Schunk Gripper Hand Rings the NASDAQ Closing Bell
14 November 2013
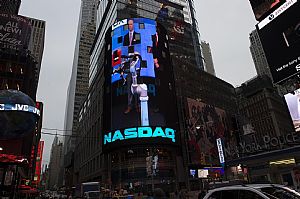
The Schunk SDH hand attached to the UR5 robot arm from Universal Robots rang the NASDAQ Closing Bell on November 12th to mark the launch of the ROBO-STOX™ Global Robotics and Automation Index ETF (Ticker Symbol: ROBO). The robotic bell ringing marks the first time a non-human performs this prestigious task.
SCHUNK has been chosen by ROBO-STOX to ring the bell along with Universal Robots to represent the rapidly developing robotics industry. At 4pm EST, the SDH 3 finger gripper from SCHUNK attached to UR5 robot arm pressed the button that activated NASDAQ’s closing bell. The bell ringing celebrates the launch of the ROBO-STOX™ Global Robotics and Automation Index ETF, the latest exchange-traded fund to begin trading through Exchange Traded Concepts’ accelerated, low-cost, private-label ETF platform.
About The “Bell Ringer” In the NASDAQ bell ringing application, the UR5 robot arm has been integrated with a three-fingered SDH gripper from SCHUNK, the toolholding, workholding and automation experts. The project was set-up with the assistance of the SCHUNK and Universal Robots’ distributor, Cross Automation. The six-axis UR5 weighs only 40lbs and handles payloads of up to 11.3lbs with reach capabilities of up to 33.5in. Repeatability of +/- .004” allows quick precision handling of even microscopically small parts. Programming happens through an intuitive 3D tablet touch screen or by simply grabbing the robot arm to demonstrate desired movement.
The SDH hand from SCHUNK enables the form-fit and force-fit gripping of a wide range of objects and can be used in the fields of service robotics and in industrial applications. Two of the three fingers can change their positions to provide a high level of flexibility, making it suitable for many different gripping scenarios. The pressure and surface are monitored by an optional tactile sensor system. This means it is possible to detect whether the object has been optimally gripped or whether a correction must be made during the gripping process. The high maximum gripping force, which conforms approximately to the force of the human hand, can be sensitively monitored by the integrated sensors and adjusted.