SCHUNK Has A New Flagship For Quick-Change Pallet Technology
18 November 2017
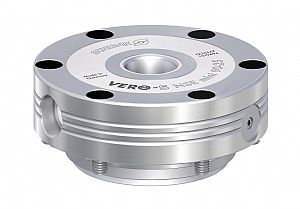
SCHUNK, the competence leader for gripping systems and clamping technology has now introduced two premium quick-change pallet modules with unique features. The VERO-S NSE3 138 quick-change pallet module and the VERO-S NSE-T3 138 tombstone module offer an optional spring-actuated cone seal that automatically locks the module's changing interface as soon as the clamping pin is lifted.
In combination with the cone seal, the quick lock prevents chips or dirt from lodging into the interface. Without changing the height, it locks the last gateway of the otherwise completely sealed modules.
Pull-down force and rigidity have been increased even further
SCHUNK has yet again boosted the performance characteristics of the VERO-S NSE3 138 as compared to previous top sellers. An enormous pull-down force of 8kN or 28kN with activated turbo function as well as increased dimensional stability for the module body have a positive impact on the rigidity of the clamping solutions. As a result, the highest tilting moments and transverse forces can be reliably absorbed when parts are clamped at the base for machining their height, for example.
Clamping and positioning of the premium modules is also carried out via a short taper with a repeat accuracy of <0.005 mm. This ensures maximum precision even in the most demanding applications. Due to the conical fitting, the clamping pins can also be joined into the modules eccentrically, making this process incredibly easy.
The actual clamping is done via spring force without requiring any external energy supply; it is form-fit and self-locking. The workpieces remain safely clamped in case of a sudden pressure drop in the air system. A pneumatic system pressure of 6 bar is sufficient to open the clamping modules.
Convenient monitoring
For maximum process reliability, both clamping slide positions "open" and "closed" can be monitored as standard using dynamic pressure. One option is a position sensor that can be used to detect locking without pins. Depending on the thread diameter of the clamping pins, holding forces of 35kN (M10), 50kN (M12) and 75kN (M16) can be achieved.
All components are made of hardened stainless steel, making them absolutely corrosion-resistant and extremely long-lasting. Special support areas facilitate cleaning and ensure a perfectly flat contact surface for the clamping devices and workpieces. The new premium modules are fully compatible with the previous VERO-S modular system, which now consists of more than 1,000 possible combinations for highly efficient workpiece clamping.