Progressing into 5-Axis Machining with Open Mind
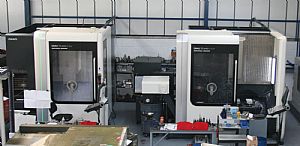
When Progressive Technologies Ltd had the insight to see the toolmaking and mould & die industries that it had historically served since 1977 enter a gradual decline, the company decided to evolve into new markets – an evolution that has paid dividends.
When Ross Pinchin took over his father Bill’s business in 1996, Progressive was a one man band operating a couple of milling machines and a manual lathe with a just a single CNC turning centre and machining centre. However, now the Managing Director of an 20 employee business operating across two sites in the Newbury area, Ross Pinchin recalls: “We needed to change direction and this required investment in new machine tools. Since 2000, we gradually employed new CNC technology to cater for the diverse customer needs. However, with the increasing complexity of components, we realised the need for 5-axis machining.”
By the middle of the 2000’s the Newbury based company built a customer base in the F1, medical, oil & gas, fibre optics, defence, aerospace and electronics industries. Working in sectors with increasingly complex component designs that required multiple set-ups, the business decided to commit to 5-axis machining and its incumbent philosophies in 2007. This commitment led to Progressive acquiring its first 5-axis machining centre, a DMG DMU50evo Linear.
Moving from 3-axis machines that adopted the 3+2 axis machining strategy with rotary tables and fixtures, to full 5-axis machining proved more than just a case of buying new machine tools. As Mr Pinchin continues: “When we decided upon the DMG machine, we realised we had to consider a suitable 5-axis CAM package. Our current package wasn’t capable of meeting our needs, so we reviewed the marketplace and despite talking to the three or four main software vendors, the name OPEN MIND kept popping up among our peers.”
“When we discussed our increasingly heavy involvement in the F1 sector with OPEN MIND and the machining of difficult 5-axis components, they took us to visit companies producing similar components for the F1 sector. We also visited a leading F1 team and when we realised they had conducted an in-depth feasibility study among CAM vendors, which OPEN MIND was the clear winner, our decision was all but made. An additional recommendation from DMG finalised the decision and when the DMG machine arrived in June 2007, we simultaneously took delivery of the hyperMILL CAM package from OPEN MIND.”
Since 2007, the leading F1 subcontractor has acquired an additional four DMG 5-axis machining centres that include a DMU80P, two DMU70evo Linear machines and an additional DMU50evo. All new machines have arrived with an additional seat of OPEN MIND’s hyperMILL, taking the hyperMILL count to five seats. However, this has now been extended to seven seats with the latest two seats arriving in December 2010.
Progressive’s Technical Director, Mr Andy Bance takes up the story, recalling: “Initially we realised that hyperMILL was a package dedicated to 5-axis machining and with the company going down that route, it was the natural selection. We were impressed with the customer testimonials as well as the collision checking that was far superior to our previous package. Now that we are fully versed in the capabilities of hyperMILL, we are impressed with functions that can drastically reduce programming times. For example, the ‘Arbitrary Roughing Cycle’ is exceptional. This one operation will virtually complete most parts in 3-axis and make it much faster to generate programs. The beauty of the arbitrary roughing cycle is that it enables the programmer to see a part take shape in one operation. The roughing cycle also incorporates intelligent tool paths and this enables us to create a geometry much faster than we ever thought possible.”
The benefit of this function at Progressive was noted when the company set up a series of six spool components on a vacuum table for processing. All six parts had a complete cycle time of 6.5 hours when utilising the previous CAM package. However, the intelligent tool paths with the drastic reduction of ‘air cutting’ enabled the Newbury company to cut cycle times by almost 50% to 3.5 hours. As Mr Bance continues: “The OPEN MIND package follows the ideal tool path, making sure there are no wasted cuts. In this instance it has saved us a huge amount of time. We cannot continually draw direct comparisons to our previous package as we are programming an average of 15 new parts each week, but when we initially did our feasibility review OPEN MIND proved far superior to the previous package. The in-programming functions in hyperMILL improve programming times by at least 25% when machining complex 5-axis parts.”
Identifying the benefits of the hyperMILL system, Mr Bance continues: “When we first looked at OPEN MIND we identified that it was easy to use and it had considerably less ‘check boxes’ than its predecessor. hyperMILL also incorporates a vast array of functions such as the ‘Tube’ and ‘Z-Level’ functions that simplify undercutting processes and in our instance inlet manifold machining. When we were reviewing the marketplace, nobody else had anything remotely similar for simplifying and speeding up the programming process. This is a philosophy that OPEN MIND still clearly maintains, as we have recently trialled and now bought the new hyperMAXX machining strategy.”
The new hyperMAXX optional roughing strategy for hyperMILL creates ideally distributed milling paths. This is based on technology that enables dynamic feed rate adjustment to existing cutting conditions. This achieves the maximum possible feed rate and speed to decisively reduce machining times, something that is currently working well at Progressive.
Added to this, all programmers have considerably more confidence in the hyperMILL anti-collision system than with previous packages. As Mr Bance states: “With the previous system there was a lot of preparation work that isn’t necessary with hyperMILL. Our previous CAM system required us to create work planes for each view, this isn’t necessary with hyperMILL. The time we are saving on the machine is considerable and the time we are saving in the office is just as critical.”
“With so many new parts being programmed each week to enable us to run the machine shop 24/7, time is of the essence. With the close of the F1 season now upon us, we are witnessing an in-flux of development work that has now seen us employ two new programmers in November. With such a heavy workload forecast and the new staff, we had to acquire a hyperMILL seat with the millTURN combined milling & turning module plus a hyperMILL seat with the hyperMAXX roughing module that has worked extremely well during the trial period. We are more than grateful that we have an exceptional package like hyperMILL on-board.”