Quality: Just-in-Time Support From Tornos For Start-Up Company
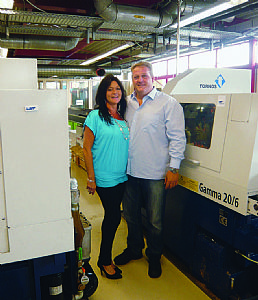
What should you do when your former employer declares bankruptcy during the crisis and when you receive only rejections to all your job applications based on market conditions? Lose hope or really get started? Horst Martin and his wife Sabine decided for the latter in mid 2010 and established their own turning shop 'Martin Präzisionstechnik' in Pforzheim with the support of Tornos and its Gamma 20/6. Just two years later they have three machines and are looking at further expansion.
Horst Martin originally trained to be a papermaker, but as an almost obsolete sector in Germany, he retrained during the 90's as a CNC milling technician. He moved up the career ladder to become the production manager of a renowned turning shop. As this company had to declare bankruptcy due to the financial crisis in 2009, Horst Martin was left for the first time with nothing. At that time, no one wanted to hire personnel, but he knew of a few companies who needed turned parts, especially small series and sample components. During an intensive discussion with his family, Horst Martin decided to go into business for himself.
The greatest difficulty was how to purchase the right machines with a limited financial budget? At the time, banks were very cautious when issuing credit and machine manufacturers were very careful with their leasing contracts. Horst and Sabine Martin approached almost all manufacturers and tried to convince them of their concept. With Jens Küttner, the Managing Director of Tornos Technologies Germany and Achim Günther, he succeeded at the AMB 2010 exhibition. Both were inspired by the energy and ability of the 'Martins' and created a specially adapted financing solution with the managers in Switzerland. Shortly after, in December 2010, the first Gamma 20/6 was delivered and commissioned.
Everything is hard at the beginning
Everything was very new for Sabine and Horst Martin at the beginning. They had to find customers and calculate and prepare offers. At the same time they also had to familiarise themselves with the machine and the control system in order to take full advantage of the machine's potential. For this, Tornos provided extremely valuable help during the start-up period. The Gamma 20/6 machine is easy to set-up and very simple to program.
Horst soon became extremely skilled with his Gamma and produced top quality products. Being both the owner and machine operator, he didn't have a 'clocking-off' time. He was able to complete the first orders quickly, flexibly and with high precision. They were mostly orders for a small series with 5 to 10 workpieces or sample parts. Here the Gamma 20 scored points due to its easy setup. But Horst Martin was able to see other advantages.
First, was its small space requirement, which he really appreciated as a founder of a new business. Then there was the practical short boring spindle kit as well as the super equipment with a 20 bar high pressure pump, CO2 extinguishers, automatic shaft unloading as well as the mobile phone radio link via SMS. As a one-man-show, it was important for Horst Martin to let the machines run as long as possible. Just before leaving work, he would set up the Gamma one more time so it could continue producing for a couple more hours on its own. News about the flexibility and quality of the young business spread quickly and he soon received more orders from neighbouring companies in the dental, jewellery and mechanical engineering industries.
A steadily climbing success curve
The main advantages Horst Martin sees in his company are the fair and direct collaboration with his customers. Horst Martin does not need any overhead, rather he sells, calculates and produces his parts on his own. It is due to this direct contact that a quick and uncomplicated solution can always be found. While the machine is running he is already calculating his next order. Three months after commissioning its first machine, the company came up against its capacity limits for the first time and had to expand. The Martin family decided upon another Gamma 20/6 from Tornos. On the one hand, Tornos proved a great partner during this phase, fully supporting the expansion. On the other, there was standardised operation, the use of existing tools and the universal programming as decisive factors. The Gamma 20/6 covers a wide range of parts from simple to complex components.
Furthermore, the machines can be used for numerous milling operations and provide high surface quality. This was an invaluable advantage especially for the long, thin needles with multiple recesses. In the meantime, as not only the number of orders but also the batch sizes continued to increase quickly, Horst Martin developed special pick-up devices in order to optimise machine use. As a one-man operation, the machines were operated almost around the clock, seven days a week. With up to 200 products in only 18 months and batch sizes up to 80,000 pieces, aroundthe clock production was absolutely necessary.
Further expansion is not excluded
With this rapid development, a new machine had to be purchased. A third Gamma 20/6 was delivered in January 2012. The ratio of requests to orders lies now at about 60%, and for some customers, Martin Präzisionstechnik now keeps its own stock. If asked about future development, Horst Martin laughs and thinks that a fourth machine is a real possibility. But, he does not need to stop there. His two sons, Marcel, 22 and Patrick, 24 are already working hard in their free time and are providing their father with solid support. It is this family atmosphere that makes this company so likeable.