint UV printers and a number of small roll-fed solvent printing machines, C3 Midlands initially built its business supplying brochures, fliers, PoS displays, exhibition stands, signage and anything else the company’s machines could process. As the quantity of large-scale PoS work grew, C3 Midlands was committing more man hours to hand-cutting and simultaneously subcontracting more large format cutting work out to external suppliers. This was almost 10 years ago and at the time the solution was an entry level KM6262.5m by 1.6m knife cutting machine from AG/CAD.
A Material Change
Since 2010, C3 Midlands has continued its successful journey of growth, taking on more Free-Standing Display Unit (FSDU) work, general converting jobs, and also increasing its throughput of work from large retail organisations. A brace of new SwissQprint printers helped handle the increased demand for print, but at the same time the increasing volume of work was pushing the aging KM table to its limits. The company identified that it was spending an increasing amount of time manually cutting and finishing, and more and more money subcontracting-out trickier putting jobs. Subsequently, this was extending the lead-times the company prides itself upon.
C3 Midlands identified that this reliance on outsourcing and hand finishing meant it had to upgrade its cutter to regain in-house control over lead times and final cut quality, so the company duly investigated the market. Commenting on this, C3 Midlands Production Director, Mr Steve Maycock says: “We recognised the main issue was the limitations of the original KM machine and we set about finding a new solution. We believe in investing in quality equipment and so we looked around at the main high-end players in the market, all of which were capable of what we needed. However, with 10 years of reliability from our KM machine, the familiarity with the KASEMAKE software and the excellent service and support we’ve received, we were already swaying towards our existing long-term supplier, AG/CAD. We still reviewed the market obviously, but we found nothing better quality, or better-suited to our needs than the DYSS range that AG/CAD supplies.”
“Discussing our specific requirements with AG/CAD, they recommended the static bed DYSS X7-1630T with a 3.2m by 1.6m (10'x5') bed, K-CUT Vision system and KASEMAKE CAD software from their large portfolio of options.Pound for pound, the DYSS came out top for build quality, robustness, reliability, back-up, software and the ability to integrate with our SwissQprint flatbed printers.”
Part of the strategy for eliminating the cutting and trimming bottleneck, was to improve the automation of production runs with seamless integration between the UV printers and the cutter. The arrival of the DYSS X7-1630T changed everything.
Benefits of the DYSS
As soon as the DYSS X7-1630T was installed in May, the benefits were instant. Mr Maycock recalls: “Firstly, we wiped out subcontract cutting costs. Whilst the old KM cutter could knife cutCorrex, Vinyl, Displayboardand Foamex PVC up to a limited thickness, customer demands have seen us taking on more Dibond (aluminium composite), Acrylic and thicker Foamex work that we simply couldn’t process on the old machine. Additionally, these substrates couldn’t be easily cut by hand or on a guillotine with the level of quality we need.”
Prior to the arrival of the DYSS X7-1630T, this situation extended lead-times and caused workflow issues due to a reliance on external cutting. “These materials had to be sent out for cutting so the associated costs, lack of control and extended lead-times have now been totally wiped out by the DYSS. Additionally, we are cutting many other materials, some up to 25mm thick. The DYSS has enabled us to bring all these processes back in-house, halving the turnaround times on jobs that were previously cut externally.We have also eliminated upwards of two days of manual cutting every week.”
Two days of manual labor each week is a considerable saving and Mr Maycock believes much of this is a credit to the ease-of-use and fast set-ups on the DYSS. “Anything from one-off prototypes to small batches to a couple of hundred parts were being cut manually with a knife or guillotine alongside the old KM table to alleviate the bottleneck. Now, the fast set-up times with the KASEMAKE CAD software and the high cutting speeds make it easier and faster to put these types of jobs on the DYSS.”
Highlighting the productivity of the DYSS X7-1630T, C3 Midlands would previously spend a full day cutting 50 sheets of 8’ by 4’ Foamex sheets on the old KM machine. The DYSS now carves through the same quantity of work in less than 2 hours, four times faster than the previous machine.
Converting Profits
A contributing factor to the cutting/finishing bottleneck was the fact that C3 Midlands has continually seen an increasing demand for corrugated FSDU’s. Running quantities of FSDU’s beyond 50-off, often resulted in work being sent for converting externally as the already stretched KM machine couldn't cope with the volume. The high-speed cutting of the new DYSS has enabled C3 Midlands to keep this work in-house, further reducing external costs and alleviating pressure on the finishing department.
The increase in physical cut size on the DYSS to 3.2m by 1.6m has contributed to slashing production times whilst simultaneously reducing material costs, as Mr Maycock states: “Depending upon quantity and sizes, lay-ups and rendering of small signage previously had to be done on by splitting across two 8’ by 4’ sheets. Now, we can put a single sheet of 10’ by 5’ on the DYSS to get a similar quantity of work finished. This significantly reduces the total number of sheets required and hence time spent loading/unloading, and also improves the yield we get from each sheet.”
The magnitude of the efficiencies made in terms of labor, materials, scrapped work and external subcontracting is huge. Added to this, the reduced lead-times improved cut quality and edge finishes, the precision of the K-CUT Vision camera system, as well as the elimination of a problematic bottleneck are all factors that have made the DYSS indispensable. As Mr Maycock says: “I don’t know where we would be without the DYSS.We'd certainly need two extra staff as we wouldn’t be able to cope with demand without the cutter. We’re open from 7.30am to 5.30pm every day and the DYSS runs constantly for pretty much the whole time.”
DYSS Helps C3 look to the future
The DYSS X7-1630T specified by C3 Midlands has the two-tool Combo-Head with a versatile 3rd station that currently houses a routing spindle attachment. “Our DYSS has a very high-quality router that handles all of the many materials that cannot be knife cut. However, we wanted a future-proof machine so the router is designed to be removable allowing it to be swapped with other tool options as they are developed. In our case, we are looking at an automatic adhesive tape applicator tool that is already on the market. This will enable us to add tapes to our FSDU work ready for assembling which is currently a time-consuming manual process. This isn’t generally a task you would associate with a digital cutter but AG/CAD has developed it and we will be adding this feature in the future.”