Procut Cuts a Clean Profile with Surtech
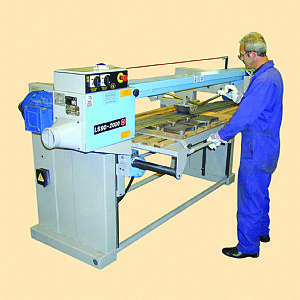
As a manufacturer of steel profiles for manufacturing and general subcontract industries, Procut (www.procutltd.co.uk) is an essential link in the supply chain of components, fitting into the chain between the steel mill and the subcontract machine shop. When Thatcham based Procut found a bottleneck in its production process that delayed the cut steel blanks from being delivered to customers, it approached Surface Technology Products (www.surtech.co.uk) of Birmingham for a solution.
The issue has always been a problem for Procut and when it won a long term order for 2000 blanks per month this became unmanageable. The company's four oxy-propane CNC profiling machines were more than capable of meeting the demand. However, the hard slag that remained on the blanks as a result of the cutting process was a difficult process to eradicate.
With the company's shop floor staff removing the slag by hand, using hammer & chisel and 7inch hand held grinders, it persevered with this process until the upsurge in work and new long term contracts created a bottleneck with this process. Whilst the lead time of 5 to 7 days for parts has remained throughout, the scheduling process required increasingly meticulous planning and additional staff for surges in workload.
The multi-head profiling machines are capable of cutting multiples of parts per day with quantities dependent upon material thickness and other parameters. These parts would then take anything up to an additional two weeks to manually remove the hard slag and dress the cut profiles. A situation that could not continue; Procut reviewed the market for a solution and found that Surtech was the only vendor capable of providing a viable solution that could be supported with impeccable service.
The first part of the solution was the acquisition of a belt linishing machine in August 2011, for the cleaning of the parts and the removal of any scale. This was soon followed by a Lima 600L friction deburring machine in February 2012 for removing the hard slag from the cut blanks.
Once all doors are closed the machine runs very quietly. The new friction deburring machine from Surtech now enables Procut to process its components at a rate similar to the actual cutting cycle to eliminate any bottleneck. As Procut's General Manager, Mr Chris Brown comments: "Our processes have always created a limited bottleneck that was manageable. However, our increased business levels highlighted the issue and we had to invest in new plant.
The friction deburrer and linisher from Surtech will pay for themselves in 18 months, such has been the effect on our business. Prior to the arrival of our new plant, we would have one man working with a chisel and hammer and another using a hand held grinder. To give a perspective of the manual labour involved, we process up to 130 tonnes of steel each month."
If the workload spiked at any particular point, the ISO: 9001 registered business would hire a delivery company to deliver its parts whilst the company's own driver would be in the workshop processing parts to minimise the bottleneck. The arrival of the Surtech plant now prevents this scenario and saves the additional cost of a delivery driver. It also ensures that two staff (sometimes three) are no longer required for hand finishing parts. The family owned business employs less than 20 staff and the capacity to allocate staff to alternate jobs whilst one man can comfortably conduct the slag removals and linishing without any fear of a bottleneck in the production process is a revelation.
Mr Brown continues: "The friction deburrer is a fully enclosed unit that has an in-built extraction unit, so not only are potential respiratory issues eradicated but the quality of the air in the workshop has improved. The same can be said of the linisher that also has an extraction unit attached for improved operator safety."
"From a quality standpoint, the friction deburrer creates a quality surface finish requiring little or no further dressing. Our customers are delighted with this, as it often removes any further finishing requirement on their part. We cut steel plate up to 300mm thick with many parts comfortably fitting into the friction deburrer. As an example of the productivity of the friction deburrer, we have just completed one order of 540 parts, previously this would take up to a full day to chip away any excess slag. With the friction deburrer the processing time was just 1.5 hours."
The friction deburrer can be loaded with up to 800 kilos of parts per cycle, a loading quantity that is governed by the dimensions of the part. Each cycle takes up to 30 minutes and parts are then removed and if required by the customer, processed on the new belt linishing machine.
The acquisition of the belt linisher, like the friction deburrer, was to limit the hand finishing the staff undertake. The Surtech belt linisher has the capacity to load a number of components on the bed and fettle them all in one process. This drastically saves time and resources whilst improving the surface finish. Whilst surface finish is not a critical element, the company also conducts plough grinding for its customers ensuring guaranteed thickness and tolerances, so a relatively high standard of surface finish and flatness is required prior to plough grinding.
The steel profiling and grinding specialist selected the Surtech linishing solution as it offered an innovative approach that allowed the operator to load small batches of parts that could all be completed in one process. Incorporating a clamping block for asserting downward linishing pressure on the components, the Surtech solution ensures the linisher and not the operator does the work.
Concluding on the purchase, Mr Brown states: "We are absolutely delighted with the two machines. They have saved us on lead times, labour requirement and costs whilst also improving our component quality. Additionally, the two machines have improved the working environment. We cannot praise the machines enough."