Rifle Maker Shoots to Success with ITC Cutting Tools
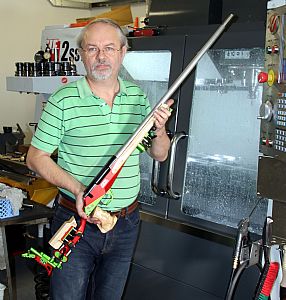
Many of us may have fired a rifle, but for Robert Nibbs it has been a lifelong passion that has evolved from childhood enthusiasm through professional career to the founding of a high-end rifle manufacturing business. Since joining his first Rifle club at the age of 14, Robert has immersed himself in the sport, representing Team GB during his career. For the last 26 years, Robert Nibbs has proudly been making rifles of distinction and precision.
Located in rural Somerset, Robert Nibbs runs a small business that designs, manufactures, builds and sells high-end target and professional rifles. As an SME, the company relies on a blend of innovative manufacturing techniques and highly-productive processes – it is here that Industrial Tooling Corporation (ITC) Ltd has stepped into the sights of this company.
At the end of 2017, Robert was having tool life issues when producing a component from 303 stainless steel. Existing solid carbide end mills were struggling to cope with the skin on the stainless and the intermittent machining process. Applying an existing solid carbide end mill, the small business could only produce 25 parts prior to tool failure. This limited tool life resulted in increased tool costs and inconvenient and repeated tool changes. Recalling the introduction of ITC cutting tools after a visit to their MACH stand, Mr Nibbs says: “I was familiar with the ITC brand and I made an enquiry via their website, they came in to review the stainless steel components and we haven’t looked back since. The ITC engineers initially trialled the WIDIA M1200HF high-feed face mill, but this was a little too aggressive for the machine parameters. We moved to the WIDIA M200 button end mills and the results have been exceptional.”
The 40mm diameter WIDIA M200 button mill cutter with WP25-PM grade inserts instantly ramped up productivity and decreased tooling costs. Commenting on this first installation, ITC’s Matt White says: “The M200 increased the feed rate from 0.1mm/tooth to 0.3mm/tooth, cutting the cycle times by more than 50%. For all of his machining processes, Robert would use the Microloc workholding system to set-up to 20 parts in a single cycle; the M200 slashed the cycle time from over one hour to 35 minutes. This would give Robert valuable time to leave the machine to run whilst he moved to other tasks, knowing that the tooling would finish the cycle intact.”
In addition, the tool costs and changeovers were drastically reduced. As Matt White recalls: “The solid carbide end mills would need to be replaced after 30 components. The 40mm diameter M200 with four insert seats has 6 edged double-sided inserts with a location lug for precision indexing. This reduced tool changeovers and set-ups drastically, but more importantly was the reduced tooling costs. Each edge of the inserts could achieve the same performance as the previous solid carbide end mill; but with 12 edges, the M200 is 12 times more cost efficient. Machining to a 2mm depth of cut, we suggested that Robert use the WIDIA M1200 for finishing operations. Applying a 0.2mm depth of cut, the M1200 has machined over 300 parts without changing an insert edge to date.”
The success of the ITC WIDIA face milling tools opened the door to trial other ITC products on the company’s HAAS VF2-SSYT 3-axis machining centre. “The performance of the WIDIA face mills was exceptional, so we introduced the WIDIA 49N9 solid carbide 3-flute rougher to the profiling of pockets on 6082-T6 grade chassis sections. We previously used solid carbide end mills from two well known brands with limited success. Then Tom Lindley, the Area Sales Engineer for the Tamworth based tooling manufacturer, suggested running the ITC WIDIA 49N9 at 12,000rpm and just shy of 8m/min at full 24mm depth of cut with a 10mm step-over; each parameter at least 50% greater than the previous tools. I was very apprehensive, but the WIDIA tool cut through the aluminium like a hot knife through butter. Processing the roughing operation at double the speed and feed parameters of the previous tools, and with manageable chip size, the WIDIA 49N9 contributed to reducing the overall cycle time of rifle butt components. This high speed machining reduced the chassis blank from 4.1kg to 1.7kg in 75 just seconds.”
The resounding success of the WIDIA face mill and solid carbide end mills gave Mr Nibbs the confidence in the application expertise of ITC’s Tom Lindley and Matt White and moreover, the quality of the products applied. This opened the door for more ITC innovations to be introduced to the Somerset based Company. Since the initial introduction, the company now utilises the ITC 2041 and 2052 solid carbide square-end tools as well as the 3041, 3051, 2201 and 3081 corner radius end mills on aluminium parts. Offering another example of the productivity gains from ITC’s industry leading aluminium tools, Mr Nibbs says: “We used to manufacture aluminium thumb wheel adjustors in 3 minutes with our previous tooling supplier and machine, but the investment in the Haas machining centre and by introducing ITC’s 3081 radius end mill for profiling the thumb wheels, we reduced the cycle time to 45 seconds, a 75% cycle time improvement. Likewise, the 3-flute 20mm diameter 3051 Series with 0.5mm radius and the 10mm diameter 3041Series with a 3mm radius have both made similar improvements on a scope stand project whilst generating excellent surface finishes.”
Referring to this influx of ITC products, Mr Nibbs continues: “The rifles consist of over 30 major components and a huge variety of smaller parts. There is a complete range of rifle variants with 3 different stock configurations for a variety of action types, and then surface finish options and colours, the completely modular rifles consist of over 63 million different combinations - and ITC has a solution for machining every component.”
ITC Shows Steely Performance
For all the stainless steel components, Robert Nibbs has introduced ITC’s 4777 solid carbide end mill range with the 10 and 16mm diameter tools to conduct the majority of stainless profiling operations. For holemaking, the WIDIA VDS Series of drills have been implemented with resounding success in combination with the TTMM range of ITC Mini Threadmills. Commenting on this, Mr Nibbs says: “I haven’t had any ITC tools that haven’t achieved what the engineers have said they would do. As a small business owner, I don’t have time to endlessly trial new tools in the hope of achieving success, so the recommendations and results of ITC tools have been invaluable to my business. Within 12 months I have changed out the majority of tooling and ITC now supply almost 90% of our tools. This is down to the impressive results and the outstanding service, support and technical solutions that have improved the productivity of my business by at least 30% in just 12 months.”
Producing more than 50 rifles each year that are accurate up to 2,000 yards, Mr Nibbs says the rifles are instruments of true precision. “During my professional career, I spent 40 hours training every week. It is the years of training and a lifetime spent working with rifles that sets my business and product range apart and puts them in the very top echelon of the market. A precision rifle is all about balance, not weight. The balance and the re-coil action are what sets high-end rifles apart. Controlling the re-coil action and efficiently using the energy expended from the action to benefit the user is all about the application of physics. To continually develop and enhance rifles is something that requires considerable design and development effort. By introducing ITC to my business and reducing my production times, I now have more time to spend on designing and trialling new components and techniques,” concludes Mr Nibbs.